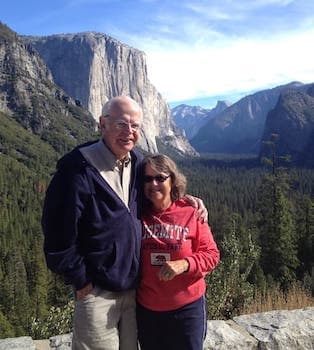
Curated with aloha by
Ted Mooney, P.E. RET
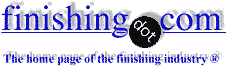
The authoritative public forum
for Metal Finishing 1989-2025
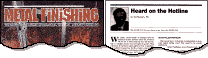
-----
BAC5845 Paint Wet Adhesion Failures to BSS7225 Type II, Class I
Q. I am applying Primer BMS 10-11 IAW Spec BAC5736 & Top Coat BMS10-60 IAW BAC 5845 with a precleaning IAW BAC5750 & Testing IAW Fed-Std-808... then performing Wet Adhesion Testing IAW BSS7225 Type II, Class 1, and I am experiencing random failures at a rate of 12 to 18%
Failures experienced are 1) Complete Paint System Failure to the substrate 2) less frequent, delamination failure between primer and top coat 3) miniature bubbling effect on the Top Coat surface where the cheesecloth was located.
Substrate material is 2024 Al & 7050 Al both anodized to MIL-A-8625
[⇦ this spec on DLA] Type II, Class I. Some units have been Hot water Sealed and some Nickel Acetate sealed. Both method of sealing have suffered adhesion failures.
The Substrate is being cleaned w/ MEK and Water Break Test is passing with water sheen that well exceeds 30 seconds.
BSS7225 requires the Wet Adhesion to be performed on the HARDWARE instead of sample panels. We've run 12 test panels of 2024 anodized and sealed 4 with hot water, 4 with dichromate, and 4 with nickel acetate and all passed wet adhesion but, for some reason we continue to experience failures on our hardware. Can someone explain why? It would be greatly appreciated.
QE/ME at Aerospace Mfg Co. - Los Angeles, California
October 7, 2009
A. Doug
If you have not done so already, refer to 3.11, 6.3, & 6.11 of MIL-A-8625
[⇦ this spec on DLA].
Are your coupons test or witness?
- Colorado Springs, Colorado
A. Doug,
To me it looks like a surface contamination problem, but that is probably an over-simplification of the problem.
I have never been a fan of sealing anodizing that is subsequently painted as sealing pretty much negates the positive effects of anodizing in the first place. I am not saying that this is the source of your problem, but it certainly won't help.
Other possibilities may include incorrect mixing ratios, incomplete curing, insufficient flash off time before a forced cure, excessive delays between priming and top-coating.
I think you need to get down on the line and see what is happening. Check how your operators are mixing the paint, how they measure the viscosity, whether they allow sufficient induction time, how they are pre-cleaning the anodizing, how they are applying the paint, how they are curing the paint. Are all process parameters meeting your specification requirements? What variables are there that might fall outside of the manufacturer's data sheets? Is the inspection (tape test) being carried out correctly? Is the right tape being used? Anyway, you get the idea.
Aerospace - Yeovil, Somerset, UK
Q. I have been struggling with a similar paint adhesion issue, testing to the same BSS7225. I am applying BMS10-11 primer on titanium that is pretreated with Phosphate-Fluoride solution per BAC5861. I was having great issues with paint adhesion prior to implementing a pre-treatment of grit blasting the part surface with aluminum oxide per BAC5748.
The grit blasting seems to help a lot, but I have had a recent rash of more failures. We are not testing 100% of pieces but test 10% of the pieces in each lot at around 5-10 lots per day.
Some failures seem to be so/so, where there is mostly adhesion with some small "specks" of removal, and other lots where the area of the tape had NO adhesion whatsoever. See pictures!
I looked at AMS2486 which specifies different solution limits than BAC5861. Most notably, the TDS of rinse water must be maintained below 200 ppm rather than 300. So far, I cannot prove a correlation to adhesion failure when TDS is over 200 ppm but it seems suspicious.
I am looking for information on what might be the most important factors in passing the Wet Tape Test. I suspect the grit blasting to be inconsistent, and there are potential issues of product being handled without gloves. I have seen fingerprints below areas of paint removal. Does anyone know what impact any of this may have? I am desperate in this case and open to any ideas! I will provide more information if it will be helpful.
- Albany, New York
February 18, 2013
Substitution of BMS10-11 primer
Q. I'm a Quality Engineer working at a company which manufactures assy of commercial aeroplanes. During assembly process the aluminum alloy detail parts that have been primed with BMS10-11 type I Class A Grade A primer always have paint peeled condition in some small areas, so touch up the bare metal is required, my question is can we use the BMS10-11 type I Class A Grade E primer substituted Grade A for touch up finishing? I have gone through the relevant Spec. BAC5736 and BMS10-11 criterion, but I cannot find any reference to this topic. Thanks in advance for any help.
Allen Hao- Chengdu, Sichuan, China
August 5, 2013
A. Hi Allen,
If you have patches of non-adherent paint I would worry about the whole coating and would suggest the parts should be stripped and re-painted.
As for touching up you need to check with your customer and ultimately with Boeing about touch up of Boeing paint schemes, we as an anonymous group cannot advise what is acceptable or unacceptable to Boeing.
Aerospace - Yeovil, Somerset, UK
Q. Hello,
What is the color of the Nose Wheel Well Spin Brake Spring?
- Miami, Florida
December 14, 2023
Q, A, or Comment on THIS thread -or- Start a NEW Thread