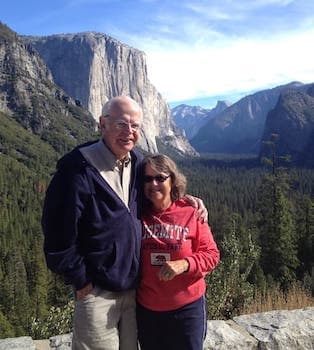
Curated with aloha by
Ted Mooney, P.E. RET
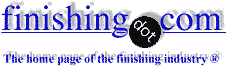
The authoritative public forum
for Metal Finishing 1989-2025
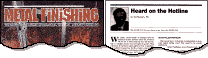
-----
Reduction in hard chrome plating hardness from grinding
July 30, 2009
We had hard chrome plated a component to 175-200 microns, checked the microhardness which 950 HV+, and after post grinding with residual thickness of 60-70 microns again the microhardness was checked .It showed 720-730 Hv
while grinding care was taken to take small cuts and with coolant
Wondering what could have caused the reduction
can anyone guide on this subject
Plating shop owner - Ambernath, Maharashtra, INDIA
![]() |
"Hard Chromium plating"
by Robert K. Guffie ![]() on AbeBooks (rarely) or eBay (rarely) or Amazon (affil links)
"Chromium Plating"
July 31, 2009by Weiner & Walmsley ![]() on AbeBooks (rarely) or eBay (sometimes) or Amazon (sometimes) (affil links) Simply stated, your measurement system is invalid! - Navarre, Florida Are you measuring hardness parallel to the surface or perpendicular? If the last then you are taking a reading that is influenced by the substrate lower hardness. The thinner the chrome the more deviation. Plating and other thin coatings and surface treatments must be checked by a micro hardness indentation parallel to the surface. Otherwise, thickness must be at least 6 to 8 times the depth of indentation to eliminate influence. Guillermo MarrufoMonterrey, NL, Mexico August 2, 2009 |
when we measured the hardness parallel to surface the hardness was
950+ and when we measured it perpendicular it showed 730.
But there are other components were we get more hardness when checked perpendicular to surface.
also we observed that on one more component,when the hardness was checked perpendicular to the surface it showed 1050, but we could see mud crack effect.
could that be because of grinding ?
- Ambernath, Maharashtra, INDIA
August 4, 2009
August 5, 2009
For true readings, you must check it perpendicular. I think that you are not polishing the sample adequately causing the indentor to strike in high spots as well as on the point , which will give you a false reading -low.
The only way grinding can lower the hardness of chrome is to burn it and that almost always will cause it to peel, especially on a 70 micron thickness.
PUS: You are getting extremely hard chrome if you are over 1100. This would further make me believe that you are not using your hardness tester correctly.
- Navarre, Florida
August 10, 2009
Hello,
which method are you using. Principle-wise you can measure the hardness with thickness of 70 microns. Depends on method and weight which you use. The diamond print leaves a 10% diamond shape in vertical and diagonal according to thickness of the to be measured substrate.
Regards
- Mexico City, Mexico

Q, A, or Comment on THIS thread -or- Start a NEW Thread