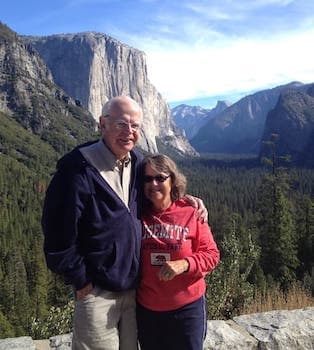
Curated with aloha by
Ted Mooney, P.E. RET
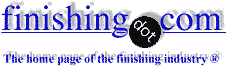
The authoritative public forum
for Metal Finishing 1989-2025
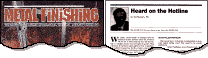
-----
Austenitic SS Passivation Problems
My company manufactures a variety of SS as well as other metallic devices. Recently had an issue with 304 SS corroding inside a poly bag in a relatively short amount of time. More than typical brown surface rust, this actually "grew" out of the SS. Found chloride present by SEM EDX at more than 10%. Further investigation with Auger Electron Spectroscopy found Cr:Fe ratio of subsequent passivated products to be at 0.7:1.0 at absolute best, or otherwise, no passivation layer at all. We follow industry standards which I've followed equally at other employers. I've never had a problem and honestly, I've never actually tested for passivation layer beyond copper sulphate. Consequently, all our parts are passing copper sulphate
⇦ this on
eBay or
Amazon [affil links] which now has me feeling a little less enamored with that test.
Recently tried a bunch of different test variables, excluding pickling, adding chromic acid, passivating longer, nitric 4, 70% nitric, etc. Awaiting test results from Auger. I've read up that EP is really the best, however, can anyone else confirm what might be expected as the limitation of Cr:Fe ratio from a nitric passivation?
I'm figuring we either have a passivation bath issue, or initial cleaning or rinsing. There's really not much else to it. I'm also testing for the possibility of sensitized SS which I've read might produce this type of corrosion problem. We bright annealed parts and put them through normal process.
Would appreciate any insight.
Regards,
Engineering - Medway, Massachusetts
November 9, 2009
Hi, Michael. I don't think that I would have come to the conclusion that the passivation was deficient from the fact that the parts rusted in these poly bags. I would have wanted to investigate why this packaging/shipping method seemed to cause this problem.
Although there have been claims for chromium enrichment through passivation, I'm not sure how much of that is sales pap vs. science, and I don't think that is the "heart" of what passivation is about. I think it's about the removal of iron particles from the surface. If the parts continue to pass the copper sulphate test, I would call them passivated and try to find out what was strange about the shipping.
Regards,
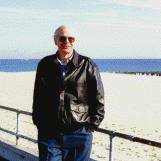
Ted Mooney, P.E.
Striving to live Aloha
finishing.com - Pine Beach, New Jersey
November 9, 2009
First of two simultaneous responses --
The high chloride would make me think that the parts were rinsed with tap water or softened water rather than DI or RO quality water.
That said, it still takes some surface iron to initiate 304 rust in most cases.
You might want to look at the Ferroxyl test which is extremely sensitive to iron. It is too sensitive for most uses, but it might help you to locate the real problem as Ted says.
Are you aware that a lot of plastic bags actually promote rust. I think that it is because of outgassing of vinyl chloride gas (or something similar).While you do not need electronic grade packing material, a better quality bag would probably be of a large help to you.
- Navarre, Florida
November 10, 2009
Second of two simultaneous responses -- November 11, 2009
Thank you Ted,
The poly bags are used on tens of thousands of shipments over the past few decades and we've not had problems with it prior to this event. Consequently, other companies I've worked for used the same bags and again without issue.
Parts have failed an ASTM
ASTM F1089 -02. After boiling for 1/2hr setting to cool for 3hrs and air drying, rust was found.
I've filed "V" notches into 300 & 400 series SS with a steel file and dipped them into copper sulphate without treatment and they pass copper sulphate, so I'm not enamored with that test.
I've found that virgin parts, when wiped after cleaning, have black smut that will wipe off them. I've let the parts soak for 2 hrs between two separate tanks. It seems that drawing compounds may be somewhat impregnated into the surface such that they just continue leeching out. Will try solvent and vapor degreasing today.
It is my understanding that the smut will prevent the nitric acid from performing it's duty at burning off free iron, because it is hidden beneath smut.
Ted or anyone have similar experiences?
Engineering - Medway, Massachusetts
First of two simultaneous responses --
Chlorides are very damaging to stainless. If you are finding chloride contamination that may be contributing to your problem.
The copper sulphate test is an odd beast at times, most austenitic grades can pass it even without a passivation treatment unless there is gross surface iron contamination. I have had many customers attempt and fail at contaminating the surface by hand just to see what a failure looks like.
Ted: The term "chromium enrichment" may not be the best thing to call it, by virtue of the iron removal you do end up with a surface layer that is higher in chromium (and nickel in the case of Austenitic grades) percentage content than the bulk alloy. One might more properly say "iron depleted" surface, though since the corrosion protection comes from the chromium it is sometimes desirous to emphasize the role of the chromium.
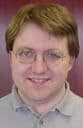
Ray Kremer
Stellar Solutions, Inc.

McHenry, Illinois
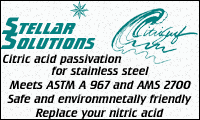
November 17, 2009
Second of two simultaneous responses --
This is a complicated situation. I am not going to say that the steel is not up to par, but the industry has been facing a situation of poor quality stainless steel, especially 304. We are called on to solve these problems constantly. 10 years ago we did not have these problems. The steel may or may not meet the assay requirements, but there is often a lot of inclusions and other foreign elements in the steel.
The Cr:Fe ratio on the surface and down to 25-30 Angstroms on the surface will greatly affect how corrosion resistant the parts are. With 304ss you should be at least at 2:1 with nitric passivation and higher with other passivation methods. 0.7:1 is certainly not high enough. If you use EP in conjunction with passivation you should get very excellent results.
It sounds to me like the chloride is the culprit here. Chloride concentrations that high will DEFINITELY cause rusting of 304ss. What is the source of the chlorides? Get rid of the chlorides and you should get rid of the problem unless the steel is really bad. Since you have not had a problem in the past, the bags should be okay unless the bag mfr has changed them. Ask them what the chloride content in the bags is.
Call us if you need help.
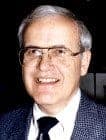

Lee Kremer
Stellar Solutions, Inc.

McHenry, Illinois
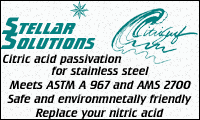
November 18, 2009
Q, A, or Comment on THIS thread -or- Start a NEW Thread