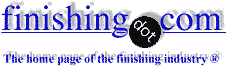
-----
Black Stain On Parts After Passivation of 420 SS
December 9, 2009
Hello,
We make bolts and screws for the aerospace and automotive industry. We have been doing passivation with a stress relieve operation for a few years. I have been in the industry for 15 years in mechanical and manufacturing engineering roles, but am neither a metallurgist or chemist.
The issue is that the parts appear to have material eaten away after passivation. As much as 0.0025" was eaten away from the surface of the finished product (0.0050" diameter), and it is pitted and scored all throughout (viewed under 40X). Here is our process:
1)Parts are cold forged from 420 SS (possible tearing and pulling of material with cutting fluid).
2)Parts are tumbled with varsol soaked cloths to break sharp edges and to somewhat clean the parts from cutting fluids (oil based varsol may not be the correct method to clean parts with cutting fluids).
3)Parts are heat treated (normally vacuum heat treat and vacuum tempered, but not necessarily done with this problem batch).
4)Parts are shot peened to remove heat scale.
5)Parts are thread rolled (threads are rolled not cut, therefore no mass amounts of parts are torn)
6)Parts are degreased in a cleaner/rust inhibitor (Gardoclean A5502 ò
"blend of organic amines, surfactants, inhibitors", 3%-6% by volume,
8.5 ò 9.5 Ph)
7)Parts are nitric passivated (to ASTM A967, screws are rotated and somewhat tumbled in order to move the solution throughout the batch within the passivation tank)
8)Parts are stress relieved at 400 F for 4 hours within 1 hour of passivation
Is there any area of my process prior to passivation that could cause this to happen? Could it be a severe flash attack of the parts as the passivation solution turned black and had black flakes (thought to be carbon) that rose to the top? One more point to add is the parts were not as bad when the parts were not 'rotated or tumbled' within the passivation tank.
Thank you for your help
Production Designer - Toronto, Ontario, Canada
December 9, 2009
Hi, Elroy. I think the parts were not sufficiently cleaned after the thread rolling. I have heard that it takes only a small amount of grease or oil to convert the strong nitric acid solution into an organic acid that causes pitting and blackening. In the long term you might consider a proprietary passivating solution in lieu of the nitric acid.
Regards,
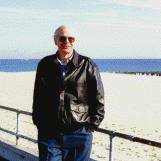
Ted Mooney, P.E.
Striving to live Aloha
finishing.com - Pine Beach, New Jersey
January 4, 2010
There are two things that could be part of the problem here. First, shot peening can sometimes fold over the surface areas to partially cover surface iron. The passivation solution may not be able to get to all of it. This can later rust, causing "rust spots". Second, it is always best to do the passivation and final rinse as the LAST process, after stress relief.
Alternative chemistry provides a solution to this problem. If you are interested in discussing this, please call us or send an email and we can provide details. Our products work very well with this alloy when used properly, even though this alloy is not a very corrosion resistance material.
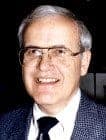

Lee Kremer
Stellar Solutions, Inc.

McHenry, Illinois
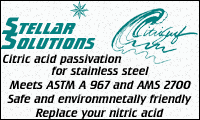

this text gets replaced with bannerText
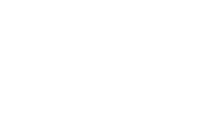
Q, A, or Comment on THIS thread -or- Start a NEW Thread