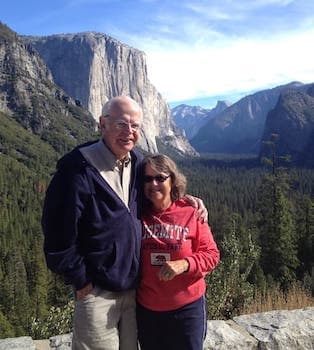
Curated with aloha by
Ted Mooney, P.E. RET
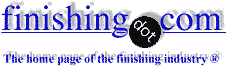
The authoritative public forum
for Metal Finishing 1989-2025
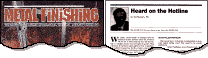
-----
Zinc vs. Phosphate screw coating?
December 11, 2009
I am a Mfg. Engineer tasked with optimizing a screw driving process on a difficult joint. I can NOT change the parts that need fastening. I CAN change the screw coating or material.
Current situation: Install an 8-32 x .312 long tri-lobular
(Tap-tite)thread rolling Zinc & wax coated screw into a(.141/.146 dia.)thru hole .156 thk. diecast aluminum base metal using a DC screw gun mounted on an ergo-arm perpendicular to the work.
Issue: Difficulties with consistently seating the screw without stripping. The prevailing (rundown) torque ramps up close to the target (seat) torque of 30 ± 5 in-lbs. Paraffin wax coated screws clog our screw feeder. Oil really helped but contaminated the parts. The water-base waxes feed better and have reduced the problem but have not eliminated it. Many rundown strategies have been tested, our current strategy gives us the best yield and have had less impact than wax.
Questions: Would a change to a Phosphate coated screw from our current Zinc coated screw reduce the friction in the joint while staying with the same wax? Does the screw coating matter if wax is present?
Any data, testing results, or experience with similar situations would be greatly appreciated.
Joe
Auto Industry production support Engineer - Milwaukee, Wisconsin, USA
Phosphate coating *may* work better. It is soft enough to somewhat push out of the way, and it's spongy nature will allow it to hold more lubricant, oil or wax. screws could be phosphate coated, dipped in oil and then spun to remove excess oil. You may have better results with manganese phosphate than with zinc.
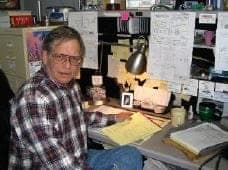
Jeffrey Holmes, CEF
Spartanburg, South Carolina
December 15, 2009
I agree with Jeffrey that a phosphate type coating would probably offer more consistency for this type of application. Specifically, I would look at a phosphate + organic sealer instead of oil or wax, in order to reduce problems with contamination, feeding during assembly, etc. Lab Oil 100WT from Heatbath is one such product. Magni B50 and Rustarest 53253 from PPG are two others. Any high quality zinc phosphate with a minimum coating weight of 10 g/m^2 should perform adequately.
Toby PadfieldAutomotive module supplier - MI, USA
January 13, 2010
Q, A, or Comment on THIS thread -or- Start a NEW Thread