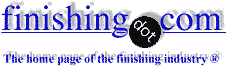
-----
Failure Analysis of cracked crimper roller
November 12, 2009
A Crimper roller, of size 300 mm dia. by 1000mm long, made of AISI
420B (hardened and ground smooth) developed cracks on its roller sides. Hydrogen cracking is the finding in a failure analysis. Can any one help me to understand the following.
1. How Hydrogen get into the grain boundary?
2. At what temperature the failure can occur?
3. How to detect defect prior to failure?
How to prevent failure?
Regards
VKM VermaCustomer - India
I find it interesting that so many people are willing to blame cracking on hydrogen embrittlement.
I will suspect overly aggressive machining or improper heat treatment as more probable.
How did the analyst determine that it was caused by hydrogen embrittlement? It requires a rather sophisticated analysis to determine it.
Was this part ever pickled or plated? If not, it is not H2 embrittlement.
H2 embrittlement does follow grain boundaries, Your part shows the cracking is between holes. The grain of most metals follows a straight line rather than a circular pattern.
- Navarre, Florida
November 16, 2009
I'm with James in being suspicious of H2 embrittlement.
Ok, it's fairly high strength steel and therefore could be prone, but if not pickled or plated then it's not H2 embrittlement.
Grinding can cause cracking if cooling is not controlled properly, and service conditions can propagate these cracks, possibly exacerbated by overtightening of the fasteners; is there a specified torque setting?
You need to determine the hardness and compare with the specified requirement or design spec.
Regards and Good Luck
Ship Repair - Plymouth, UK
November 19, 2009
Q, A, or Comment on THIS thread -or- Start a NEW Thread