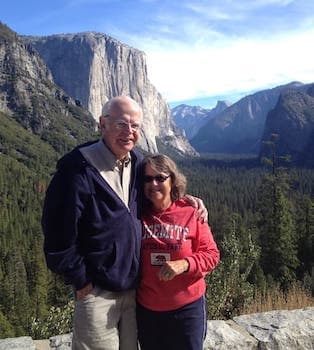
Curated with aloha by
Ted Mooney, P.E. RET
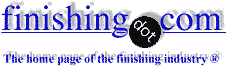
The authoritative public forum
for Metal Finishing 1989-2025
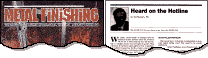
-----
"Time Window" for Sealing after Anodize
November 9, 2009
Hello Everyone,
We utilize a lot of anodized parts for an aerospace application. One specific part is anodized per
MIL-A-8625 / MIL-PRF-8625
[⇦ this spec on DLA], Ty III, Cl I
(hard, non-dyed). We were recently made aware that a recent "lot" of parts was not sealed. The parts have been sitting in stock for a few weeks now and I'm wondering if they can be sealed as is or do they have to be stripped, re-anodized and then sealed. Is there a specific
"window" to seal the part after it has been anodized? Corrosion resistance is important for the application. Note that the parts are stored in an environmentally controlled stockroom. Thank you for any input on this matter.
Regards,
Mike
customer - Wall Twp., NJ, USA
First of two simultaneous responses --
Normally Type III hardcoat is NOT sealed because the hydrated aluminum oxide molecule is softer than the non hydrated molecule. If you have been in air for "weeks" then you cannot reliably seal the hard coat. Once it is dry you cannot apply a reliable hydrated oxide (seal).
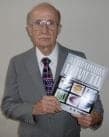
Robert H Probert
Robert H Probert Technical Services

Garner, North Carolina
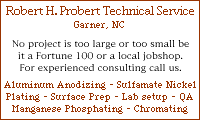
November 10, 2009
Second of two simultaneous responses -- November 11, 2009
Mike,
The last thing I would do is strip the parts, you may have some serious dimensional issues if you do.
I don't personally know what the window for sealing of hard anodising is, I've always sealed within a couple of hours of anodising. If you wish to seal after a period of days may I suggest you use a re-activation step first. I have used phosphoric acid with a touch of HF successfully on chromic acid anodising and I see no reason why it shouldn't work with hard anodising. All this does is gently surface etch the anodising, opening up the pores to allow the sealing to take. This is all theoretical as I have never actually tried this, but there is no reason why it should not work.
Aerospace - Yeovil, Somerset, UK
You do not want to seal Type III class I - it will only soften the coating -
Bob BramsonB&M Finishers / Prismatic Stainless Steel

Kenilworth, New Jersey
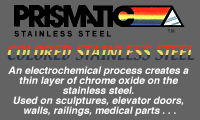
November 13, 2009
First of two simultaneous responses -- November 14, 2009
Mike
Similar to Brian Terry's approach would be to immerse the parts in a mild nitric acid solution, similar to that used prior to dyeing. ~5% v/v for 5-10 minutes. Observe for a water break, less the parts were handled with bare hands during packaging.
Consider sacrificing a good part and a delay-sealed part to a salt spray test, a mild caustic strip rate comparison, or the acid dissolution test (sorry I do not have the ASTM spec handy).
- Colorado Springs, Colorado
Second of two simultaneous responses --
Normally, you should do the sealing as soon as possilbe, because doing so you could get anti-corrosion with minimal sealing time (1hr hot DI seal/1mil, normally); however, you still could get the same anti-corrosion with increased sealing time if parts are left for weeks. I have personally tested sealing 6hrs/2 mil Hot DI seal for parts left 4 weeks which still meet spec. for anti-corrosion requirement.
John Hu- Singapore
November 15, 2009

Q, A, or Comment on THIS thread -or- Start a NEW Thread