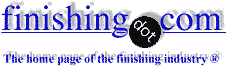
-----
Paint Peeling Problems on aluminum extrusions and castings
September 2, 2009
Hi, I'm the paint process eng. at a Mexico facility.
Our product is a al, extrusion and casting.
Our main problem is peeling, on our aluminum product.
I have two questions.
1.- Which test can we make to find the root cause?
2.- And which part of the process I need to look up?
Regards from Mexico!
Paint Process Eng. - Tamaulipas, Mexico
Hi, Victor. If the parts are exposed to any silicone anywhere, peeling is inevitable. It's more likely the pretreatment than the paint itself. The parts are probably not clean or not properly pretreated. What is the pretreatment process?
Regards,
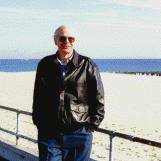
Ted Mooney, P.E.
Striving to live Aloha
finishing.com - Pine Beach, New Jersey
September 3, 2009
September 7, 2009
The pretreatment is:
1. First stage. Cleaner-alkaline degreaser ph. 10+
2.- Rinse
3.- Iron Phosphate
4.- Rinse
5. Seal
All except the rinses need temperature.
The products are from Houghton Int.
Do you think, this problem would be the cleaning process?
Because we load the material at the conveyors by hands. (We are using gloves of nitrile).
Perhaps we don't use silicone at our process (just a few caps from Shercon)and we are using kind of coolant to grind the product.
- Tamaulipas, Mexico
September 8, 2009
Just some thoughts-
make sure the temp for the cleaner is at least 120 degrees
the phosphate is a multi-metal type(contains fluorides for the aluminum)
the time in the phosphate doesn't exceed 1 to 1.5 minutes concentration 1.5-2.0, and the temp doesn't exceed 110 degrees
you need purified water (DI or RO) as your last stage instead of the sealer.
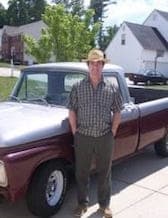
Sheldon Taylor
supply chain electronics
Wake Forest, North Carolina
Thanks.
The tanks (perhaps we have immersion tanks)are running with a normal conditions. The alkaline is with 140°F as minimum. But the time at the phosphate tank is 3 minutes, conc. is 3.0-3.5% and has
120°F. Is this a problem?
And why I need change the seal?
We are using RO water to our process.
Regards!
- Tamaulipas, Mexico
September 9, 2009
Victor,
The only point about the sealer was that it shouldn't be your last tank. I was actually giving the running parameters of iron phosphate and steel substrate, my bad since you are only treating aluminum. Fluorides added to the phosphate react to the surface of aluminum so I'm not really sure if it matters where you run your phoshate concentration and temp in your case. Maybe you could ask your chemical vender.
Here's a question, if you are only treating aluminum why aren't you using a caustic solution for pretreatment?
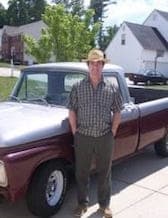
Sheldon Taylor
supply chain electronics
Wake Forest, North Carolina
September 14, 2009
Sorry I didn't tell you, we are running steel and cast iron, with the same process (not same tanks).
Degreaser, rinse, iron phosphate, rinse & seal.
But the problems are on aluminum.
And we want to change to pretreatment, using a acid stage to etch the surface (I'm not pretty sure if etch and pickling is the same).
Thank you so much..
- Tamaulipas, Mexico
September 16, 2009
Q, A, or Comment on THIS thread -or- Start a NEW Thread