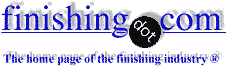
-----
Trivalent on anodized 6061 aluminum, in a marine environment?
September 25, 2009
I'm looking for a non-reflective finish for 6061-T6 aluminum that will be used in underwater equipment housings for scuba divers. The goal is to last 1,000 hours in a salt fog test, not add too much tolerance to some precision hole diameters (too much buildup could cause the seals to not work properly).
Would type 2 anodizing with a trivalent seal be best? I see a lot of data online on trivalent with 2024, not so much information on trivalent and 6061. I'm concerned about the added tolerance from type
3 anodizing, and the customer doesn't want to use anything with hexavalent chrome. Also, for cosmetic reasons, the customer wants a finish that visually contrasts with high-phosphorous EN plated shafts.
mechanical engineer - Somerville, MA, USA
Do not put into salt water any: aluminum, aluminum oxide, or hydrated aluminum oxide (sealed). The only thing that will work for you is either electroless nickel over the aluminum or powder coat.
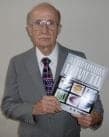
Robert H Probert
Robert H Probert Technical Services

Garner, North Carolina
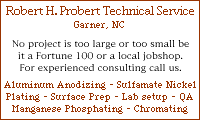
September 28, 2009
Mr. Probert, thank you for your response. Could I ask you to elaborate on why you don't think sealed anodized aluminum is appropriate for a saltwater environment? I assume that you have seen corrosion from that chemistry, but how quickly and how severe? Your statement that sealed anodize aluminum won't work in saltwater seems to contradict some of the reports I've seen from the Department of Defense on type 2 sulfuric acid anodize post-treated with chromate that survived over 1,000 hours of a neutral salt fog without visible corrosion.
Is the issue that the DoD and you are talking about different time scales? The product I'm working on has a target service life of around 1,100 hours underwater (3 hours per day, every day for a year), if that helps.
- Somerville, MA, United States
September 29, 2009
Sodium Chloride attacks (1) aluminum, (2) aluminum oxide and (3) hydrated aluminum oxide. If the hydrated aluminum oxide molecule is occluded with hex chrome then perhaps it will take 1000 hours of sea water. The whole process would have to be perfect, not like then typical job shop in the yellow pages. I may be out-of-date but have not heard of a trivalent chrome seal for anodizing. Recommend testing before you commit, menawhile use electroless nickel or powder coat. And even if we get 1000 hours, if a scratch and the chloride gets to the metal, it will go fast.
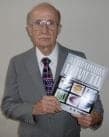
Robert H Probert
Robert H Probert Technical Services

Garner, North Carolina
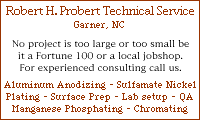
October 1, 2009
The Navy's dive development unit at Panama City, FL uses a lot of passivated 316 for their manifolds and etc. They do a lot of research and some of it is classified. They might talk to you in general terms of metallurgy selections.
James Watts- Navarre, Florida
October 3, 2009
Q, A, or Comment on THIS thread -or- Start a NEW Thread