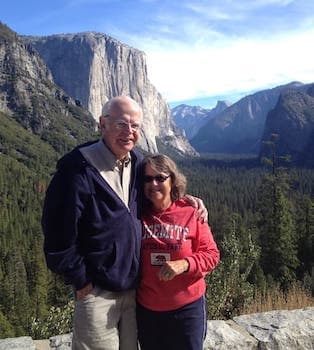
Curated with aloha by
Ted Mooney, P.E. RET
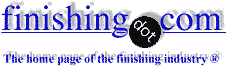
The authoritative public forum
for Metal Finishing 1989-2025
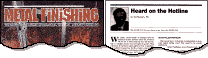
-----
Corrosion on 316SS Castings after Passivation
We are currently having a problem with cast 316 stainless steel and corrosion. After a normal passivation in a Nitric Acid bath, the surface of the casting is corroding (surface rust). There seems to be free Fe at the surface that is NOT being removed with passivation. Can someone please give a suggestion to eliminate this issue? We have done analysis on the material and it has come back with in the acceptable range for 316SS. We are in the process of trying electropolishing but are not sure what the effect will be.
Stefan Koveal- Concordville, Pennsylvania
2000
2000
You would be amazed at the amount of iron that can be smeared and imbedded into the surface of SS. Using high speed steel inserts will do it, clamping will do it, movement across the table of a band saw will do it.
Passivation only attacks the extreme top surface of the smear (Fe). Repeated cycles will help some. Lengthened time in the passivation will do very very little. The best apparent answer is electropolish. This works extremely well, but is a higher cost process. Several vendors have links from this site. Check the vendor listings.
James Watts- Navarre, Florida
Nitric acid passivation is good the day the nitric is new and its all downhill from there. The desire to not buy new nitric and the disposal costs work in tandem to keep the solution in the tank far past its prime. At some point it quits passivating and becomes an iron immersion coating.
Our new Selective Abstraction Passivation gives the optimum passivation possible at all times. I think we all agree that electropolishing is the best form of passivation, but the cost and the appearance is not always required. SAP will provide the best passivation short of EP and does not change the surface finish.
Dan Weaver- Toccoa, Georgia
2000
Another potential problem with stainless steel castings is porosity or nonmetallic inclusions. When microscopic porosity or large inclusions are present at the as-cast or machined surfaces, passivation solutions may not be fully removed by post-passivation rinsing. Subsequent corrosion by the retained acid will bloom 'rust' to the surface. Better control of surface condition of the castings or more aggressive rinsing after passivation will be required to prevent the rusting.
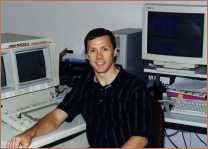
Larry Hanke
Minneapolis, Minnesota
2000
Stefan,
4 years ago a metallurgist associate of mine and I figured out how to cast 304 into ferritic sand. (Yes I know you aren't supposed to do these things). We were able to assist a v.large multi-national solve a huge problem. Few people would believe what we did until they saw the results with their own eyes. The results are in daily use on the rail tracks of a major American city! Cheers
Hamish Hunt- Melborne, Australia
2000
Q, A, or Comment on THIS thread -or- Start a NEW Thread