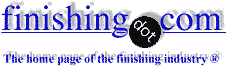
-----
Oxalic Anodizing Performance vs Mechanical Finishing process
We are using oxalic anodization on 6061 Aluminum and did an experiment to determine what impact the surface finish has on HCl bubble test (corrosion resistance) test results. We found that Lathe turned parts give a lower level of performance than Milled parts for the same level of surface finish (Ra in microinches.) The lathe turned parts are not sensitive to varying levels of surface finish in the range of 8 - 25 microinches while the mill finished parts perform better when the surface finish has a lower level of Ra.
Can anyone explain this phenomenon and suggest what could be done to raise the corrosion resistance of the lathe turned parts?
Engineer - Austin, Texas, USA
October 14, 2009
My guess is that a turned part has ridges like a super fine screw that will not anodize as well in the valleys and will hold the acid better.
A milled part will tend to be smoother (if done well) so will anodize better and not hold the acid as much. Sometimes tiny differences make a huge difference in the final part.
Solution-try a very thin final pass with the lathe part. Try to achieve a finish similar to a great diamond turned part. IE: slower feed.
- Navarre, Florida
October 16, 2009
Ahhh.. gotta love the AMAT specs.
First things first, make sure you are comparing apples to apples, and that the material you are comparing is from the same lot. Also, believe it or not, there is a difference between plate stock, and bar stock...in particular with the test you are performing. Usually lathe turned parts are from bar stock, while plate stock is used in mill machined parts.
With that being said, for that test, you do want the Ra to be as low as possible, so I would suggest a sanding/polishing step after the machine work to get a low Ra value. If both parts have the same Ra value prior to anodizing, are anodized under the same conditions, and one fails and one passes, then it would be obvious to me that you are starting with materials that aren't exactly the same.
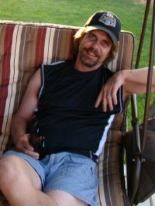
Marc Green
anodizer - Boise, Idaho
October 22, 2009
A further experiment indicated different results on milled finish
(same Ra) of the same piece of aluminum depending on distance from the rolled surface. Center of the rolled plate being less corrosion resistant than the surface. This is presumed to be because of gradation of grain structure.
Which type of aluminum gives the most consistent grain structure for anodization across its thickness?
- Austin, Texas, USA
November 2, 2009
I believe the spec states that 6061T6 must be used, with the best, most consistent, results being obtained from 1/8" plate stock (the thinner the stock, the more consistent grain structure). Also, I strongly suggest using certified Alcoa material.
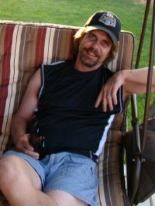
Marc Green
anodizer - Boise, Idaho
November 3, 2009
The parts I am anodizing are made from 2 in to 4 in rolled plate that is machined away so that some surfaces are from the interior of the plate and others are closer to the rolled surface. I want all of the part to have similar performance with respect to corrosion resistance. The grain structure in the interior of the rolled plate is not the same as that near the surface. This seems to impact the anodizaiton performance.
Now it is easy for everyone to achieve good perfromance on sheet metal coupons or the top surface of the rolled plate where the grain is well behaved, But some anodizers are better than others at achieving the desired performance on the surfaces from the interior of the rolled plate.
What are the important parameters in the anodization process that would cause that?
- Austin, Texas, USA
November 17, 2009
November 23, 2009
Although I'm very familiar with the test, and most likely the requirements of the end user, my background is in Sulfuric anodizing, not Oxalic.
Are you using Alcoa material? I've found that it does have a more consistent grain structure than other manufacturers. But even on thicker stock there will be some variance.
Without going into too much detail, the 3 factors I've found that influence results on that particular test, in sulfuric anodizing were:
Electrolyte temperature
Current density
Sealing parameters.
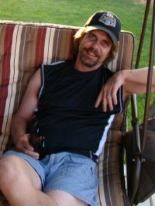
Marc Green
anodizer - Boise, Idaho
Q, A, or Comment on THIS thread -or- Start a NEW Thread