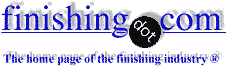
-----
Chrome Coverage Problems
I had some parts decorative chromed. Everything looks great except for the 1/2" deep .090" wide trepan groove, there is some grey colored plating in it but it doesn't shine like the rest of it, now, after a couple of days, I find that inside of the groove is rusting, this is very bad.
What can I do that will give a decorative finish and be able to penetrate down into this groove? I have 10,000 more being machined and need a new plating solution. Thank you for any help you can provide.
Donald Stegall- Eden Prairie, Minnesota, USA
2000
If after a couple of days you have corrosion on the parts, I think that your problem is not chrome related but nickel related. You do not have enough nickel deposit at the low current densities. And of course if the nickel is so thin it has terrible chrome acceptability.


Sara Michaeli
Tel-Aviv-Yafo, Israel
2000
Don,
in the quantities that you mention, there is no economic way to plate chrome in that slot. It can be done with an auxiliary anode, but that is terribly time consuming and would require a very special rack to do it since it is so deep and so narrow. I would take a very quick look at the exact requirements and see if electroless nickel might do. It is hard, has good wear resistance, is bright to very bright and is nearly a silver color. Drawback-it fingerprints.
James Watts- Navarre, Florida
2000
Thanks for the info,
to follow up on your advice regarding the electroless nickel process, when you say it fingerprints, what exactly does that mean. Does this process offer better coverage since it is a barrel process, since my current problem is that the air can't escape from the groove during the rack dip. The requirements are that this part will spend most of it's time outside. I would like it to remain corrosion free for 6 years. Thanks again.
Donald Stegall- Eden Prairie, Minnesota
2000
![]() |
Electroless nickel is not necessary a barrel process but it sure promises a much better corrosion resistance. I would describe the drawback of EN as higher price and close maintenance. If your are looking for corrosion resistance I would strongly recommend a zinc-alloy. ![]() ![]() Sara Michaeli Tel-Aviv-Yafo, Israel . By- it fingerprints- mean that fingerprints are significantly easier to see on EN than on chrome. They do not come off as easily in my opinion. I would have thought that a slit of your size would not have held air if it were mounted with the slit mounted vertically (0.090 runs up and down). If that is the true case, it will also not clean or etch well which will not plate well or in short , be useless. Barrel may have enough agitation to avoid the problem. Without seeing the part, it is really hard to even guess. James Watts- Navarre, Florida 2000 |
Dear Mr. Stegall: If you are not locked into using chrome there is a new chrome alternative that can be used. It is a tin/colbalt alloy bath that has all the properties of hex-chrome, except hardness. There are a couple out there and I myself will be R&D-ing these products. If interested let me know. Ken Hutchinson Nico products
Ken Hutchinson- Minneapolis, Minnesota, USA
2000
I clean slot machines on a gambling boat. The machines have a chrome plate on them. I need to know how to get the fingerprints off of it. What do I use and what do I not use?
Thank you.
Jessica Van Ness- Longs, South Carolina, United States
2001
Q, A, or Comment on THIS thread -or- Start a NEW Thread