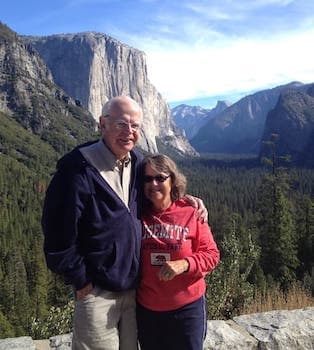
Curated with aloha by
Ted Mooney, P.E. RET
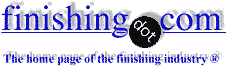
The authoritative public forum
for Metal Finishing 1989-2025
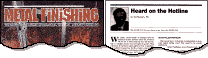
-----
Most efficient way to polish forged stainless steel bicycle lugs to a mirror finish
My Name is Mason Steele and I build steel bicycle frames in sunny San Francisco, California. It's a relatively new thing for me, but I'm loving it.
So, I just built my first frame using stainless steel lugs and accents. The use of stainless on bicycles is a relatively recent development as the same effect use to be had by chroming individual portions of the frames post-fabrication. I have read a number of different articles about polishing these lugs and cannot help but think I am missing something. Lugs are a fairly complex shape with angles that are all but impossible to reach with files and fingers.
I started polishing my lugs by filing off the inconsistencies and dimples from the initial forging process. This was only possible in more broad, flat areas. I then used emery cloth to rub out my difficult angles as I could fold the cloth into tubes that would fit along creases. Even with a week of polishing I still wasn't getting a smooth surface, and incredibly there were still dimples in the hardest to reach places. So I took a rotary tool to it with a very rough polishing wheel. This seemed to work much better, however the area I could cover before burning out each wheel was miniscule! I went through a packet of them and then moved onto sanding wheels from
180 to 240, to 360 grit. From there I hit it with a buffing wheel using ryobi's stainless compound. I wasn't getting a mirror finish. So I went back and stepped up my hand sanding using chop sticks wrapped in sandpaper (from 360 grit to 620 to 1500. Rubbing a bit of water on the lugs and hitting them with these sandpapers was quite helpful. Though it was again impossible to get into certain angled areas without destroying the paper. It's been 3 weeks of working on this particular project, and though my lugs are shiny, they aren't ripple free or mirrored.
I can't help but think there may be a much much easier way to do this using some kind of media tumbler. Can you gurus of stainless steel point me in the right direction?
Thanks,
hobbyist trying to start a new business; bike builder - San Francisco, California, USA
November 29, 2009
Not much action here. There are pics of my work at www.steelmason.wordpress.com if that helps. Was I not clear enough in my question?
I tried two new products today: An 80 grit Walter flap wheel, which took off way too much metal on my angle grinder, and a "medium" grit surface conditioning disc that worked very well but could not get into the corners...
- San Francisco, California
December 18, 2009
December 23, 2009
Well to be quite honest I looked at your post some time ago and just laughed because I didn't know what the hell you were trying to describe. After seeing the photos it's so simple it's laughable. I do just that sort of polishing all the time and it's no big deal. The good old boys at Smith & Wesson can polish a stainless handgun to a mirror finish in under an hour and would do the same with the joints that you glue your bike frames together with.
You are going to have to go out and buy yourself a 1.5 to 2 HP 8 inch buffer or bench grinder and about a dozen 8 inch by 3/4 HARD FELT wheels. You will also have to get cutting compounds in grits 320,
400, 600 and mirror weights. I use Polish-O-Ray and Matchless and both of these companies have very helpful tech staff.
The trick is to custom shape the wheels while they are running with a wood rasp so that they fit into all the nooks and crannys. Some of the wheels will look flat others rounded while still others will be near knife edge. Once a wheel is coated with a certain grit it must be dedicated to that grit till you toss it away. NEVER MIX GRITS! Work from coarsest to finest and re-coat your wheels often it's the grit that cuts not the felt. Getting a finish with no ripples is not that hard its just common sense and LOTS of practice! Lots of brainiacks try to find ways to cheat by using flapper wheels, grit impregnated wheels or even the 3M wheels and although those wheels are great for some applications I can tell you right here and now that they will not work for your application.
Welding the joints to the pipes may take a bit of re-thinking though. I believe most of those welds are done with furnace brazing or silver solder in some of the custom shops. Once you have welded the joints to the pipes it will be very difficult if not impossible to re-polish the joints to any degree so you will have to find a low temp solder with which to do the welds. Silver or brazing will carburize your parts and spoil your polish job. Common lead-tin won't be strong enough but there are some specialty solders that will work. I use just such a solder for high powered rifle sites and shotgun ribs called force-44. It's very expensive but I'm certain you can find an equivalent that's much cheaper if you go to some welding shops.
Learn to enjoy dirt, grit, burned fingers and parts flying all over your shop cause its gonna be a learning curve!

Rod Henrickson
gunsmith - Edmonton, Alberta, Canada
Q, A, or Comment on THIS thread -or- Start a NEW Thread