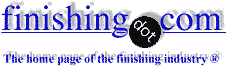
-----
Acceptance Criteria for 300 Hrs. Salt Spray Test on Epoxy Primer Coated MS Components
I am going to conduct 300 Hrs. Salt Spray Test, ASTM B117 on MS Tubular components with having surface pre-treated and Epoxy Primer Coated.
What 'Acceptance Criteria shall I keep?
manufacturer - Ahmedabad, Gujrat, India
August 27, 2009
August 31, 2009
Hi, Nandoo. Oftentimes you will pretreat and paint to a particular spec, and that spec will specify the acceptance criteria. If there is no spec involved, your choice is to either find a spec and use its acceptance criteria, or to invent your own acceptance criteria. It is usually faster and easier to find someone else's rather than to write your own.
You could try finding a USA military spec that seems close, and use its acceptance criteria. American mil specs are available for free at
assist.daps.dla.mil/quicksearch/
American small businesses are taxed to provide this free service to their offshore competition :-)
Regards,
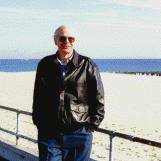
Ted Mooney, P.E.
Striving to live Aloha
finishing.com - Pine Beach, New Jersey
September 4, 2009
Unfortunately, as you have not provided any basic information I don't think anyone can provide an answer to your question. You need to inform the reader:
1)What pre-treatment is being used? Shot-blasting, iron phos, zinc phos or just cleaned to remove oils and dust.
2)What type of epoxy primer is used? Solvent based with or without anti-corrosive pigment and is it air-dried or baked?
Or could it be:
3)Powder coating epoxy primer?
4)What film weight is applied?
To give you an idea what you require, MS that has been pre-treated using zinc phos process, followed by a correctly formulated anti-corrosive liquid epoxy primer or an epoxy powder primer should show no sign of corrosion creep away from the cross-hatch at 300 hour point of the ASTM B117 test.
Most requirements are for 500 - 1000 hours rising to 2000 - 3000 hours in some later specs.
Birmingham, United Kingdom
Q, A, or Comment on THIS thread -or- Start a NEW Thread