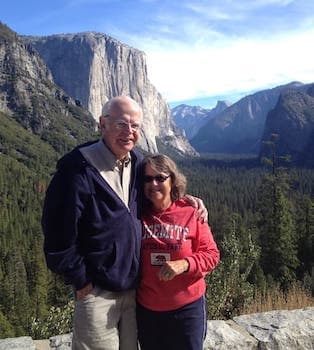
Curated with aloha by
Ted Mooney, P.E. RET
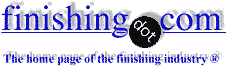
The authoritative public forum
for Metal Finishing 1989-2025
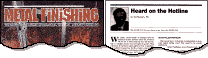
-----
Floating dross after a holiday
November 18, 2009
What is the reason of floating dross?Especially this case is shown after week holiday..
Now Ni content is at about 450 ppm. Al is 100 ppm, Fe is 250 ppm. Pb is 200 ppm Sn is 180 ppm.
our kettle dimensions are 7x1,5x2,5 (depth) and we use 99,995% purity zinc and always depth is at about 2,4m.
Flux baumé is 30 (double salt),however iron is at about 12 g/l and pH is 1.In a month,we will install flux regeneration system..
We have in trouble especially for <3 mm.and high surface area
What is your comments?
Kindly Regards
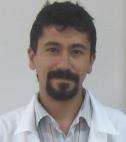
Hakan Esen, Material Engineer(BSc.)
galvanizing plant manager - Bursa, Turkey
Fe in flux is too high, causing Fe to get to the zinc and form fine dross particles which don't sink.
Adding Pb to the surface spreading it round the whole surface area while it melts will increase dross density causing it to sink to bottom where it can be removed from.
Otherwise don't allow any holidays !
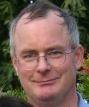
Geoff Crowley
Crithwood Ltd.
Westfield, Scotland, UK
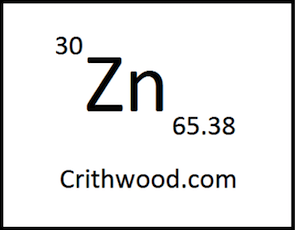
November 20, 2009
Hakan
If you want to be "lead free" you cannot add the lead as suggested by Geoff. Indeed this method, via my lead alloying device works. I had about 10 users of my lead alloying device, but the environmental picture is changing rapidly and I expect lead-free galvanizing will be required in the not too distant future.
There are many other methods that are claimed to work, both on floating dross and pimple (dross or ash) avoidance. The truth is that the root cause must be determined so as to use the proper solution.
Floating dross was a big problem in North America, especially on Monday mornings (after the Saturday and Sunday weekend "holidays"). My clients using IQM no longer have this problem. I am not able to disclose publicly how the floating dross problem has been eliminated using IQM.
Regards,
Galvanizing Consultant - Hot Springs, South Dakota, USA
November 23, 2009
Lead and Chrome are in a similar category.
They have their place and can be used effectively, but environmental pressure will reduce their use.
But until someone comes up with a cost effective alternative that's proven to reliably work, then they will be found in use in most countries.
Europe is moving towards low lead (as opposed to lead free) galvanizing.
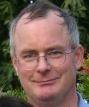
Geoff Crowley
Crithwood Ltd.
Westfield, Scotland, UK
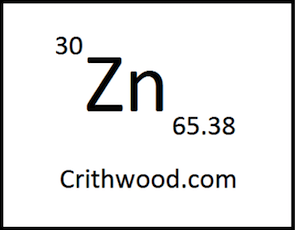
November 24, 2009
Sirs:
After thinking more about the floating dross after non-use of the kettle, I wondered if bismuth could also drop the dross down. Bismuth at about 0.1% is used in North America to take the place of lead and most reports are that it reduces zinc usage (although the cost is high and should NOT be used with kettles having a lead heel, because bismuth is 75 times more soluble in lead than zinc).
In the USA, lead is being be phased-out state-by-state over time with lead allowable concentration being more severely limited each year. My experience is that at 0.5% lead in zinc gives worse galvanizing than lead free galvanizing.
Tin in the zinc above about 0.3% can cause stressed steel to crack. Thus the use of tin to reduce zinc usage can be a major problem.
Regards,
Galvanizing Consultant - Hot Springs, South Dakota, USA
November 25, 2009
We tried Bismuth for a year or so.
It had no detectable effect on dross formation, but it did make the dross difficult to remove from the kettle due to high fluidity.
It showed a barely detectable difference in fluidity meaning smaller "spikes" (stalactites), but was not worth the high cost.
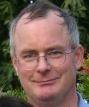
Geoff Crowley
Crithwood Ltd.
Westfield, Scotland, UK
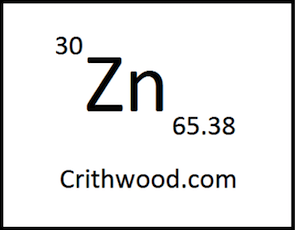
November 30, 2009
December 1, 2009
Hakan,
Your aluminum at 0.01% is too high. The max. aluminum for general galvanizing is 0.007% and is found in many places in the "old" literature and that value "the magic number" is correct. Above 0.007% aluminum, the aluminum reacts with the chloride in the flux forming aluminum chloride and much white smoke in the galvanizing plant.
Obviously you are using the European hot dip galvanizing method: e.g. high baumé,' double salt and likely warm flux. In North America most galvanizers (except those with European technology use low baumé flux (e.g. about 14 deg. baumé and hot; 71C). Each method has its +'s and -'s.
At pH 1 in the flux you are dissolving the steel product in the flux and the iron+2 is increasing internally. Once you get your flux purification machine, I expect it will immediately add ammonium hydroxide (aqua ammonia) up to pH 5 and then peroxide will likely be added. You have over 1% iron+2 in your flux so a large quantity of iron(+3)hydroxide will be formed. It will look like tomato soup. I hope you have a filter press to deal with this soup.
In addition the raising of the pH of the flux will make it weaker and likely you will have some galvanizing issues at the kettle.
I do not expect your floating dross to be reduced. It would be nice if you posted your results, both of the use of the flux purification machine and the possible reduction of the floating dross.
Regards,
Galvanizing Consultant - Hot Springs, South Dakota, USA
Q, A, or Comment on THIS thread -or- Start a NEW Thread