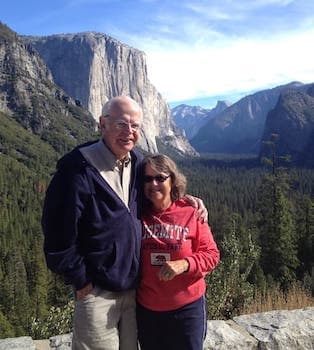
Curated with aloha by
Ted Mooney, P.E. RET
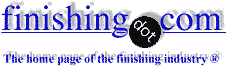
The authoritative public forum
for Metal Finishing 1989-2025
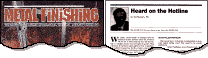
-----
Corrosion problems on externally tested Alocrom test pieces
We have recently begun a relationship with a new potential customer for Alocrom 1200 work. Part of the qualification process requires the submission of 2024 test panels for corrosion testing which have been failing (quite drastically) at the customer's own site.
Our own test panels consistently pass (tested in house).
The test panels are thoroughly rinsed in shop temperature DI water post Alocrom and left to air dry on the jig for 24 hours. The panels are then wrapped in acid-free tissue paper before being boxed and couriered to our customer.
Can anyone suggest why there is such a drastic difference in result between the two labs when processing solutions, conditions test piece batch etc. are all identical? Is there a 'better' way to pack and transport the test pieces?
Plating shop lab manager - Thrupp, Gloucestershire, Great Britain
November 10, 2009
Hi, Neil. I think the first thing to do is ask the customer to immediately courier back a few of the test panels without even opening them. Then you will start with the knowledge of whether the problem is differing test procedure, or something that happens in packaging and shipment.
Regards,
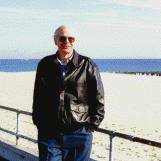
Ted Mooney, P.E.
Striving to live Aloha
finishing.com - Pine Beach, New Jersey
November 10, 2009
First of three simultaneous responses --
Are you drying your test panels on the same rack for the same length of time. Are the panels that are being shipped handled with clean white gloves.
I would want to get a set of failed panels back to see how they are failing.I would like to be assured that the customer is also handling the panels with clean white gloves.
If the spots are larger than medium pits with some trailing streaks, I will suspect that they are not being handled correctly at some point.
My wife used a common hand lotion that could strip the chem film in a matter of minutes, so anything is possible.
Ted had a very good suggestion.
- Navarre, Florida
November 10, 2009
Second of three simultaneous responses --
Quality of water or salt purity used in chamber testing may affect final results. So you might check with them to compare.
Terry Tomt- Auburn, Washington, USA
November 11, 2009
Third of three simultaneous responses --
Neil,
This is a phenomenon that I have seen before. There seems to have been two main factors with the panels. The first was packaging and the second was the delay in testing.
Try sealing the test pieces in plastic bags after wrapping in paper. This would cut down on any potential dehydration.
Do you know what the delay is between when you process the test pieces and when they are corrosion tested? I have found that delays, which in some cases has amounted to a couple of months, has had a huge effect on results.
There may also be an issue with corrosivity of the cabinet. There is a test in ISO 9227 for corrosivity, if your customer is carrying out this test it would be useful for you to get their results, do the test yourself and compare the results.
I would also suggest that you try sending some panels to an independent test lab and see if they match your results or those of your new customer. This at least gives you an independent opinion on results.
aerospace - Yeovil, Somerset, UK
November 11, 2009
Q, A, or Comment on THIS thread -or- Start a NEW Thread