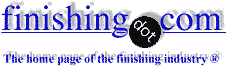
-----
Part numbering/drawing
December 7, 2009
I am responsible for the output of the design office in a medium size engineering company. All our drawings define the finished component, some with very tight tolerances. We have had a few issues recently where either within the company, or with sub-contractors, they have manufactured parts to the drawing and then plated the parts (ENP or Hard Anodising mainly) which has taken those parts outside of drawing limits. They clearly haven't taken the plating into account.
We are now being requested to supply pre plated drawings. This involves us in having to issue new 'unfinished' component part numbers and the job of calculating the pre-finished sizes.
My view is that this is determined by the manufacturing process and therefore we are not the best suited to provide these drawings. We know from empirical history that the plating thickness varies on the same component, so this task is awkward to say the least.
We already cater for the tightly toleranced, critical dimensions by having pre and post plating tables on the drawing, but never the whole drawing.
I'm interested to know what everyone else does. Is there an industry standard for instance?
Do you have such a thing as two drawings, one unplated, one plated?
We need to have drawings which define the design intent and requirement, but do you provide process information such as this as a rule from the design office?
Also, if you would supply pre-plate dimensions on a drawing, what do you do about the solid model of a part? Is the plating allowance generally taken up by the manufacturing engineers as a post processing task? Or would the design office be expected to provide a pre-plate solid model?
We have always modeled to mif limit of the finally finished part.
Many many thanks for your opinions in advance
Draughtsman - Basingstoke, England
The practice for design company is:
1. clearly states what finish process (such as mil-8625F, type III, class 1 etc) is required;
2. clearly states that all dimensions apply after finish;
3. indicates masking area if any (such as treaded holes etc).
leave other things to machining shops and platers.
- Singapore
December 8, 2009
December 9, 2009
In a perfect world you might be right, John. But as an engineer in the finishing industry for an entire career, I don't think I ever once saw such a drawing :-)
Thanks for starting what I hope will be an interesting ongoing discussion, but I think the design shop must specify the thickness of finishes because:
1. The machine shop (which is generally operating under a distinct contract from the plating/anodizing shop) will not have any idea what the correct plating thickness should be and how to allow for it; and even if they did, they cannot/ will not take responsibility for telling the plating/anodizing shop how thick the plating should be.
2. You can't leave it to the plating shop to determine plating thickness for several reasons, including the fact that plating thickness is inconsistent across the part (as Ian mentioned) and they will not know what areas need how much corrosion protection, since they won't know how the part fits the assembly or is exposed to the world.
3. Although there are occasional exceptions (like in hard chrome plating of rolls), the general truth is that plating shops don't measure anything but the thickness of their coatings, and usually just the minimum and maximum. Plating is generally a "bulk operation" -- nobody ever checks hole diameters, tapers, runout, chamfers: they just put a min/max thickness of plating on indicated areas, which is usually the whole part.
4. Even if the above problems were overcome, this would leave the designer not knowing how much virgin material is left -- information which he needs for strength, strain, and fatigue calculations. He cannot calculate based on final part dimensions because the plating must be assumed to contribute zero strength to the part. Having less substrate material and more plating could be disastrous.
Management consultants discover in almost every project that insufficient communication was the major problem. I think the designer must talk to the machine shop and the finishing shop, take everything he learns into consideration, and spell it all out in the drawing and documentation -- although I do agree that separate pre & post drawings is often overkill.
Regards,
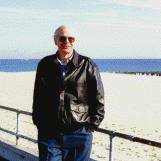
Ted Mooney, P.E.
Striving to live Aloha
finishing.com - Pine Beach, New Jersey
December 9, 2009
Ian
If only more draughtsmen would ask these questions before submitting drawings both they and the platers would save much angst.
A full response would be rather long but the good news is that you are ideally sited in Basingstoke to attend meetings of the Southern Branch of the Institute of Metal Finishing who hold regular seminars locally and you can discuss the subject with a selection of experts
There is a link on this site or try
www.uk-finishing.org.uk/index.htm
Make a start at the "Knowledge" link on the home page and also look out for Southern Branch meetings. You could also ask for a local contact - it could even be me!
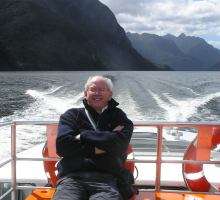
Geoff Smith
Hampshire, England
Q, A, or Comment on THIS thread -or- Start a NEW Thread