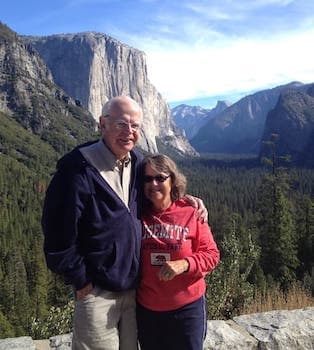
Curated with aloha by
Ted Mooney, P.E. RET
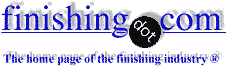
The authoritative public forum
for Metal Finishing 1989-2025
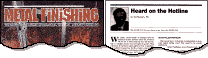
-----
Low(er) temperature black oxide for 300 series SS
Hello,
I need to set up a black oxide process to meet the requirements of MIL-DTL-13924
[⇦ this spec on DLA] class 4. Please let me know if there is a process that runs well below the typical 290 F range. I know it exists for mild steel, but is there such a process for stainless?
Thanks,
Plating Engineer - Grand Junction, Colorado
October 26, 2009
First of two simultaneous responses --
True there is a black coating that is sold as low temp black oxide, but it is not the same. It is normally a selenium product. It is inferior to a hot caustic true black oxide in most respects. It, however, good enough for many uses. I have used both.
For the straight word, go to OEM's for the low temp product to see if there is a suitable material for SS.
- Navarre, Florida
October 27, 2009
Second of two simultaneous responses --
To my knowledge no one sells the old sodium cyanide salts or the mercury base bluing solutions anymore and for good reason. Those were much the same as standard bluing salts and operate at 300 degrees. The new stainless salts are much different and operate at around 250 degrees Fahrenheit. But be forewarned. Although the new stuff may not kill you, it's a multiple step process which not only involves the regular cleaning, rinsing and bluing but it must also be activated with hydrochloric acid prior to going in the bluing tank. On top of that it's fussy as hell to use and often takes a bit of witchcraft to get good results. It is decidedly not a dip and ship process no mater what the manufacturer may tell you. I used it for about ten years and finally gave up in disgust. Mind you I blue firearms and they HAVE TO BE PERFECT or the customers freak out. Good luck!

Rod Henrickson
gunsmith - Edmonton, Alberta, Canada
October 27, 2009
November 12, 2009
Try old Naylors solution: 1 lit H2SO4(d.1,55)
13 gr Na2Cr2O7
18-25 °C temp.
5-10 minutes immersion
sodium thiosulphate
⇦ this on
eBay
or
Amazon [affil links]
based solution can be used too:
1 lit water
50 ml H2SO4(d.1,84)
200 gr Na2S2O3
30 °C temp.
(according to Hndbuch der Galvanotechnik, Muenchen 1966.)
Hope it helps and good luck!
- Cerovski vrh Croatia
Q, A, or Comment on THIS thread -or- Start a NEW Thread