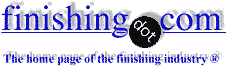
-----
Tin Plate Rusting
August 23, 2009Hi There,
I have noticed that there has been quite allot of dialogue in terms of tin plating rust here but I can't seem to get an answer for my specific situation so I thought I'd ask it directly.
I am currently working on a product that uses a tin coated plate approx. 1mm thick. Each plate is stamped out of a sheet of tin coated steel prior to being used on our product. I have noticed recently that on some units there is rust around the perimeter of the clips, however the majority of the units don't show signs of this? I understand stamping out the plate will cause non coated steel to be exposed but why the discrepancy? Also recently, (and alarmingly), there have been plates coming through with spots approx. .5mm in diameter appearing in clusters on the surface of the plates which are supposed to still have the protective tin layer? I noticed from an earlier letter that coating thickness could be a factor that I can push back to the supplier but could this be caused via another mechanism? Is there anyway to rework the affected area so that further rust can be prevented?
Any Help would be greatly appreciated!
production line manager - Thailand
Hi, Samuel. Tin plating does not sacrificially protect the underlying steel. That means that parts that are stamped from preplate are likely to rust at the exposed edges in anything but an extremely benign environment.
Unfortunately, the parts that are not rusting may be zinc plated rather than tin plated. People use the colloquial term 'tin' to refer to 'sheet metal', which is actually steel with or without zinc plating -- and this confusion of terms may be part of the problem.
Regards,
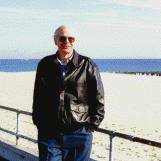
Ted Mooney, P.E.
Striving to live Aloha
finishing.com - Pine Beach, New Jersey
August 25, 2009
Samuel, Tinplate is funny stuff. Firstly, if you cut it, you will expose the base steel in the cut edge. This will rust if exposed to the correct conditions, so it is often a good idea to coat the cut surfaces with a lacquer.
Secondly, there is not much tin on tinplate - typically there are 2.8 g/m2 of plate; this is normally good enough for most products, especially cans, but it can be porous, so a thicker coating is advantageous. Over the past 20 years or so there has been a trend towards thinner tin coatings, but this has almost always resulted in extra problems and it has usually been abandoned. I would suggest you check the tin thickness and perhaps specify a thicker coating.
Thirdly, when tinplate is made nowadays, the tin is electrodeposited and then flash melted; this creates an intermetallic layer of FeSn2 between the tin and the steel and this can offer some extra protection to the steel; the flash melting will also usually help seal the surface , but if the steel base is slightly dirty, it will result in increased pores. However, when thin tin layers are melted, the amount of tin consumed in the FeSn2 becomes disproportionate and the tin thickness is significantly reduced.
Your pores of about 0.5mm are larger than a normal pore, so I would think they have been caused by the tinplate being exposed to either acid or alkali spray or droplets. tin is amphoteric and will dissolve in both acid and alkali. This problem can be reduced by ensuring the tinplate is coated in a thin layer of oil immediately after it has been manufactured
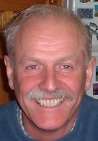
Trevor Crichton
R&D practical scientist
Chesham, Bucks, UK
September 9, 2009
Q, A, or Comment on THIS thread -or- Start a NEW Thread