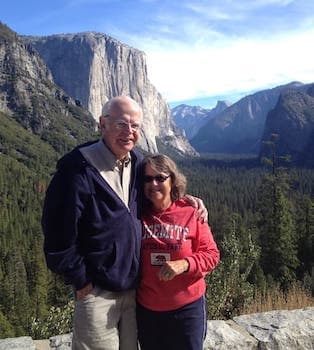
Curated with aloha by
Ted Mooney, P.E. RET
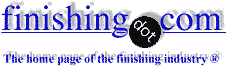
The authoritative public forum
for Metal Finishing 1989-2025
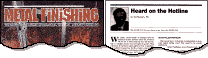
-----
416 SS, Images and data for salt spray (fog) testing
October 16, 2009
Hello:
I sell industrial hdwe & fastener in So New England.
I get frequent questions from engineers designing new and upgraded products for outdoor application most often requiring SS or aluminum products mixed in the application.
This poses several issues to the ocean atmosphere here in New England.
This current customer request is all SS construction.
My customer is upgrading an exterior metal product with a spring loaded screw machine part.
The mfr is calling out a 416 SS w/ Blk Nitride finish(for appearance)for this part and as the product is installed along the coast line my customer has been opting for 300 series SS construction for all the other parts for their product upgrade.
The concern is about the longevity of the part in the ocean atmosphere as it can not display "rust" / corrosion for several years and has a product life of 20 years.
As these are small parts on a larger unit mounted up on a post (8-12" high they will not get frequent inspection but on the occasion of maintenance to the unit they need to appear presentably and work freely when turned.
The customer is asking for both performance ratings/results and an image of the material after salt testing to show what the discoloration can look like.
Can I get help in resources for this data.
Thank you
industrial hardware sales - West Hartford, Connecticut
For decorative SS items (handrails and sculptures, mostly) placed along oceanfronts, we always recommended 316 or better, and in that environment even the 316 generally needs annual or semiannual treatment to clean up "tea staining" corrosion and repassivate the surface.
Since your object is a functional part it may be hard to change to a different alloy as that could affect the mechanical properties. However you may have no choice if you need years without corrosion.
The black nitride finish may provide some additional corrosion protection.
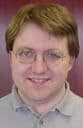
Ray Kremer
Stellar Solutions, Inc.

McHenry, Illinois
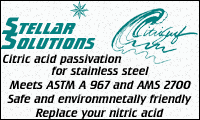
October 23, 2009
There's no way I'd use 416 in a marine or salt water environment, and I'd doubt the black nitride will help much if at all. 416 is a free machining, low-chromium martensitic (sometimes) stainless steel. Ease of machining and potential to harden to about HRC 35-40 are it's strong points, but corrosion resistance is one of the weak points.

Lee Gearhart
metallurgist - E. Aurora, New York
October 29, 2009
November 24, 2009
Hey Ivan,
For the marine environment in your application I suggest 316, or
316L. You can go more exotic and fabricate with 2205 or 2507 duplex stainless (more expensive)for even more corrosion resistance.
At the very least passivate or better yet electropolish the 316 or
316L as the last step in the manufacturing process. This will greatly increase the corrosion resistance.
I have results and pictures from an extensive salt fog test/study for long term marine exposure on 304 and 316 welded stainless steel samples. The samples were: raw un-treated, passivated only, electropolished only, electropolished and passivated.
Of all the samples the electropolished only and electropolished plus passivated 316 samples were virtually unaffected and in the same condition as before the test was started.
- North Vancouver, BC, Canada
You could try baked on PTFE coatings which have about 500 hour saltspray. Deep water (ocean floor) valves and fittings are coated with various epoxies and teflons.
Wayne McKee- Mississauga, Ontario, Canada
December 2, 2009
Q, A, or Comment on THIS thread -or- Start a NEW Thread