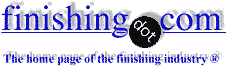
-----
E coating vs Zinc plating, long term which is the better option?
Q. My part can either be e-coated or zinc plated. Does either process have an advantage over the other for the long term. Other than the e-coat there will not be an additional finish coat applied. Thanks
Gregg Yasherproduct designer - Cleveland, Ohio USA
September 29, 2009
by Electrocoat Association
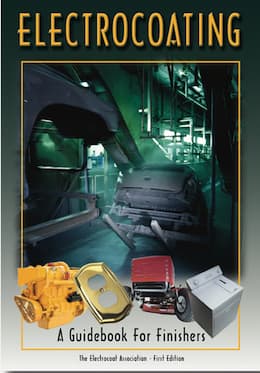
on eBay or Amazon
or AbeBooks
(affil link)
A. Hi, Gregg. If one were "better" than the other, the latter wouldn't exist. Selection of one process over another must take into account the kind of parts and the exposure situation. For example, if the parts get scratched, zinc plating will still provide sacrificial protection, while electrocoating does not. But a non-sacrificial coating like E-coating will probably easily outlast a thin sacrificial coating like zinc plating if you try to judge it by salt spray test rather than real-world exposure. What are the parts and the situation? Thanks.
Regards,
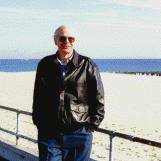
Ted Mooney, P.E.
Striving to live Aloha
finishing.com - Pine Beach, New Jersey
September 29, 2009
Q. For rust prevention, which is the first choice: zinc plating or e-coating.
Michael Shen- detroit, Michigan
October 16, 2012
A. Hi Michael. E-coating will probably outperform zinc plating in salt spray testing, which is one measure of rust resistance. That does not change the previous answer though, that zinc plating is a sacrificial coating whereas e-coating is only a barrier layer coating, and it isn't possible to make proper suggestions in the abstract.
Luck & Regards,
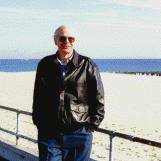
Ted Mooney, P.E.
Striving to live Aloha
finishing.com - Pine Beach, New Jersey
October 16, 2012
Q. Hi,
My client is looking for Zinc-Nickel coating for a valve bracket. We currently offer e-coat. However, this program is concerned about conductivity and wants to switch to Zn-Ni.
1. What is the cost difference between the two coatings?
Automotive - Detroit, Michigan
January 25, 2017
Q. Which is costly between E-coating and Zinc Passivization?
Bharath Reddy- Pune, Maharastra, India
May 19, 2017
A. Zinc plating is one of the least expensive and most versatile corrosion resistant finishes, especially for small hardware, because the items can be plated in bulk and with relatively simple equipment, yet can be readily automated. Zinc-nickel is an alloy finish that is somewhat more expensive, and somewhat less commonly available, but not drastically so. Still, it does no good to get estimated costs if the service isn't actually available, so the best way to proceed is usually to get quotes. Good luck.
Readers: In posting questions please try to heed the repeated requests of our regular responders that you not post abstract questions, but carefully detail your own situation.
Regards,
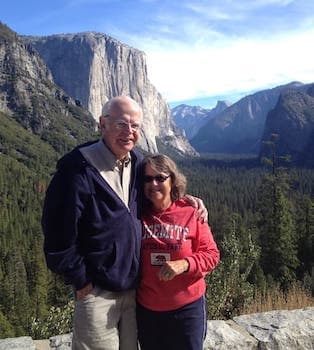
Ted Mooney, P.E. RET
Striving to live Aloha
finishing.com - Pine Beach, New Jersey
May 2017
Door accessories: plating or e-coating?
Q. Hello everybody! I'm working for a plant. We make door locks and accessories. Lately, we are having kind of a dilemma: to zinc/chrome our handles or e-coat? We have a plating plant here. We plate steel and ZAMAK. It looks like e-coating is going to be more expensive, but I can't make the whole picture of the costs as regards our core product, as well as technical peculiarities.
What type of treatment would you advise and why?
One more moment: decorative effect is also important.
THANKS in advance.
employee - Ryazan, Russian Federation
July 4, 2017
A. Hi Viktoriya. I have expressed my opinion that zinc plating and chromating is probably less expensive than e-coating and that the chief reason is probably that many of your parts can be plated in bulk rather than having to be individually jigged for e-coating. Beyond that, abstract ideas about cost don't go very far -- you would need to cost out an e-coating line and the labor and chemicals it requires to operate.
Zinc plating is a sacrificial coating which offers corrosion resistance advantages in rough service, and the abrasion resistance of metal. But phosphatizing followed by e-coating will probably offer greater corrosion resistance in most applications. You know what the plating looks like because you already do it. The e-coating will look like paint, but it can look like pretty nice looking paint :-)
Regards,
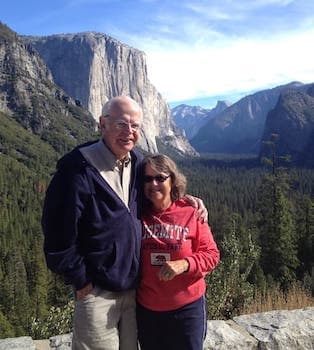
Ted Mooney, P.E. RET
Striving to live Aloha
finishing.com - Pine Beach, New Jersey
July 2017
Dear Mr. Mooney, I appreciate your advice!
Viktoriya Kapustina [returning]OOO "BORDER" - Ryazan, Russian Federation
July 7, 2017
A. The two work differently. E-coat is a barrier, while zinc is a sacrificial anode. Zinc will tend to degrade over an area, whereas e-coat tends to pit, rather than a large patch. Been a while since I've worked with e-coat, but if I recall testing, e-coat lasts a little longer. Just recognize that the parts down the road will look very different, and pits may be a more serious failure mode.
Dana Trousil- Victoria, BC, Canada
August 11, 2017
October 19, 2017
Q. For steel parts, like car suspension arms, tie rod ends, mounts, brackets etc. Can zinc coating be done over e-coating?
Like, if you put an e-coat on first, can you then zinc coat it on top of/over the e-coat?
Or would that have to be done vice-versa?
I'm trying to explore options for higher durability coatings for longer parts service life.
Then, can those coatings withstand being powder coated or ceramic coated in a kiln as an additional finish coating for aesthetics?
Or would the e-coat or zinc compromise the ability of ceramic coating or powder coating?
Or does e-coat or zinc coat break down from kiln heat or chemical incompatibility?
- San Jose, California USA
A. Hi Ryan. Electroplating, galvanizing, and other finishes of solid metal, and conversion finishes like phosphating, chromating, and anodizing, must react with the base metal and can only be done onto bare metal. Because of the very high process temperatures involved in ceramics, they usually can only be done on bare steel. An actual ceramic coating is like covering the component in melted glass, but some paints call themselves 'ceramic' with no justification except having some ceramic particle grit in them.
In general, organic finishes like e-coating, paint, and powder coating can be done on top of metallic finishes -- but that does not guarantee compatibility of the particular metallic finish and the particular organic and its deposition method. Please name an actual part with an actual finish and why you consider it less than satisfactory, and please introduce yourself as a hobbyist wanting to restore old parts or a plant manager wanting to build a production line or whatever, and people may be able to give specific advice. Good luck!
Regards,
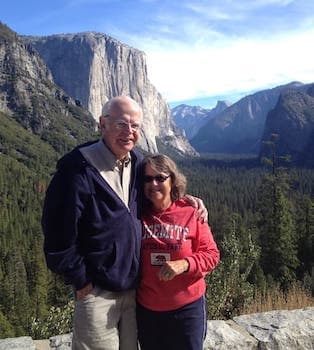
Ted Mooney, P.E. RET
Striving to live Aloha
finishing.com - Pine Beach, New Jersey
October 2017
Q. Hi,
We use E coating for commercial vehicle transmission output flange. Earlier we were using Zinc plating. Would there be a difference in coefficient of friction? Is this quantified?
Thanks
- Pune, India
July 22, 2019
A. Hi Rao. Sorry I don't know the coefficient of friction for these two finishes, but yes they could be quite different. The new finish is a thin layer of paint and the old is metal. Regardless of the coefficients though, I wouldn't expect paint to resist wear/friction for very long without either wearing off or gumming up.
Regards,
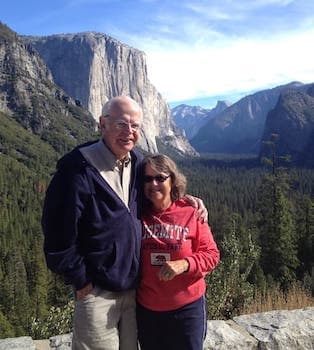
Ted Mooney, P.E. RET
Striving to live Aloha
finishing.com - Pine Beach, New Jersey
July 2019
Q, A, or Comment on THIS thread -or- Start a NEW Thread