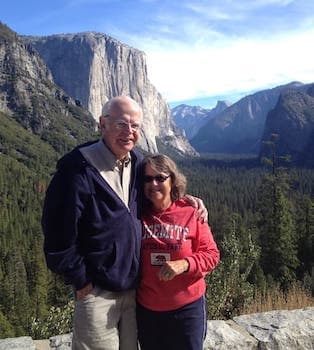
Curated with aloha by
Ted Mooney, P.E. RET
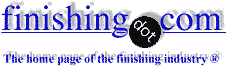
The authoritative public forum
for Metal Finishing 1989-2025
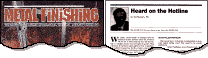
-----
Passivation / Electropolishing : Can we describe the atomic mechanisms/chemistry in detail here?
November 4, 2009
Hello,
I'm a materials engineer working in the medical device sector. When I first started working with metallic implants 5 years ago I was charged with setting up an electropolishing process, passivation follow up process, as well as corrosion testing of the finished parts. I recall at the time doing massive amounts of research online trying to understand what was actually happening during these processes on an atomic level. Eventually my searches led me to this forum where I found the most detailed and informative responses in archived threads. The general ideas I took away from my research at the time were:
-Electropolishing is a pretty well understood process wherein a viscous film is formed on the surface of the part when given an anodic potential. The film is thinner at microscopic peaks and thicker at microscopic valleys which enables preferential diffusion of the peaks, resulting in a net smoothing effect. Although agitation is typically used during the process, the film will typically be drug out of the tank and must be rinsed away, after which an robust oxide layer forms on the surface when exposed to air [not sure if the oxide layer actually forms in the bath (?) ]
-Passivation (I'll confine the discussion to nitric acid) is used to remove any free iron or other concentrated elements from the surface that may be left during electropolishing. When the part is removed from the nitric acid bath the oxide layer forms from contact with air and will be even more robust than if EP only...assuming the possibility of free iron.
Now to my questions:
1) Is my general recollection of how these processes work accurate? If not, where am I off?
2) How come when I now search these forums I see many threads saying that there is no engineering reason for passivation? From my personal experience, both the rest potential and breakdown potential of EP + Passivated parts is improved compared to EP alone. These results were observed in cyclic polarization curves that may not be relevant in most of the industrial applications on cited on this forum...
3) I'm now at a new company and not directly responsible for the EP/Passivate processing. The manufacturing engineers are claiming improved surface quality when they passivate BEFORE EP. This struck me as odd because I'm sure the passivated surface is removed completely by the EP process BUT could this make sense if the passivation process is acting like a pickling where the benefit would be as a surface prep before EP?
Am I way off here?
Materials Engineer - Medical Device - Temecula, California, USA
November 5, 2009
Anytime that you do 2 different surface improvements, you will have a tiny bit better product.
As a scarred warrior of difference of opinions within a company, strongly consider that it will only make a tiny difference in the final product. If they are happy with doing it backwards, smile and go along with it.
Properly operated EP is a great process by itself.
- Navarre, Florida
First of two simultaneous responses -- November 17, 2009
1. Yes, more or less you are correct. citric acid passivation works the same way as nitric does, and of course passivation can be done without EP.
2. The need for passivation depends on the grade of stainless used and what kind of environment it will be placed in. There may be "no engineering reason for passivation" in certain instances, but that's not valid as a generality.
3. You are correct, it should be EP then passivation, though any needed surface prep before the EP should be done. That wouldn't really be passivation then, it would be pickling as you said. Many people still use the terms interchangeably, especially since nitric baths are used for both.
Either EP or passivation are good for corrosion resistance, both together is even better.
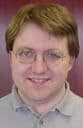
Ray Kremer
Stellar Solutions, Inc.

McHenry, Illinois
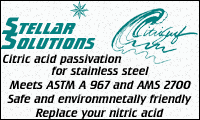
Second of two simultaneous responses --
Your comments about electropolishing are broadly correct, the only point I would raise is that when the workpiece is removed from the electroplishing bath, it may become covered in another layer besides oxides, namely phosphates or any other anions present in the electropolishing solution. The purpose of electropolishing is to create an equipotential over the metal surface; this inhibits the creation of corrosion cells as no Redox reaction can take place. Obviously in metals such as stainless steel, this is not possible, but nevertheless, the electropolishing process does still reduce the possibility of any local cells being created.
Regarding the use of passivation prior to electropolishing - The passivation will help reduce corrosion prior to electropolishing, but it will certainly be of no use after electropolishing - it will have been removed or damaged. In fact, passivation may even be detrimental to the passivation process and it will inhibit the electrochemical reactions form taking place, so there will be uneven and incomplete electropolishing. Post electropolishing passivation would be beneficial, but it may result in the surface becoming duller, which is possibly not what is wanted.
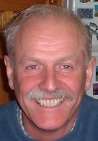
Trevor Crichton
R&D practical scientist
Chesham, Bucks, UK
November 18, 2009
Q, A, or Comment on THIS thread -or- Start a NEW Thread