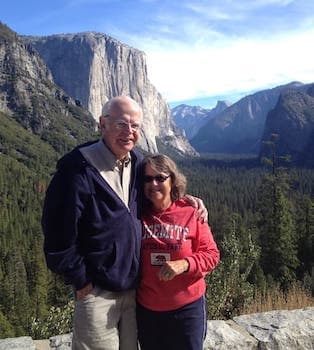
Curated with aloha by
Ted Mooney, P.E. RET
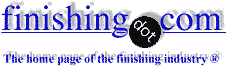
The authoritative public forum
for Metal Finishing 1989-2025
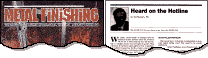
-----
Is There a Clear Chromate Product that is on QPL & Meets Spec?
2000
Q. I have asked and read similar questions before, BUT, now I am asking more specifically:
Is there a chromate (aka Iridite / Alodine), for aluminum, product available that is:
1) on the QPL
2) produces a clear color
3) meets all requirements of the spec,
MIL-C-5541 Class 1A & Class 3
Thanks
David A. Kraft- Long Island City, New York
A. Both Iridite and Alodine have a "clear" on the QPL.
James Watts- Navarre, Florida
2000
Q. I think my concern is similar to Dave's. Can these products on the QPL consistently pass the required corrosion and adhesion testing of MIL-C-5541 when applied so that they are "colorless"? Or do the process parameters needed to produce a clear coating (ie: very dilute baths, short immersion times, and/or hot water bleaching) significantly degrade the conversion coating's performance below the minimum specification requirements? My interpretation of MIL-C-5541 is that if you certify a clear coating you must perform your monthly tests on a clear coating using a QPL product.
Chris Jurey, Past-President IHAALuke Engineering & Mfg. Co. Inc.

Wadsworth, Ohio
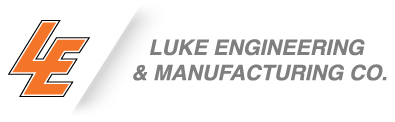
2000
2000
A. Hello, David.
Short answer to your question: No. (If one conversion coating chemical would meet all aspects of the Mil spec., the name Alodine or Iridite would represent one or two products each rather than families of products.)
Long answer: The term "clear chromate" to me is an oxymoron (like "jumbo shrimp"), as many high school chemistry students know that chromates in solution are orange (acidic) to yellow (basic). A clear chromate coating simply does not have very much chromate in it otherwise it would be orange to gold. A chromate conversion coating protects aluminum in two ways: (1)as a barrier coating, where its presence simply prevents contaminants from getting at the surface, (2) By oxidation-reduction, where the hexavalent chromium reacts with possible oxidants which would cause the aluminum to corrode. The latter mechanism is very important in protecting aluminum alloys which have alloying elements within them such as copper, which with a little moisture, and especially in the presence of chloride as a catalyst, set up a classic galvanic couple with copper as the cathode and aluminum as the anode, which causes the aluminum to corrode.
That brings us to the MIL specs, where the Class 1A requires the coating to protect 2024 alloy (which has 4.5% copper) such that it passes 168 hours salt spray. (But to get on the QPL-81706 the product must withstand 336 hours salt spray). There is not enough chromate in a clear coating to protect 2024 for 168 hours in salt spray. By the way, there are other ways to chemically oxidize aluminum with a clear coating. All of them provide only the protection in (1) above, and because they are all porous, they do not sufficiently protect 2024 in salt spray. For most of our products we recommend a minimum coating weight of about 40 mg./ft2 to pass salt spray, and prefer at least 60. At these coating weights, these coatings are the nice golden/orange color typical of gold chromate conversion coatings.
I'm going to get commercial here to make my point. MacDermid has a full line of Iridites, but I am only familiar with our Alodine line. I am guessing that some of the confusion here may come from the fact that products such as Alodine 600 and Alodine 1200S are on the QPL for both Class 1A and Class 3 coatings. Both of these products are typical gold chromates. The catch here is that nowhere in MIL-C-5541 does it say that Class 3 coatings MUST be colorless. In fact, the spec states that colorless coatings must be specified, that is, they are a special case of Class 3 coatings. As Alodine 600 and 1200S are specifically designed for corrosion resistance but happen to meet the resistivity and corrosion requirements of Class 3, it would be very difficult to get a colorless coating from them. That is why we offer Alodine 1000 and 1500, which are specifically designed to be clear. These latter two won't meet the salt spray requirements of Class 1A because they won't protect 2024 in ! salt spray, but they do provide the corrosion resistance requirements of Class 3, which specifies passing salt spray with 6061 T6 alloy. Without relatively high amounts of copper in the alloy, the barrier mechanism of (1) above is enough to pass salt spray.
To those who are thinking of bleaching out the gold chromates to achieve a colorless coating, remember that you are removing the chromate, which is still soluble until the coating dries and cures. (Did you ever try to bleach out an aged gold chromate? It won't work.) A porous oxide is left behind, which will not provide the redox type of corrosion resistance described above.
One catch in the Class1A requirements may help here, but only if you are not required to strictly abide by the QPL-81706: the latest revision of MIL-C-5541 allows you to pass salt spray with the alloy you are working with, so if you work with one or two non-high copper alloys, you don't have to pass on 2024 but on the alloy of your parts. This could mean that a clear product could provide sufficient protection to meet that Class 1A requirement. However, to my knowledge none of the clear products on the QPL are approved for Class 1A coatings. I know that I would hesitate to sign my name to any certification with this situation unless salt spray panels were run with the parts and passed salt spray before the parts were shipped.
Our company has been working for many years, and for the last ten years in a joint project with our largest chromated Alodine customer, on replacing chromates in conversion coatings, due of course to the environmental nightmares that hexavalent chromates provide. We are getting very close, but I can tell you that the largest hurdle that we have had is to provide this redox mechanism with chemistries that are environmentally friendly. We have learned first-hand that the chromates or some other reducing agents must be there to prevent that copper/aluminum galvanic corrosion.
If this "long answer" is too complicated, bottom line is: gold chromates for Class 1A coatings, clear to light gold coatings for Class 3. If you need a clear coating with high corrosion resistance, anodizing may the best answer. If you need high corrosion resistance and low electrical resistivity, you've got a major design problem.
Phil Johnson
- Madison Heights, Michigan
Q. Is there an appreciable difference in the conductivity of bare 6061-T6 aluminum and that which has been conversion coated to MIL-C-5541E?
Vincent B. Keenanorbit/fr - Horsham, Pennsylvania
2000
Q. Dear All,
May I use Alodine 600 as alternate of Alodine 1000 ? What's is the differences of them? properties? usage? process?.
Thank you,
Engineering design - Bandung, Indonesia
December 16, 2008
A. As to clear chromate conversion coatings that are listed on the QPD for Mil-DTL-81706, you really only have one choice and that is to only offer Type II for your clear requirements. The Type I clear coatings are accomplished by a reduction in concentration or time in solution, both of which compromise the performance of the coating.
Ed Peters- Frederick, Maryland USA
February 22, 2016
Q, A, or Comment on THIS thread -or- Start a NEW Thread