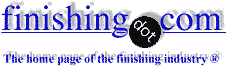
-----
Improving "Hard Use" Custom Knives through coating
Gday folks, I am a low volume custom knife maker. High performance knives require exceptional hardness, wear resistance, toughness, strength. This means using tool steel alloys so corrosion resistance is an issue too.Materails include S7, A8 modified and CPM3V.
Typically, my knives are heat treated to a blade hardness of 61 rockwell c, and the spine differentially hardened to 55 Rc.
I am considering how industrial plating or some other process may result in higher hardness and better wear resistance, possibly enhanced corrosion resistance as well. Boron carbide, nitriding. Or possibly multiple processes such as nitriding and galvanising to a smooth surface finish.
Is it possible to achieve an industrial metal finishing that is highly resistant to being abraded off and has the toughness to resist shocks?
Thanks
product designer - Canberra, ACT, Australia
August 15, 2009
August 20, 2009
The short answer is yes. If you look in any of the surface engineering journals or machine tool catalogues they will be full of coatings for cutting tools each one claiming better wear and shock resistance, prolongling life and reduced down time in machining. As an example TiN coated drill bits are readily available to the home DIY market.
I've never seen anyone apply them to knives but unless size is an issue I can't see why they wouldn't have the same effect. The latest articles are talking about multiple nanolayers of coatings alternating between 2 or 3 materials.
The issue may be that one these layers are damaged I am not sure whether you would then have difficulty in sharpening the knife subsequently.
Aerospace - South wales UK
Whatever you do to the blade prior to coating will remain, say glass beading or highly sharpening the edge... as the thickness of the films deposited over the substrate, in this case your knife, are very thin... but extremely hard and durable. Your knife will remain sharp for a very extended time. These coatings are generally applied via vacuum deposition, so it will be difficult to find a company to do your individual piece, and probably expensive as well.
J RussellThin Film Coatings - Providence, Rhode Island
August 28, 2009
Sporting knives have been PVD coated since the early 1990's. Buck was the first to adopt the technology, and it was patented by Molecular Metallurgy. You can probably find someone in your area that can do the work.
Nitrides provide the best wear protection, though some blades are now coated with diamond-like carbon coatings. Most do not provide much in the way of corrosion protection. The coatings are too thin, and full of pinholes.
We ran some tests a few years ago on the corrosion protection of hard nitrides deposited on mild steel. TiAlN provided no improvement whatsoever. TiN was not bad. The big surprise was ZrN. The test was the ASTM B117 salt fog test. After less than an hour, uncoated samples were completely covered in rust. Oiled zinc phosphatized samples made it to around 16 hours. But the ZrN-coated samples were pretty rust free after 24 hours.
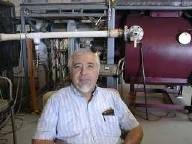
Jim Treglio - scwineryreview.com
PVD Consultant & Wine Lover
San Diego, California
September 2, 2009
Q, A, or Comment on THIS thread -or- Start a NEW Thread