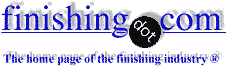
-----
To Pass 24 hours of Neutral Salt Spray Test in Nickel and Chrome Plating
Q. Respected,Sir / Madam. we have a customer requirement that is 10 micron of bright nickel and 0.2 micron decorative chrome plating on ferrous material and he want 24 hours of neutral salt spray test. sir we have tried plating 15 micron of nickel and 0.4 micron of chrome even then we have failed in salt spray test (neutral salt spray test) can anyone please tell me how many microns of nickel and how many micron of chrome is required to pass this 24 hours of neutral salt spray test Thank you to all who help!.
Aboo Backerproprietor - Bangalore, India
September 23, 2009
A. 15 should come close. I prefer 25 µ Ni. Cut some parts in the rust area and see if you have a columnar or and laminar plate. Also check how much Ni you have in those areas. This requires a rudimentary metallurgical capability.
James Watts- Navarre, Florida
September 24, 2009
A. Dear Aboo Backer,
You can try duplex nickel plating instead of only bright nickel. 6 micron semibright nickel layer, over that 4 micron bright layer and then chrome of 0.4 micron.
- India
December 1, 2012
Q. We are doing Nickel chrome plating with Nickel layer of 8 to 10 microns and 0.2 micron of chrome layer, on wrenches made from chrome vanadium steel.One customer needs 12 hour salt pray value at 5% salt solution. We get about 8 hours in many wrenches but in few it goes up to 22 hours from same lot. Pl suggest the possible reason and what should be done to improve the salt spray value say up to 15 hours. .
Krishan Sharma- Jalandhar, Punjab, India
November 17, 2012
A. Dear Krishan,
You can, as Mr. Kumba said above, do semi-bright nickel and bright nickel above (6 micron and 4 micron seems right, you can try 5 and 4 or something in between). The bright nickel is anodic to the semi-bright nickel, so you have a sacrificial protection and a barrier protection. So you can achieve more than 24 hours of salt spray for a nickel-chrome system.
Hope this works for you! Best regards,
- Cañuelas, Buenos Aires, Argentina
December 27, 2012
Thanks a lot. I shall try duplex plating.
- Jalandhar, India
January 2, 2013
January 17, 2013
A. Duplex is a good idea but not with 10 microns.
You need altogether (semi bright plus bright) 25 microns


Sara Michaeli
Tel-Aviv-Yafo, Israel
Thanks Sara and James for saying what I was leaning towards but wasn't quite confident enough to write. Still, I think 15 microns minimum thickness ought to survive 24 hours and more; but if the average thickness is 15 microns, the minimum might be a half or third of that.
Readers should remember that, unlike zinc plating which will galvanically protect steel even if porous, nickel is only a barrier layer, and it is cathodic to steel as well. The steel will rapidly rust in an attempt to cathodically protect the nickel plating if there is even slight porosity.
Regards,
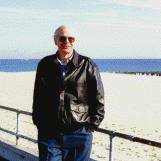
Ted Mooney, P.E.
Striving to live Aloha
finishing.com - Pine Beach, New Jersey
January 17, 2013
Q. Please tell us about sst life of nickel chrome plating( 3~ 4 micron) on CRCA components. What is the standard for sst life of nickel chrome on crca components.
Pankaj Singh- Faridabad, Haryana, India
January 8, 2014
Q, A, or Comment on THIS thread -or- Start a NEW Thread