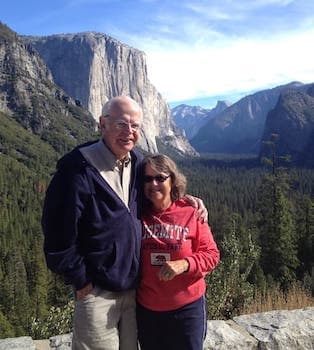
Curated with aloha by
Ted Mooney, P.E. RET
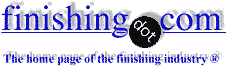
The authoritative public forum
for Metal Finishing 1989-2025
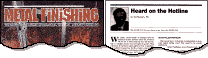
-----
Black oxide problem on selectively chrome plated component
November 26, 2009
hello everyone I'm a chemist working in an electroplating shop and I have a problem in black oxidizing a part which has an internal chromium plating.
the problem is that when this part is black oxidized,after the process it comes out from the vat with a rusty color,like red .when I tried to overcome this problem by increasing the concentration of caustic soda ⇦liquid caustic soda in bulk on
Amazon [affil link]
and sodium nitrite the result was ok but I had another problem ,which is it turns to the same rusty color when left in air for hours.
I use before black oxidizing sand blasting,alkaline degreasing,acid pickling (only sulfuric acid not hydrochloric, for not destroying chromium inside).
there is a sign which proves that the vat is working properly, is that any other part is black oxidized in this vat is very fine..i guess it may be a high carbon steel
anyway if someone can help me to find a way to black oxidize this part I'll be grateful..regarding that I'm using this formula for black oxidizing
(NaOH 700-750 gm/l , NaNO2 100-120 gm/l) at 138-142 centigrade, sometimes I make it reach 148.
thank you all
Industrialist - Cairo, Egypt
First of two simultaneous responses -- December 1, 2009
Well there are a couple things here I could suggest.
Your operating temperatures are in the ball park. 138C to 148C is usually just fine for 4140, 4350, leaded or cold rolled steel.
When you mention your red discoloration you are a little vague.
If the red coating can be wiped away and the color is fine underneath it generally means that your chemical concentration is too high or too low. Usually it means that it is too high and you are creating red oxide not black oxide. The cure for this is simple. Make certain that your bath is operating at a slow rolling boil the same as you would see if you are cooking pasta. Then add water to lower the temperature or let the water boil off to raise the temperature. Doing this will allow you to control the concentration properly. THE BATH MUST ALWAYS BE OPERATING AT A SLOW ROLLING BOIL! This is extremely important and I can not over stress it enough.
If the red color can not be wiped away it means that your solution is improperly mixed or that you are trying to blue steel that has vanadium in it.
Your mixture of (NaOH 700-750 gm/l , NaNO2 100-120 gm/l) seems a bit off. As a rule 500 grams of sodium hydroxide NaOH to 250 grams of sodium nitrate
⇦ this on
Amazon [affil link]
NaNO2 is the most commonly used mix. Lots of people change it slightly but not much. Try increasing your niters a bit. Again add water until you have a rolling boil at 138C to 148C. There is no way to measure or weigh the correct amount of water. Ball park yes, exact no!
Some steels take on a red or purple color from other elements that are added to it. Vanadium has a nasty reputation for doing this. Some people claim that by adding potassium nitrate will help solve this problem. I have tried it and many firearms makers have also tried it but in most cases the manufactures just quit using chrome vanadium steel and I just gave up on the potassium as it just didn't seem to work but you can give it a try. Some people swear up and down that it works. I just don't happen to be one of them.
If you see red forming after the material comes out of the tank I'm willing to bet it is rust. Boil the parts in fresh water after they come out of the tank and then oil all of the parts liberally and it should stop. There is no need to pickle the parts with acid before putting them in the tanks. That is a trick that is only used in stainless steel blueing. That system uses and entirely different blueing bath altogether.

Rod Henrickson
gunsmith - Edmonton, Alberta, Canada
Second of two simultaneous responses --
Ahmed,
Black oxide on its own will not offer you any corrosion protection, you need to add a supplementary treatment. What you are seeing is flash rusting, which happens very quickly. Where I work after black oxide the operators immediately de-water after rinsing, degrease and re-dewater. This is successful in 99.5% of cases in preventing the flash rust. Dependent on where the parts are to be used supplementary treatments may include things like oiling or varnish.
Aerospace - Yeovil, Somerset, UK
December 2, 2009
First of two simultaneous responses --
Rod,
NaNO2 is sodium nitrite, not nitrate. So, when you mention potassium nitrate is it also nitrite?
- Navarre, Florida
December 2, 2009
Second of two simultaneous responses --
Try uspto.gov website,there you can find at least one expired patent on new 2 step black oxide process(and many older variants of process).Hope it helps and good luck!
Goran Budija- Zagreb,Croatia
December 3, 2009
December 3, 2009
Hummm! I'll be damned James. It would seem that laziness breeds errors. I had simply copied and pasted Ahmeds mix from his posting to mine without even looking or thinking about it.
I have to admit that rite is wrong and rate is right. In other words what I wrote was right but what I copied was wrong! I have never actually used sodium nitrite NaNO2 for blueing. All I have used is sodium nitrate NaNO3.
Thinking that you may have hit the nail on the head and figured out why his bath wasn't working. I immediately called on my buddy the mad scientist who supplies me with corrosive, explosive and otherwise highly regulated powders and questionable animal and insect parts that cost me hours of paper work to procure in a method that is favorable to the Canadian gubberment!
I asked him if sodium nitrite could be used in place of sodium nitrate in blueing solutions or would it cause problems? He responded by rolling his eyes in the back of his head and simply said, "and why the hell wouldn't it work? You could use ammonium nitrate if you wanted too"! He started to get into borrowing oxygen atoms from water and temperatures but I was already walking out. I guess I learned something!
Oh, by the way potassium nitrate, KNO3 is right but I still think it's wrong! A complete waste of time to use it despite what a lot of people say.

Rod Henrickson
gunsmith - Edmonton, Alberta, Canada
Q, A, or Comment on THIS thread -or- Start a NEW Thread