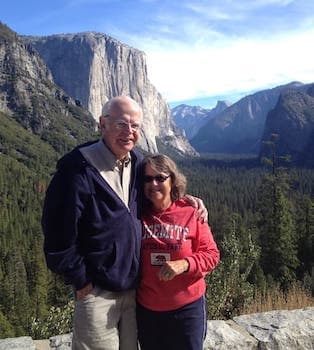
Curated with aloha by
Ted Mooney, P.E. RET
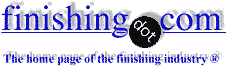
The authoritative public forum
for Metal Finishing 1989-2025
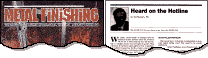
-----
Problem with Crazing on 7075 Aluminum parts after Bake
We are having our machined 7075 parts anodized per "MIL STD 171 7.2.2" We are required to bake test 18 parts at 320 degrees for 1 hour with no effects on the anodized finish. Some lots of parts fail because of crazing. We have will have months go by with no failures and then will have almost every lot fail because of this crazing. I have studied the lots of raw stock looking for variations that may have caused this problem. We have tried to create the crazing by increasing times and temperatures during the anodize process with no success. I am wondering if anyone else has seen this problem and possible solutions to eliminate the problem.
Richard Wormplating parts for Military application - Fridley, MN, USA
September 10, 2009
Richard
What are your anodizing parameters and coating thickness?
- Colorado Springs, Colorado
September 11, 2009
Sheasby and Pinner say that cracking starts at 80 to 100 °C because the coefficient of expansion of the coating (aluminum oxide) is 0.2 times that of the underlying aluminum metal. Also be aware that zinc migrates with time and/or temperature
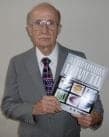
Robert H Probert
Robert H Probert Technical Services

Garner, North Carolina
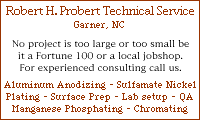
September 14, 2009
September 17, 2009
Willie,
My parameters are 165-175 gm/l Sulfuric Acid, 10-15 gm/l Aluminum, 16 volts DC for 25 minutes. Our target thickness is .0002-.0005.
Bob,
I know that coefficient of expansion between the Anodize & Aluminum is severe and this causes a lot of stress. My question is why does this not happen to all the lots of parts that are processed? We have had period of several months with no failures after baking. If the zinc is migrating with time/temperature how can we work around this problem?
- Fridley, Minnesota USA
September 18, 2009
Hi
The reason for seeing it sometimes and not other times can be due to variation in the humidity.
Have just been to Southern Metal Finishing Conference in Charleston
(hot and humid) and the oxide layer would definitely have been able to withstand crazing for a longer time here than in a cold and dry environment :o)
So high humidity in your working environment will increase the time before you see cracking of the oxide layer.
Sunny regards
Anne
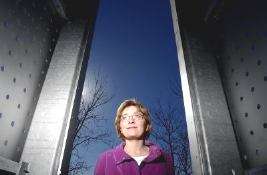
Anne Deacon Juhl
- - Trustrup Denmark
September 18, 2009
Richard
Something in the process is not stable (enough).
If you determine the material is not the cause, consider keeping your thickness to the low side, and adjusting your acid concentration, current density, and/or temperature to produce a more porous coating.
- Colorado Springs Colorado
Q, A, or Comment on THIS thread -or- Start a NEW Thread