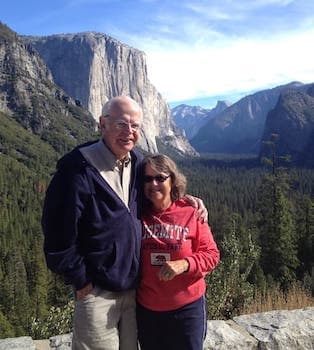
Curated with aloha by
Ted Mooney, P.E. RET
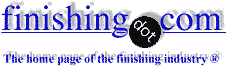
The authoritative public forum
for Metal Finishing 1989-2025
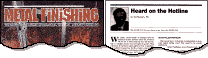
-----
Vacuum plating results in more thickness than bargained for
We send our watch parts for Titanium, IPS, and IPG treatment, but the plating has a problem adhering to 10 - 20% of the pieces. After
250°C heat-treatment and vacuum, we see the plating risen into a hump, but only on the cast parts (which are silicon brass). Lathed pieces never have the problem.
The plating company has been blaming our casting material, but we haven't been able to come to a firm conclusion.
work in jewelry & watch industry - Kaohsiung, Taiwan
October 16, 2009
First of two simultaneous responses --
We PVD coated cast parts, and often see the same problem. There are often voids in cast parts. When put in a vacuum chamber and heated, the gas in the voids expands. Pressures rise enough to produce the humping effect you describe. If the voids are near the surface, you can get holes as well.
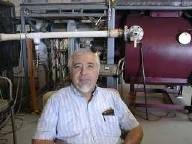
Jim Treglio - scwineryreview.com
PVD Consultant & Wine Lover
San Diego, California
October 19, 2009
Second of two simultaneous responses --
This is a wild guess, since I can not see the part.
The plate delaminated. The cause is probably because typically, cast parts require a lot more preplate time and concentration. This removes the brass portion of the alloy and leaves a silicon rich surface which is tough to plate.
The probable cure is to add a fluoboric acid dip after the other preplate processes. This will remove a lot of the silicon allowing the entire surface to plate.
- Navarre, Florida
October 19, 2009
Q, A, or Comment on THIS thread -or- Start a NEW Thread