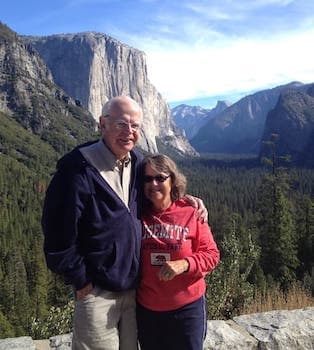
Curated with aloha by
Ted Mooney, P.E. RET
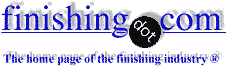
The authoritative public forum
for Metal Finishing 1989-2025
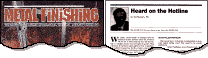
-----
Copper-nickel-chrome plating on diecast aluminum blisters and peels off
December 7, 2009
My company deals with furniture components in High pressure diecast Aluminum. These components need to be polished before being passed through a process of decorative nickel chrome plating - 4 microns Copper , 7 Microns Nickel and a flash of chrome.
We have been having problems in the quality of the chrome plated parts for 2 years now as below :
1) Plated parts when kept for a month form bubbles and eventually these bubbles burst to have the chrome film peel off.
2) Parts have process pitting or small pin head bubbles evenly spaced over the part. These parts after being kept for a month develop into larger bubbles and then result in peel off.
3) We have had a problem with the bonding of the copper plating on the part as the Aluminum Zincate solution that is used in the process to activate the part, was not of correct concentration.
Please suggest solutions for the same, does the alloy composition play an important role in these problems ? Is there a specific grade of Die casting alloy that gives improved results ? Is there a method to impregnate material in the aluminum casting to nullify the effect of porosity.
Product Development Engineer - Pilerne, Goa, India
December 13, 2009
DEAR ALOKJI
I CAN SUGGEST THE FOLLOWING STEPS TO ELIMINATE BLISTER PROBLEMS WHILE PLATING ON ALUMINIUM DIE-CAST
1. ULTRASONIC CLEANING WITH NEUTRAL LIQUID CLEANER
2. MILD ALKALINE CLEANING FOLLOWED BY RINSING & sulfurIC DIP
3. ZINCATING
4. REMOVING IN 50% NITRIC ACID FOLLOWED BY 3-4 RINSES
5. ZINCATING TILL DARK GRAY
6. 3-4 RINSES, THEN COPPER PLATING
- RAJKOT, GUJARAT, INDIA
December 16, 2009
SUNIL,
AFTER PLATING AL-DIE CAST BLISTERING BECAUSE YOU DO NOT HAVE RIGHT CYCLE AND TIME FOR EACH TANK.
SOAK TANK
RINSE,RINSE
TRIACID DIP ( SULFURIC ACID ,NITRIC ACID, AMMONIUM BIFLUORIDE - NO WATER( YOU HAVE GOOD VENTILATION AND GOV.REGULATION)
RINSE,RINSE,RINSE
ZINCATING ( ELECTROLESS ZINC)
RINSE,RINSE
50% NITRIC ACID
RINSE,RINSE,RINSE
ZINCATING
RINSE,RINSE
ELECTROLESS NICKEL
RINS,RINSE
COPPER STRIKE OR ACID COPPER
TRY THIS CYCLE BUT EACH TANK TIMING IS VERY IMPORTANT
GOOD LUCK.
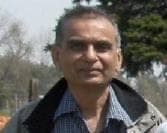
Popatbhai B. Patel
electroplating consultant - Roseville, Michigan
Hello and a Happy New Year to everyone,
how is the polishing process done and with which polishing equipment
(pastes, polishing material etc)!
Die cast must be carefully polished due of the characteristics of the material (die cast skin, structure of die cast, die cast process parameters).
Above mentioned process step from the previous response is recommendable.
Best wishes,Dominik Michalek
- Sydney, Australia
December 30, 2009
January 5, 2010
Dear All,
Thank you for the replies , I still would like to know about any specific alloys that would be the most suitable for the process.I need help to decide what the constituent materials in the alloy affect the plating and how , ex excess silicon etc. I have failed to mention that the contours of the parts are complicated and require a lot of effort for proper finishing and obtaining good nickel throwing coverage in the bath.
@ Mr Sunil : We are following the exact same process except for the ultra sonic cleaning. How important is this process ? Does it guarantee all impurities being removed from the pin holes ?
@ Mr Patel : Our vendors use a single cyanide copper tank & single nickel tank. A consultant recently suggested replacing cyanide copper with electroless nickel plating for less than 1 micron and then building the thickness with 6 microns of nickel. Please advise if you have worked with this kind of a plating process before and if the same is advisable.
@Mr Dominik : The process is rather standard, pillar mounted buffing machines, flap wheels (emery paper wheels) with various grits for good finishes & cotton wheels. Buffing soap is used as per the grit of the wheels. the parts are then cleaned with kerosene before plating pre cleaning process starts. The cleaning process includes the hot baths and tri acid dips as mentioned. My major doubt though remains on the ultra sonic cleaning and the alloy material.
Thanks once again for the replies, wishing you a very happy new year
2010
- Pilerne, Goa, India
January 4, 2010
Hi,
I would suggest to have an alkaline etch in your cleaning cycle and choose the zincating process depend upon your aluminium alloy, also the second time zincating thickness should be as low as possible, or it would be bulky to loose the bonding
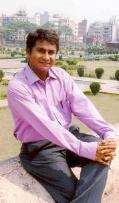
Praveen Kumar
plating process supplier
Mumbai, India
First of two simultaneous responses --
Someone a lot smarter than me may have a solution, but I do not think that kerosene will remove the "soap" that will get into the tiny spots of a cast part, even a high pressure cast. I would try a few parts that are soaked in alcohol for a few minutes to see if they still blister.
I like ultrasonics and it is a huge help on many parts. Is it a guarantee? that is probably not 100 %, but should be a big help. The initial cost of good equipment tend to be high for my budget. Since these parts are small, you could buy a cheap ultrasonic jewelry cleaner
⇦ this on
eBay
or
Amazon [affil links] and try it on a lab scale. Some that are imported into the USA are cheap compared to a few years ago.
- Navarre, Florida
January 5, 2010
Second of two simultaneous responses -- January 6, 2010
I do not have much experience in electroplating.But from your description the failure appears to be due to oozing out of gases ( or even liquids ) through the pores in the substrate. possible solutions are
1. Reduce porosity - this may be difficult
2. Increase adhesion so that pressure exerted by oozing out fluids can not peel off the copper layer.
Coating of copper by PVD could be an effective alternate. PVD is a dry process and the components are heated before coating. This results in removing some trapped gases. Adhesion of copper is better than in electroplating. However one has to pay particular attention to the geometry of the substrates as PVD processes have poor throwing power.
Bangalore Plasmatek - Bangalore Karnataka India
You forgot the etcher prior to the tri acid.
An alkaline or acidic etcher is mandatory


Sara Michaeli
Tel-Aviv-Yafo, Israel
March 3, 2010
Q, A, or Comment on THIS thread -or- Start a NEW Thread