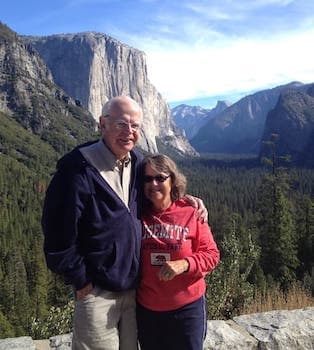
Curated with aloha by
Ted Mooney, P.E. RET
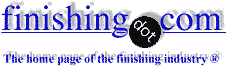
The authoritative public forum
for Metal Finishing 1989-2025
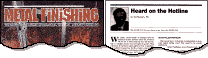
-----
Black spots/Lack of adherence of Zinc in HDG of heat treated bolts
October 13, 2009
I'm a engineer in the midwest (USA) looking to solve a bare
(black) spot defect that has started becoming a significant issue with one of our suppliers. Is the following process sufficient in cleaning heat treated parts prior to HDG?
4 min alkaline degreaser ambient temp
Dip in rinse tank (tap water)
6 min 10-12% HCl ambient temp
Dip in rinse tank (tap water)
4 min Flux tank ambient temp
Thank you in advance for any suggestions that would help with this issue
Fastener Manufacturing - St. Joe, IN, USA
First of three simultaneous responses --
If you did not mandate the prep process, then the problem is with your vendor and it is his problem. I would hope that you had enough boiler plate in your contract in the quality section that it is obvious that the parts do not comply.
As a side bar, the amount of heat treat scale from poorly operated furnaces will vary by orders of magnitude. It is not uncommon to have to use abrasive blast to get the part clean enough.
- Navarre, Florida
October 14, 2009
Second of three simultaneous responses -- October 15, 2009
Drew:
When you said: "...black (bare) spot defect that is BECOMING a significant issue..." it alerted me to the fact that here in the USA we are going into winter. Thus as winter approaches the AMBIENT temperature of all the tanks will decrease AND the black (bare) spot problem will increase. (Unless of course, the plant is in a heated building.) I recommend that you actually measure the temperature of the caustic, acid, and flux tanks as AMBIENT has no scientific meaning. Obviously you have access to the galvaning plant as you have measured the TIME in each tank. In addition to time and temperature for the bolts in each tank the concentrations, compositions, and impurities of each tank are also critical. As a supporter of finishing.com I have requested information about your company and look forward to helping you solve this problem. With the limited information that you have presented, I do expect that the precleaning steps are not adequate.
Regards,
Galvanizing Consultant - Hot Springs, South Dakota, USA
Third of three simultaneous responses -- October 15, 2009
4 mins alkaline degreaser at ambient temp.
Time is Ok, but most alkaline degreaser are far more effective at about 50-60 degrees C.
Dip in rinse tank (tap water)
OK
6 min 10-12% HCl ambient temp
This seems rather short. You mentioned heat treatment in the bolts. If this was at sufficient temp to create oxide scale (grey flaky stuff sometimes called mill scale), then 4 mins in 10% will not be enough. The consequence of under pickling is that you will not present a chemically clean surface to the zinc, and so it will not alloy. Where any scale remains will have a coating gap.
Dip in rinse tank (tap water)
OK
4 min Flux tank ambient temp
Here you didn't mention concentration, flux ratio. Typically cold
(ambient) flux has poor performance. This could also create problems manifesting as gaps in the galv. Best temp here is quite high, like about 60-70 C. There's a whole range of opinions about whether you should use "double salt", triple salt or quadraflux. This refers to the ratio of the ammonium chloride to zinc chloride in that flux solution. But whichever you use, using it at ambient is likely to lead to quality issues.
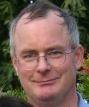
Geoff Crowley
Crithwood Ltd.
Westfield, Scotland, UK
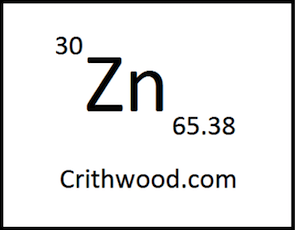
Q, A, or Comment on THIS thread -or- Start a NEW Thread