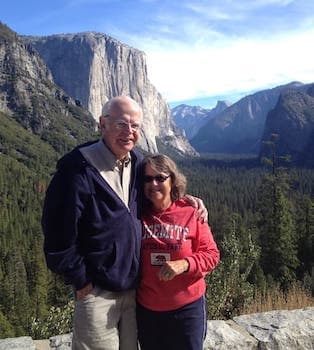
Curated with aloha by
Ted Mooney, P.E. RET
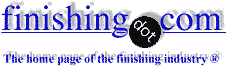
The authoritative public forum
for Metal Finishing 1989-2025
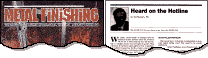
Thread 528/30
Minimum thickness for black anodizing?
Q. Hi All,
I run a small anodising shop and wanted some expert advice. We currently run our anodising at 12% sulfuric for type II. At present we ramp to 10V and hold for 5 minutes and then ramp to 16V for a further 30 minutes. Whilst we seem to get good results on our colours, the black is never black black, more dark grey. I am open to any help I can get as we are gaining experience through trial and error on some jobs. Our vat's temperature is currently controlled at 20 °C
Look forward to any advice and thanks in advance
- plymouth devon england
July 6, 2021
publicly reply to Craig short
A. Hi Craig. It's possible that your black dye isn't good enough, but you probably thought of that already.
The thing which makes black anodizing different from most other colors is that it must be really, fully, saturated to absorb all colors ... and for that it must be thick. You may know this, but to help beginning anodizers understand: anodizing involves building a layer of oxides with "pores" (microscopic drill holes) which extend from the surface most of the way to the substrate. The dye doesn't go on top of the surface, but into those pores. A rather thin layer is enough for pastel colors, but a thicker layer is required to generate good saturated colors, and a thicker layer still for black.
Most shops probably consider 0.0005" anodizing the minimum for black, but many shops making high quality stage equipment, etc. will insist on at least 0.0006" or more.
Please tell us what alloy you are anodizing, and what anodizing thickness you are achieving.
Luck & Regards,
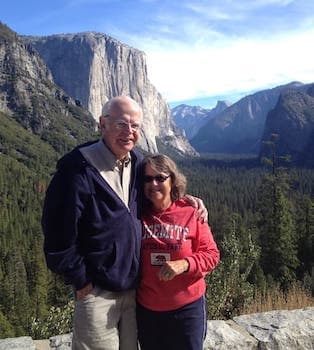
Ted Mooney, P.E. RET
Striving to live Aloha
finishing.com - Pine Beach, New Jersey
July 2021
publicly reply to Ted Mooney
A. When you respond to Mooney's list, please also clarify the acid concentration. If 12% by volume of 66 degree Be acid, then it is a bit high which causes a larger pore and adsorbs more dye but does not seal well. IF it is 12% by weight, it is low, which along with 20 °C (instead of 22 °C) causes a smaller pore which adsorbs less dye. Also tell us whether you see "bleeding" after sealing.
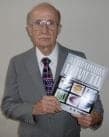
Robert H Probert
Robert H Probert Technical Services

Garner, North Carolina
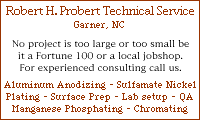
July 7, 2021
publicly reply to Robert H Probert
A. I fully agree with Ted. Additionally, in order to get black color, voltage of anodizing should be a little bit higher than 16 volts. If I were you I would try 18 or 19 volts to get min. 15 micron and more...
Apart from anodizing bath conditions, you should consider electrocoloring bath's parameters. So tell us coloring bath's parameters such as voltage (AC), ramp duration/voltage and analytical values (Sn+2, sulfuric acid and if you use stabilizer). Normally, black color is got between 10-15 minute from electrocoloring bath.
Alaattin TunaAnodizing Supervisor - Sakarya
July 10, 2021
publicly reply to Alaattin Tuna
Hi,
Thank you for the replies. We currently anodise to 15 microns. My concern is at 12% strength and 16v we may be growing the oxide layer too quickly and this would lead to a tighter structure. Some advice I have been given is to anodise at 12v for longer, but as a business this adds considerable time
- plymouth england
publicly reply to craig short
⇩ Related postings, oldest first ⇩
Q. Hi anyone
I intend to anodize sheets of aluminium (AA5182) with the size of 3 * 1.5 m. The desired color is black and I am wondering what would be the minimum thickness for obtaining a reasonable aesthetic effect. The scratch resistance is not that relevant as the products will be used in office environment and I think that any type of anodizing will offer that required resistance.
Another question is related to the panel sizes: I was reading on several posts about the problems with big sheets as they might create uneven color. Do you know anything about this? Do you have suggestions for the process?
Thank you
Marius
ergonomics - Dubai, UAE
August 9, 2009
publicly reply to Marius Moldovan
![]() |
South Carolina A. Marius, ![]() Tim Hamlett, CEF - West Palm Beach, Florida, USA August 11, 2009 publicly reply to Tim Hamlett, CEF A. It is very difficult to get the current evenly distributed on thin sheets, make contact in several places. Better still, use an aluminum v-block on the bottom and just depend on titanium clips at the top to hold the panel in place. ![]() Robert H Probert Robert H Probert Technical Services ![]() Garner, North Carolina ![]() August 11, 2009 publicly reply to Robert H Probert |
Aluminum Alloy 6061 Black Anodizing: Coating Thickness
Q. I am new to anodizing and am curious about measuring the coating thickness of the piece being anodized. For instance, if I were to anodize a piece and dye it black, would the coating thickness be the layer of oxide after anodizing, or would it be the combined layer of oxide plus dye (correct me if I am wrong, but I assume that the dye also adds a certain thickness)?
Chiraag Bhawnani- Atlanta, Georgia, USA
September 4, 2019
publicly reply to Chiraag Bhawnani
A. Hi Chiraag. No, the dye has no thickness. The dye is absorbed into pores, microscopic 'drill holes' in the anodizing. When you read that black anodizing is thicker than other anodizing, what people are actually referring to is the fact that to get a good, saturated, black color the anodizing has to be rather thick to be able to absorb enough dye -- as Tim & Robert Probert say, 0.0005" or preferably more. When doing a light pastel color, not requiring much saturation, it is possible to use thinner anodizing like 0.0002".
Regards,
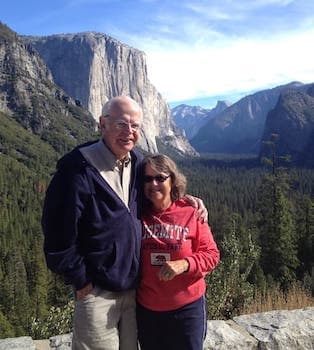
Ted Mooney, P.E. RET
Striving to live Aloha
finishing.com - Pine Beach, New Jersey
September 2019
publicly reply to Ted Mooney
Minimum aluminium thickness for anodising
Q. We have some very thin, very small components for black sulfuric anodize (25µm). They are less than half a mm thick and are partially dissolving during the etch process. This is the second time we've attempted this job and we've had the same result both times. Any advice?
Jane McMullenPlater - Dorset, UK
September 17, 2019
publicly reply to Jane McMullen
![]() |
A. Firstly I advice trying acid etch process which does not involve as much as in normal etch process, or secondly if I were you I'd skip the etch process for this black anodizing. Etching is not necessary for black anodizing if custumer accepts that appearance. - TURKEY,sakarya September 17, 2019 publicly reply to Alaattin tuna A. Even if you get by the etch loss by skipping it, be reminded that, from both sides, the coating goes 50% under the original surface and 50% over the original surface +/- 10%, then all you would have left is solid aluminum oxide (very brittle and would fall apart). ![]() Robert H Probert Robert H Probert Technical Services ![]() Garner, North Carolina ![]() September 17, 2019 publicly reply to Robert H Probert |
Q, A, or Comment on THIS thread -or- Start a NEW Thread