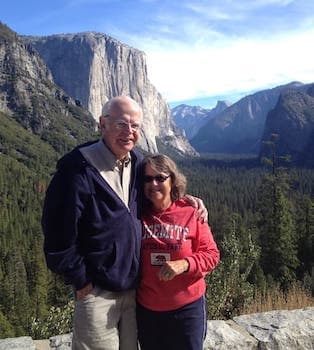
Curated with aloha by
Ted Mooney, P.E. RET
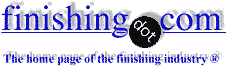
The authoritative public forum
for Metal Finishing 1989-2025
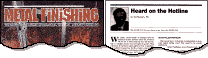
Thread 529/13
What metal can be permanently magnetized and remain stainless and workable as small washers
August 19, 2009
Q. I would like to know what metal can I use, which must remain stainless and absolutely not rust and which at the same time can be permanently magnetized.
I need to manufacture small washers with diameter 2.0 mm, thickness 0.5 mm and laser drill small holes on them, which are in diameter of 0.02 mm to 0.10 mm. Then I need to permanently magnetize them. The metal to be used must remain stainless and as such that the humidity, rust and water does not block the small 0.02-0.10 mm holes while they must remain open.
I would be very thankful, if someone could help me in this question and give some information as well how to magnetize the washers with the strongest possible magnetic power and permanent result.
Jukka I [last name deleted for privacy by Editor] medical instruments - United Kingdompublicly reply to Jukka I
![]() |
"Driving Force:The Natural Magic of Magnets"
by James D. Livingston on AbeBooks or Amazon (affil links) A. I do not think that there is any metal that will reach the Utopian status that you are seeking. - Navarre, Florida August 22, 2009 publicly reply to James Watts A. All metals are subject to oxidation when exposed to humidity. Even stainless steel. I think alternatives would be better. - Toledo, Ohio August 22, 2009 publicly reply to Robert H Kinner August 22, 2009 A. I have spent quite a long time reading about magnets as they massively affect the sound of any musical pickups that rely on them or speakers that use them in the drive coils. I was also interested in them due to their use in magnetic suspension in things like turbo molecular pumps. But I can't profess to know everything possible with them. - UK publicly reply to John Heritage A. Firstly, no stainless steel is totally corrosion resistant, so there must be a compromise between materials and its operating environment. Secondly, only 200 and 400 series stainless steels are magnetic, although 300 series will become slightly magnetic under some circumstances. You may find the 200 series offers you the best option (201, 202 perhaps). ![]() Trevor Crichton R&D practical scientist Chesham, Bucks, UK August 23, 2009 publicly reply to Trevor Crichton |
A. Dear sir.
you can go in for ss grade 316 and coating of titanium nitrate coating by PVD process on the metal completely finish your operations before send ing for coating it may be 5 microns to 8 microns. the mat'l should be completely magnetised before sending for tin coating also alternatively you can try ceramic coatings to 5 microns which will prevent 100% corrosive.
with warm regards.
- Bangalore, India
September 14, 2009
publicly reply to B. Manickavelu
? Hi Sir
We could really do with some more information here. Stainless against what environment - in vivo? in vitro? What orientation for the magnetic field?
I would speak to magnet manufacturers first. What you need may be available off the shelf! What you describe sounds very like the ferrite cores once used for computer memories.
If you are thinking of implants, gold plating may be the best option.
One more thought. Consider any coating process before magnetising. These tiny magnets will coalesce into an unmanageable mass unless kept separate so barrel plating would be a problem
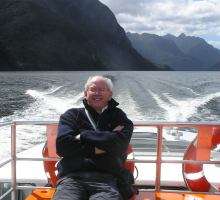
Geoff Smith
Hampshire, England
September 24, 2009
publicly reply to Geoff Smith
Q, A, or Comment on THIS thread -or- Start a NEW Thread