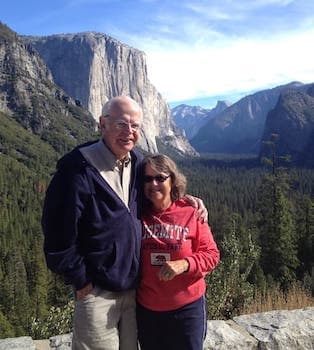
Curated with aloha by
Ted Mooney, P.E. RET
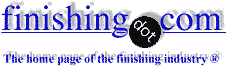
The authoritative public forum
for Metal Finishing 1989-2025
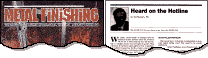
-----
White film or "dust" on anodized parts
Current question & answers:
August 18, 2021Q. We have a black dye tank and are getting a copper/bronze film on the tank. It is on the parts after they are anodized but wipes off easily. What is weird is that even though it wipes off the rag is still white, like nothing was on it. A few months ago we ran some castings in the dye, I know, not too smart, and I was thinking that once they hit the dye after anodizing the heat opened the pores and the dye got contaminated? Any suggestions? I have attached some photos.
- Joppa Maryland
A. Hi Henry. This thread introduces some additional ideas regarding what can cause such films, and topic 2238, offers rather deep coverage of analysis & maintenance of the black dye tank itself.
Luck & Regards,
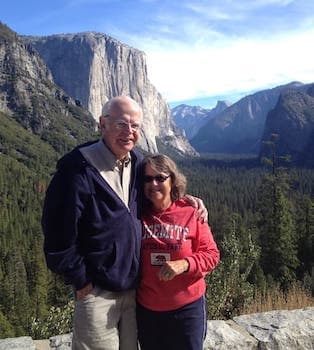
Ted Mooney, P.E. RET
Striving to live Aloha
finishing.com - Pine Beach, New Jersey
August 2021
A. Hi Henry!
You gotta get a filter pump with 20µm baleen polypro and a mixer in there. You really should never find yourself in a situation where a dye tank develops stratification, especially a surface scum layer. Keep it fully turned, pH adjusted to less than 0.25 units off manufacturer target, and if it's not in constant use, cover it. But keep the mixer/filter going even when idle, and change the filter tubes at least once a week.
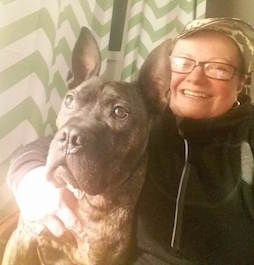
Rachel Mackintosh
lab rat - Greenfield, Vermont
September 28, 2021
⇩ Related postings, oldest first ⇩
Q. Our black anodize is coming out with a red tint to it. Has anyone come across this problem before? Please help.
Randy A. Mattson- Seattle, Washington
2002
Treatment &
Finishing of
Aluminium and
Its Alloys"
by Wernick, Pinner
& Sheasby
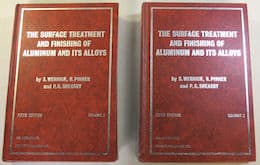
(note: this book is two volumes)
on eBay or
AbeBooks
or Amazon
(affil links)
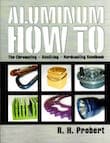
Aluminum How-To
"Chromating - Anodizing - Hardcoating"
by Robert Probert
Also available in Spanish
You'll love this book. Finishing.com has sold almost a thousand copies without a single return request :-)
A. Hi Randy. Change your lighting or change your dye :-)
Some black dyes have a red tinge that doesn't show in fluorescent lighting.
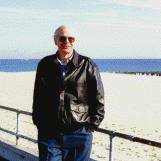
Ted Mooney, P.E.
Striving to live Aloha
finishing.com - Pine Beach, New Jersey
A. Randy:
A. All aluminum black dyes are either blue, green or purple (red) based. There are a number of factors that will/can yield the base color of the black anodize; Oxide coating too thin, dye time too short, dye bath pH too high, dye bath concentration (active dye) too low or dye bath contamination. Your supplier should be able to check this for you.
- Monroe, North Carolina
2002
Q. Also some of our black parts have a white film on them. They are easily wiped off with MEK / methyl ethyl ketone. What causes this?
Randy A. Mattson [returning]- Seattle, Washington
2002
A. The sealing process, especially a nickel acetate seal, can leave a white residue.
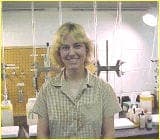
Megan Pellenz
- Syracuse, New York
2002
A. I have seen the reddish tint on black due to a couple of different reasons. One is sometimes you will notice a light discolor film of brown/red scum floating on top of the black dye after the air has been shut off. This is typically anodizing salts that have flowed downstream and will take every opportunity to attach themselves to dyed parts.
If this is not the reddish color you are speaking of, then here is another suggestion: Your black dye might be low on buffering agent. If you use sodium acetate, them make sure that you are at a 50% concentration of sodium acetate compared to your black dye. If the recommended amount is not 50% then make sure it is where it is supposed to be. Send a sample to the lab and ask for them to analyze the sodium acetate concentration for you and adjust accordingly.
- cicero, Illinois USA
August 1, 2016
Q. We are having difficulty anodizing (especially black dye) aluminum parts. There appears to be, for lack of a better term, "dust" or "sand" on the parts. Originally we thought the problem only existed on black dye parts and eventually determined that the dye was contaminated. We have changed the dye bath as well as the seal (nickel acetate). We then were informed that our sulfuric bath was too low in concentration and increased it to 230 gm/l. Still have the same problem except the "dust" is smaller, but more prevalent. Sometimes we can wipe the "dust" off after dye and then seal resulting in a okay finish, but sometimes we end up with white spots in place of the "dust". We are wondering if we should approach the sulfuric bath, or move to the front of the line and examine the clean, etch or desmut bath. Any ideas?
P.S. 14 amps/sq. ft. and 720 rule for soak time. All alloys, with most of the problems arising with 2024.
Thanks in advance for the help.
anodizing shop junkee - Mulberry, Florida, USA
October 14, 2009
![]() |
A. I think that your problem is not having a dedicated desmut tank after the etch step. Some combined ones work when the tank is new, but get worse as they age. You say that 2024 is a problem . 7075 is probably as bad or worse (guess). Both are high alloy, mainly copper, and will smut a lot, giving the dust like parts as the aluminum around the smut anodizes and the smut does not. James Watts- Navarre, Florida October 16, 2009 A. 1. Check for galvanic voltage (about 1.08 volts) between the titanium rack and the stainless steel dye tank. Find a way to reverse it or come back and I will write it out again. ![]() Robert H Probert Robert H Probert Technical Services ![]() Garner, North Carolina ![]() October 16, 2009 October 17, 2009 A. You probably are in a dusty environment. I advice setting up a small clean room with air purifier to isolate exposure to dust as the metal surface becomes vulnerable because of charge/ions diffusion it has went through while the plating process. - Gilroy, California |
Q. If I didn't mention before, we do have a dedicated desmut tank. Each tank is followed by a dedicated rinse tank.
The dye tank is poly-pro, not stainless, so I am not having that issue.
The shop is very clean, but we had the thought of dust contamination at first also. We dumped and recharged the dye and seal because that was our first thoughts. That did not help at all. We are climate controlled and have only been in this facility for several months. I don't think dirt is our problem, but we have not completely ruled out that possibility.
We have had great success for some time now and then things slowly started getting worse. Does copper contamination cause any of these issues? We had a long hook on one rack that was in the bath and caused the cathodes to take on a copper color. This is the reason we are now dumping the entire acid bath and restarting. We originally had around 120 gm/L, but were told to charge the tank up to 230 gm/L. We noticed a big difference in the color of the parts after anodizing. We are planning on recharging at 165 gm/L, but Mr. Probert says 180 gm/L. Which is best when we anodize a little bit of everything. We are also wanting to change the cathodes (which brings up another questions). We were told that the original cathodes were 1100 alloy, but are trying to locate 6063-t6 because of all the chatter leading us that way. So far we have had no luck in locating them locally. Will another temper or alloy work?
Thanks for the help.
Cheers
anodizing shop junkee - Mulberry, Florida, USA
October 20, 2009
A. Mike
Do you pretreat the components via any buffing/abrasives/blasting process?
Some time the particles from all the above three processes will cause the issue on your parts.
Vijendran
- Chennai, India
October 22, 2009
A. Good Morning from the UK
You may find that the powder is in fact an oxide of aluminium, which is the result of the anodic coating being dissolved by the sulfuric acid in solution.
When the coating has built up sufficiently in thickness and you can no longer increase that thickness because of lack of Voltage available from the rectifier, then the solution just dissolves the anodic layer you have just laid down.
Decide when this situation has developed and just remove the component from the tank, although the real answer is to use a rectifier with more voltage available to complete the task or reduce the number of components in the tank to compensate for the overloading in the tank, which is another source of problems.
Hope this is of help
- Camberley, Surrey, UK
October 24, 2009
A. Hello,
Is the problem still there?
Do you anodize/ dye on titanium racks? Try to dye one part on aluminum only, when 2000 alloy not too long. Or put a magnesium bar in the dye while dyeing, in contact with the titanium rack.
- Eindhoven, Netherlands
April 1, 2010
Q, A, or Comment on THIS thread -or- Start a NEW Thread