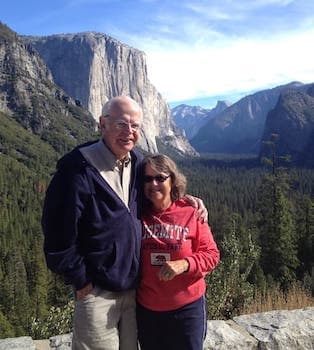
Curated with aloha by
Ted Mooney, P.E. RET
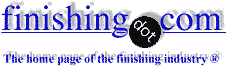
The authoritative public forum
for Metal Finishing 1989-2025
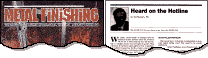
-----
Thickness guideliness for copper or nickel over brass
I'm currently faced with a problem in understanding the thickness guidelines for plating over brass. I have an electronic component with brass pins that are dipped in Sn63/Pb37 solder with no undercoat. On this site, there were recommendations of 150 microinches of nickel or 100 microinches of copper over brass and that would help with solder adhesion. I needed to know if the industry standard is documented in an industry specification or is just "best practice"? I am going to need some ammunition to support my position that we should reques
John Williamsbuyer of finished goods - Hartford, Connecticut, USA
October 5, 2009
With proper preparation,good adhesion on brass can be obtained without an undercoat, however, hot dip coating results in a reaction layer of a relatively brittle copper-tin intermetallic compound. If the temperature is too high or the exposure is long, the thickness of this brittle layer can be significant and flaking or peeling can occur.
For this reason and also for better dimensional control, many copper and brass electronic components are now plated with solder instead of being hot dipped.
Nickel would form a diffusion barrier that prevents the copper-tin compound from forming, whereas copper would not.
consultant - Cleveland Heights, Ohio
October 12, 2009
Q, A, or Comment on THIS thread -or- Start a NEW Thread