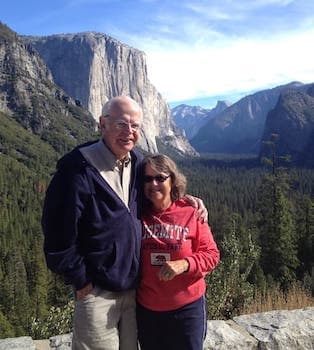
Curated with aloha by
Ted Mooney, P.E. RET
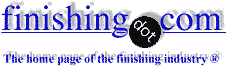
The authoritative public forum
for Metal Finishing 1989-2025
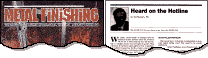
-----
Would coil anodizing be best?
July 31, 2009
Hello Everyone,
It's not very often I post on this side of the conversation... let's hope I remember to include all the useful information I typically wish other people remembered!
I've got a situation where coil anodizing (reel to reel, continuous tape, etc.) seems to be the proper solution, and I'm curious whether or not the rest of you have any better suggestions. I also posted a RFQ in that portion of the page, if you would like to make direct contact with a quote.
Our ultimate goal is to have a metal part that is shaped roughly like a funnel, with a non-conductive inside coating, good thermal conductivity (which is why we are looking at aluminum), and a pleasing visual appearance on the outside.
The part itself is about 1/2 inch by a 1/4 inch and the aluminum is similar to a heavy foil - 0.004" thick. The anodize that we are looking for would be a standard Type II class 2, preferably dyed gold using FAO and sealed in nickel acetate.
The alloy hasnīt been decided on yet, and we would be absolutely open to suggestions (not being overly knowledgeable about coil anodizing, Iīm not sure which alloys do the best in terms of being able to shape or bend slightly AFTER anodizing -- which always trips me out).
Being a huge proponent of bulk anodizing, I thought about going that route - but the parts are just too thin to live up to the conditions. So, in the interest of trying to find the next cheapest alternative, we are now thinking about going with coil anodizing and following one of two paths:
1) shape the part but leave it on a 1 inch wide tape (a few abreast) (ultimate length to be determined, unimportant to needs - could be anything from a few feet up to hundreds of yards. Open to suggestions.), coil anodize it, punch it out for use.
or
2) get the tape anodized, then shape and punch (I'm betting this option wouldn't work - I think that the stretching of the metal would cause the anodize to crack too much to be of use).
Of course, like I indicated in the header, I'm also completely open to suggestions. The primary goal is to have the inside be non-conductive, the outside be pleasant visually (it will be visible to the end user), good thermal conductivity, and the coating to be CHEAP per piece.
Any thoughts or suggestions?
Thanks - Jim
former member with a bunch of ties, now a buyer and product designer - San Diego, California
Hi, Jim. The electronics industry did a lot of "bandolier plating" (I don't travel to plating shops as much these days so I'm not sure if it's still as common). But picture bullets in machine gun belts, and you'll have the general idea of bandolier processing.
The parts are automatically inserted, by vibratory feeder bowl equipment, into plastic carrier strips that convey them through the various process tanks. Because they are held in proper orientation, it's easy to process just one side. In some cases, rubber gasket material is used as a moving mask to keep some areas covered for selective processing.
It's expensive in terms of initial engineering and set up, but very inexpensive in terms of labor cost.
Regards,
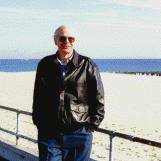
Ted Mooney, P.E.
Striving to live Aloha
finishing.com - Pine Beach, New Jersey
March 13, 2010
Q, A, or Comment on THIS thread -or- Start a NEW Thread