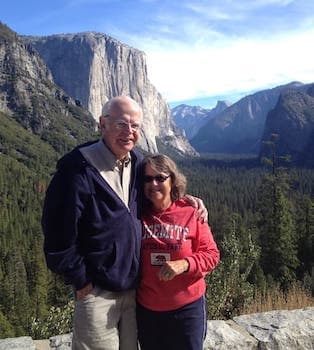
Curated with aloha by
Ted Mooney, P.E. RET
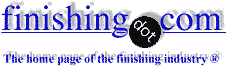
The authoritative public forum
for Metal Finishing 1989-2025
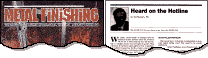
-----
Tin/Silver Plating Solution: Acidic Vs. Basic
October 29, 2009
Hello, my name is Kristen Krcma. I have been assigned the company tin/silver solder project and needless to say I am a little out of my element (or elements as the case may be). I am just trying to get a good understanding of the plating solution.
Here is my question: Should the tin/silver electroplating solution be acidic or basic?
Here is what I have found:
MSA(aq) helps keep dissolved tin in the stannous oxidation state.
MSA plating chemistries can provide control of the stresses present in the Sn plat-
ing and result in plating less prone to whisker growth.
MSA solution plating is a more controllable process and obtains high quality tin base coatings of consistent chemical composition.
I found one reference stating a pH of 5-10 was desirable (no info on why though).
Background/my concerns:
We hope to plate on a copper or nickel substrate.
Using a basic solution may be desirable to decrease hydrogen evolution.
Using an acidic solution may be desirable to avoid hydroxide precipitation of the tin or silver.
So what do you think? Which would you use/try first? Are there additional concerns that I should look in to? Are my concerns legitimate? Do you have any suggestions about other chemicals to use besides MSA for the solution "starter"?
I would really enjoy and appreciate any input (even if you call me names and suggest I go read a chemistry book).
Thank you and have a great day,
R&D Laboratory Technician - Moses Lake, Washington, US
November 2, 2009
Kristen
I am sure that none of our contributors would call you names!
You do, however, appear to have been given a rather difficult task.
If your company intends to carry out the plating, you are looking to buy into a complex technology that cannot be covered in a brief web reply. (think in terms of a couple of years training starting from a technical background start)
If, on the other hand the plan is to sub-contract the work, very few of your concerns are problems to you. Speak to local platers.
On your specific question - Bright Acid Tin is probably the easiest to control. Stannate (alkaline) tin requires special control of the anodes unless it is in continuous use. I have no idea what MSA is.
Almost all silver plating is from a cyanide solution. Non cyanide solutions are rare and difficult to control.
If you are intending to set up a plating line do not forget the effluent treatment requirements, environmental legislation etc,
Hope this helps
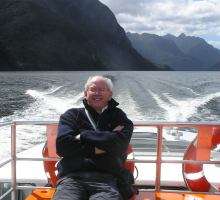
Geoff Smith
Hampshire, England
----
Ed. note: MSA is methane sulfonic acid
Mr. Geoff Smith,
Thank you for your response.
Just to add a little more information. Luckily, my only task is to develop a lead-free solder solution utilizing beaker scale testing. We then have another company test the chemical with their production-scale supplies/set-up.
I was also thinking that Bright Acid Tin chemistry would be the easiest place to start (I just didn't want to sway any opinions). I couldn't find any up-side to using an alkaline solution; do you happen to know of any? Like the editor note states MSA is methane sulfonic acid (sorry for not stating that in the original post).
We were hoping to stay away from cyanide, but like you said it is difficult to control the plating without it.
Thank you again. Your response is really helpful.
- Moses Lake, Washington, US
November 3, 2009
Either can work well. Avoid bright finishes as they contain organics that make follow on soldering difficult as it ages. Specify a matte finish. The drop dead time on easy soldering varies from a week to a month for bright plating that we have done.
James Watts- Navarre, Florida
November 4, 2009
November 6, 2009
Kristen
Thanks for the additional information.
If you are looking for a solderable surface, bright acid tin is simple, cheap and long established technology. The most effective
(necessary) organic additives are patented.
Stannate (alkaline) tin is usually plated without additives but requires control of the coating that forms on the anodes.
If you are trying to develop a tin/silver alloy, life becomes much more difficult.
Acid tin is no good as silver sulphate is not soluble, same with the stannate bath and silver hydroxides.
Methyl sulphonates were introduced as a safer and environmentally friendly (both questionable) alternative to the fluoborate standard tin/lead bath. Silver methyl sulphonate may be a possibility but becomes a major project.
If you are new to alloy plating, I suggest that you start by reading
"Modern Electroplating" by Lowenheim
[on
AbeBooks,
eBay, or
Amazon affil links]
and move on to
"Electrodeposition of Alloys" by Abner Brenner ⇦[this on
Amazon,
eBay, &
AbeBooks affil links]
I am still not certain what you are trying to achieve. Current lead free solders simply require a solderable substrate like tin. If you are aiming for a deposited solder, you need to start by selecting a target alloy with acceptable melting point, adhesion, strength, compatible fluxes, etc. and then try to develop a plateable version.
But I am still not convinced that there is not a simpler way.
Hope this helps
Geoff
PS Tin whiskers are rarely a real concern and are suppressed by even a small alloying metal, but check on allotropy of tin if it is expected to operate at any extreme (aerospace or military) operating temperatures.
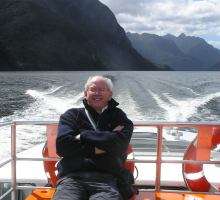
Geoff Smith
Hampshire, England
adv.: Supplier of Copper Anodes, Nickel Anodes, Bismuth Metal, & Other Metal Products for Industry & The Arts
Q, A, or Comment on THIS thread -or- Start a NEW Thread