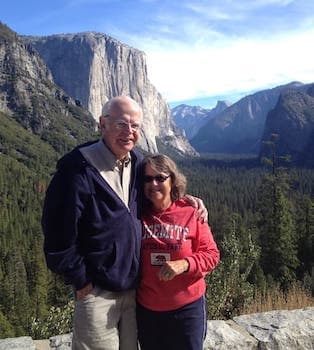
Curated with aloha by
Ted Mooney, P.E. RET
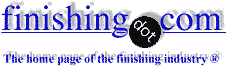
The authoritative public forum
for Metal Finishing 1989-2025
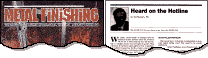
-----
CrN coated tool failure
a CrN-coated, Cr-Mo-W steel tool, used for injection molding of plastics, suffers visible, repeated failures as in the attached photo when used to work 30% glass fiber reinforced polyamide (PA6), cuasing remarkable wear loss without substrate oxidation/rusting. No significant problems occurred when the same tool was used for molding PVC, acetal resins and other plastics. The problem may be attributed to the excessive wear due to the high content of glass fibers? so a harder coating is recommended (for example TiN)?
R&D - Italy
December 10, 2009
December 18, 2009
Hi Andrea,
Craters like those are typical of situations where the substrate suffers deformation due to extreme pressures aggravated by abrasion. How deep are the damages, where are they located and what is you mold hardness?
About coatings, TiN and CrN, though very hard, are extremely thin
(around 2 microns). They work fine only when the substrate is hard enough to withstand the loads. I would recommend filling the defects with a hard alloy, preferably with an electro spark equipment (ESD) and coating the more exposed areas with Tungsten carbide. ESD is capable of filling up to 3 mm thick and coat up to 0.05 mm" thick WC.
Monterrey, NL, Mexico
The substrate is a tool steel with over 62 HRC hardness. The application (CrN on tool steel) is rather usual in molding industry and this worked well with several different plastics. We thought the issue could be the glass fiber and consequent abrasion, since analysis on section did not highlight any substrate deformation.
Andrea Vecchi- Carpi (Modena), Italy
December 29, 2009
Q, A, or Comment on THIS thread -or- Start a NEW Thread