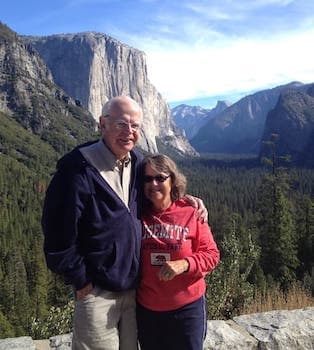
Curated with aloha by
Ted Mooney, P.E. RET
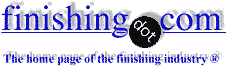
The authoritative public forum
for Metal Finishing 1989-2025
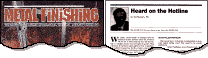
-----
Galvanizing irregularities & defects and how to control and remove them
September 24, 2009
Q. We have a hot dip galvanizing line, and during producing zero spangle product, we face this defect: it is called galvanizing irregularities on the surface of the sheet.
Product specification as follows:
- coil Thickness 0.5 mm and 0.8 mm
- coil width 1250 mm
- zinc coating weight 150 g/m2
For your information, in case of decreasing the coating weight to 120 g/m2 we never face this defect.
And now I am asking your kind personal help about how to remove this defect when zinc coating weight is 150 g/m2, taking in your consideration that the air knife gap is 0.65 mm in the middle and 0.9 mm on the edge; line speed 90 mpm and the air knife pressure 550 mbar.
- Cairo, Egypt
October 23, 2009
A. Hazem:
In producing zero spangle, I presume your lead (Pb) content of your molten bath to be near zero? It would be helpful to also know your aluminum content, I presume near 0.2%. Are you a hydrogen/nitrogen hot atmosphere operation just prior to the molten zinc? Or (unlikely) a flux operation? What type of zinc kettle do you have iron or ceramic? How long has the present kettle been in operation (since change-out)? Perhaps I could help if you could provide answers to my questions.
Regards,
Galvanizing Consultant - Hot Springs, South Dakota, USA
November 15, 2009
Q. Dear Dr, Thomas
1- Yes, Pb content near to zero, less than 90 ppm.
2- Also the aluminum content is within range 0.18% to 0.22%.
3- Yes, we have a hydrogen/nitrogen hot atmosphere operation just prior to the molten zinc (NOT flux operation).
4- The type of zinc kettle is stainless steel 316 L
5- The present kettle been in operation since 2008.
Wishing you to help me to solve the problem.
Thanks so much.
- Cairo, Egypt
November 16, 2009
A. Sir,
316L stainless steel (containing about 12% nickel) is not a suitable material to use for a hot dip galvanizing kettle because the nickel in the stainless steel is attacked by the molten zinc and becomes brittle. You may have a dangerous situation. You should have the molten zinc tested and if it contains more than 0.05% nickel then you have a major problem.
How thick is your stainless steel kettle? What are the kettle dimensions (L, W, D)? What temperature do you operate the kettle? What is the weld material and what process was used for welding?
Regards,
Galvanizing Consultant - Hot Springs, South Dakota, USA
A. Dear sir,
I think you mean irregular spangle; that can be from:
1. difference in roughness of base,
2. dirt on the surface,
I think you have to improve the cleaning section.
If you have skin pass and chromate you will do better to use dry skin pass and then chromate.
steel - esfahan, mobarake, Iran
April 13, 2013
by Kuklik & Kudlacek
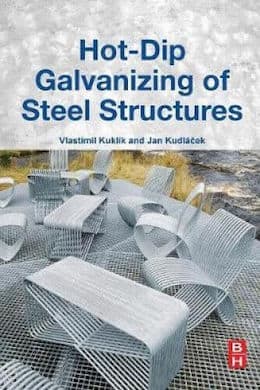
on AbeBooks
or eBay or
Amazon
(affil links)
Q. Respected sir....
I am from India. My responsibility is to look after quality. I came across many defects which I have recognised but a few of the defects I can't recognise. I just want that if you can discuss a small description related with defects ... maybe by uploading their pictures?
Utkarsh limited - West bengal
August 12, 2017
A. Hi Raj Kumar. Just as a doctor may be able to at least ask additional questions after he has learned your body temperature, yes, it is quite possible that we can begin a process of suggesting how to correct the problems after you upload those pictures.
We already have a number of threads with pictures of galvanizing defects, and have enjoyed some success at it.
Regards,
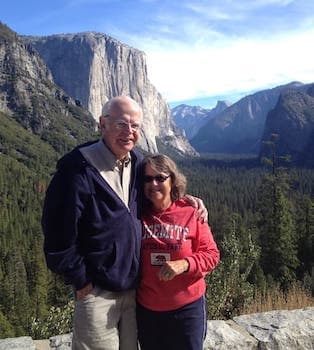
Ted Mooney, P.E. RET
Striving to live Aloha
finishing.com - Pine Beach, New Jersey
August 2017

Q, A, or Comment on THIS thread -or- Start a NEW Thread