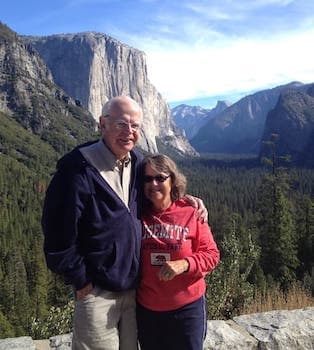
Curated with aloha by
Ted Mooney, P.E. RET
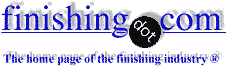
The authoritative public forum
for Metal Finishing 1989-2025
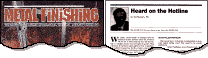
-----
Plating Process Control Sheet Template
Q. Hi, I am an engineer from surface finishing company. I do have a question on the process control limit.
How do we decide the frequency of chemical bath concentration analysis? Do we have any handbook or specification that mention about the frequency, or we just depend on the manpower/ workload?
Engineer - Malaysia
April 13, 2025
Tip: This forum was established to build camaraderie among enthusiasts through sharing tips, opinions, pics & personality.
The curator & some readers who publicly share their info will be less likely to engage with those who don't.
A. Hello Hong,
If it is not otherwise given in a governing standard required by your customer, the test frequency for each parameter will ultimately depend on the size of the allowable range and the expected rate of change based on your typical workload. For example an example of the first case, in order to comply with chromate conversion coating of aluminum per MIL-DTL-5541
[⇦ this spec on DLA], you are required to perform your solution analyses at least weekly, regardless of how they actually trend over time. As an example of the second, the concentration of a component in one of our descaling baths drops from nominal to the lower control limit in about 4 to 6 days of typical operation. Consequently, we test it every three to make appropriate adds before it trends out of control. SAE International offers a document "ARP4992" which can help you determine the appropriate frequency of analysis for each of your tests based on their performance over time. The document is written with the aerospace industry in mind, but is appropriate for anyone looking to maintain good control of their baths.
Best of luck,
Plating Engineer - Minneapolis, Minnesota
April 21, 2025
⇩ Related postings, oldest first ⇩
Q. My question is related to the maintenance of all process solutions. When the process solutions go out of spec what do you do with the parts? The process solutions that I am referring to are: Chromate Conversion Coating, Anodize, Etching, Deoxidizing, Alkaline Cleaning, Degreasing, etc. The Quality lab tests all of the solutions used by production, once per week. When a solution is nearing its useful life it has always been difficult to explain what coarse of action is acceptable. Quite often the solutions are dumped prematurely. Quality management wants to know if a tank goes out of spec. do the need to reject all parts run during that week? My answer, as a Manufacturing Materials & Process Engineer, is that the parameters used to each solution are guidelines. Parts processed outside these guidelines are considered to be acceptable based on acceptable performance tests further down the production process ie. adhesion, salt spray, etc.
John P. McLaughlinaerospace - Moosup, Connecticut
1999
SPC = statistical process control
A. It has been my experience that even when the process analysis goes outside of specification limits, most people will continue to accept the parts as long as they pass cosmetic or performance criteria. I think there is a tendency for the "engineers" to create analytical limits that are far too tight. Many plating and surface finishing solutions are far more forgiving than we give them credit for, and can often be nursed along until you have the time to make the chemical adjustment, or dump and start over. Consider two set of limits: Control Limits, and Specification Limits (terms obviously borrowed from SPC). The first set are tighter and serve to trigger action such as chemical additions, dummying, or carbon treatment. They are the warning that it is time to do something, but you can still use the bath. The second set are the "DO NOT CONTINUE TO USE THIS PROCESS UNDER ANY CIRCUMSTANCE" limits. Shut down when you get there. Analyze your bath whenever you think you are going to be near the Control Limits. You can do a higher frequency of analysis until you have a sense of the necessary schedule. A week is way too long to wait for some parameters. For others once a month is often enough. You have to study the process to know what is right.
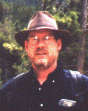
Bill Vins
microwave & cable assemblies - Mesa (what a place-a), Arizona
A. We have found it useful to establish two criteria for tank chemistry control. The first uses the SPC concept of control or action limits. If the bath parameters fall outside of this range then some action is required. (i.e., add chemicals, regenerate acid, or dump bath.) The second is a wider specification or never exceed limit. If the bath parameters falls outside of this range then unacceptable products could result and the production should be quarantined pending further testing.
Chris Jurey, Past-President IHAALuke Engineering & Mfg. Co. Inc.

Wadsworth, Ohio
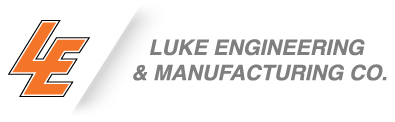
A. Just to add one more item to excellent suggestions above: Implement a "deviation Signature procedure" for every lot processed after control limit is reached. This is signed by line engineer and approved by Engr. Mgr. Keep track of all deviations signed and number of parts processed. Over a period of time, it will allow for modifications in control limits. Plus, it will force an action from Engg/production dept. This worked like a charm in where I worked before.
Mandar Sunthankar- Fort Collins, Colorado
A. The Boeing position in this type of situation is as follows: Any parts produced in a solution which is identified as an out of specification condition must be rejected by Quality and sent in with a tag identifying it as discrepant material. The time frame for the out of spec. solution parameters can be identified from the last analysis and extrapolated to the current date. Engineering then can make a decision based upon physical testing, how far the solution is out of spec., etc. Parameters listed in our specs., are required, they are not merely guidelines. Frequently, chemical manufacturers will have a wide concentration range depending upon circumstance like soil loading etc., those make their way into specifications, however many solution parameters are critical, as in phosphoric acid anodize, or silicates in anodize seals for example. Further, any tank solutions when identified as out of spec. can not have parts processed through them. Process control tests such as salt spray, coating weights, are typically performed on a frequency ! determined by time, monthly, weekly etc. Usually, the time frame the process control tests are performed in, is not the same as when the parts are actually processed. Typically, Quality will determine through history an action through prevention to eliminate this type of situation in the first place. One strategy used is "bleed & feed" in order to maintain solutions almost indefinitely. Another strategy is quasi-SPC using moving range calculations.
Ward Barcafer, CEFaerospace - Wichita, Kansas
A. I've read some good advise above and wholeheartedly agree with using SPC with two levels of action/alarm. The first being "process warning alarm" and the second "process out of spec warning". When the process reached the first level, it is time to take action to adjust the process back within those fairly tight limits. The second alarm is used to recognize when the process is about to go haywire, but still well before it actually causes performance problems. Next, I'd like to suggest two other ways in which to determine solution-life oriented controls.
PM = periodic maintenance
TDS = total dissolved solids
1. Production oriented limits. This is a simple calculation that any engineer worth his salt can do. Count the number of parts, square feet, cubic feet, pounds, etc. of production that have been put through each bath before it is dumped (based on performance criteria). You only need to do this through three dump cycles for it to be "statistically significant". And you have just set up a preventative maintenance-type dumping schedule. Of course, the dump schedule may be different for each tank (more than likely). If you adjust the PM schedule for each tank forward slightly (a few days or weeks), you'll never get to the point where you have to dump for performance reasons (in theory).
2. Soil loading. cleaning tanks can be monitored for the amount of soil build-up (called "soil load"). Determining the limit is the same as above. Take a sample just before the tank is dumped and measure the "soil load". This will establish the limit. The same is true for rinse tanks and etch tanks. The "soil load" is determined differently for each tank. Rinse tanks for example the soil load could be TDS or ppm of cleaner dragged in. Cleaner tanks are generally measured for the percentage of oil in the tank, because as oil builds up in the tank it has the potential of re-depositing on the parts. Etch could be measured by TDS again or by the concentration of aluminum in the bath. Good Luck...


Craig Burkart
- Naperville, Illinois
Automatic process control: what is possible?
Q. Hi,
We have a rather new plating shop with baths of about 200 liters each to deposit (copper, nickel, silver, gold) on decorative zinc pieces.
We would like to make the process more stable and so have better end products. We do daily analysis in laboratory, but is there more to make the baths steadier, closer to their optimum? What kind of apparatus exists to measure or even correct parameters online?
Thanks,
- Querétaro, Mexico
2005
A. There are all sorts of things that can be done to reduce chemical parameter variation in plating line baths, but these have to be matched to individual situations. Without more information, about the only thing that can be suggested is the addition of plating additives based on amp-hour consumption and a long conversation with a consultant or your suppliers.
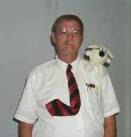
James Totter, CEF
- Tallahassee, Florida
Q. I also read about the automatic dosing equipment for brighteners from our provider.
We have temperature controlled heaters.
I guess it is impossible to check for concentrations on line (CuCN, NiSO4, boric acid, KCN or AgCN for example), as I see how complex the laboratory work is sometimes?
- Querétaro, Mexico
A. I wouldn't say its impossible to check the basics automatically in your line, but I would say its uncommon at least where I come from.
I remember receiving some junk mail advertising from some company in the UK once that had a process control unit that claimed to measure many of the basic components in plating solutions via voltammetry and this could be connected to auto dosing units that would correct and maintain the solutions. I don't recall what the name of the manufacturer was. Searching on google for "online analysis of plating solutions" gave me a link to this website:
http://www.manufacturingtalk.com/news/moh/moh100.html ⇩
This site talks about the technique a bit.
However I think you should just go with a good plating supplier that is happy to analyse your solutions for free.
It will be cheaper and you will have someone to point the finger at when something goes wrong :)
- Melbourne, Vic, Australia
Ed. update: The above link is broken. Thankfully, the Internet Archive preserved a copy here
Please consider a donation to The Internet Archive. Don't follow abandoned links, old URLs are sought out by hackers!
A. By having both yourself and your suppliers analyze your plating bath at regular, scheduled intervals; keeping track of work load during those intervals (amp hours or mil/sq ft. processed) a correlation and averages can be drawn. These can be used to schedule regular standard additions.
I have also seen automated equipment to control the solutions in all parameters but they are generally cost prohibitive. I would suggest the use of amp hour feeds for brightener additives.
process supplier - Great Neck, New York
A. Decorative applications:
Your biggest issue will be color variations from batch to batch, piece to piece. You need some one that has a knack for color judgement and can make the necessary adjustment on line.
I tried colorimetric measurements, it worked with painted surfaces but not with the electroplated surface.
Good luck,
Hamilton
- Mays Landing, New Jersey, USA
Q. We are working with our plater to update their antique handwritten process/job control sheets with an electronic version that is easily understood by the operators and easy to extract data from by our office person. This will help in generating SPC charts. Can anyone help?
Joe LindquistGold plating customer - Sylmar, California, USA
July 1, 2009
Electrochemical Metallizing by Marv Rubinstein
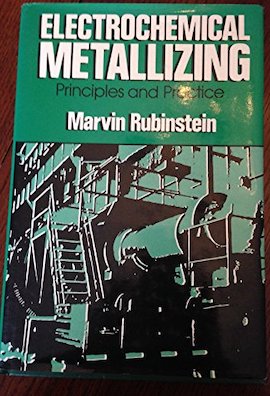
on AbeBooks
or eBay or
Amazon
(affil links)
A. Hi, Joe. I don't have a template for you, although Marv Rubinstein's "Electrochemical Metallizing" ⇨
has some old but good ideas.
But what I saw repeatedly in my consulting career was process/job control sheets that don't address the actual issues that the operators face every day: plating barrels not rotating due to stripped gears, current contact saddles not being clean, excess grease in the cleaner tanks, solution levels too low in some tanks, rectifiers with bad diodes, shortage of anode material, poor methods for getting the boric acid into the nickel tank, etc..
I would suggest that the lead plater, not just shop management, be in the meetings with you because you need instructions that are actually useful in instructing the operators what to do.
And the SPC analyst should be required to spend an hour every day out watching the plating operation, where s/he will see that the problems I just mentioned are often what is causing those blips s/he has been trying to account for chemically for two weeks :-)
General George Patton could have been speaking of some SPC efforts when he declared that "No good decision was ever made in a swivel chair."
Best of luck!
Regards,
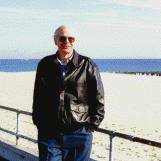
Ted Mooney, P.E.
Striving to live Aloha
finishing.com - Pine Beach, New Jersey
A. It's a hell of work but absolutely worth it. Best is to create a project team together which contains supervisors, operators, line (department) manager, Plant manager and lab chemists/Quality Assurance. With a together's brainstorm you will soon have an overview of data's you will need for a proper process control.
- Process descriptions
- Work and Hazardous Advices
- Maintaining advices
- Chemical Addition advices
- Scheduled maintenance (Electrical, Mechanical and Chemical)
- Checklists of process parameters
- Development of calculation programs (easy in excel) which allows to analyse the operational costs and allows to open up hidden "cost-creators".
Like I said, bunch of work, but absolutely worth it.
Good Luck and Best regards,
- Mexico City, Mexico
NDA = non disclosure agreement
Q. Sorry for the delay in following up on this question. We are beginning the effort of creating a detailed jobsheet with the help of the plater's team and an outside plating consultant. The main issue is selling the plating shop on the idea that this will benefit us AND HIM, especially on repeat orders. They have been very reluctant to share their step by step processes, equipment settings and times, etc. We have an NDA in place, but they have been digging their heels in about sharing details (tribal knowledge). Any additional words of encouragement?
Joe Lindquist [returning]- Sylmar, California, USA
May 12, 2010
![]() |
A. If you are paying a fair price for the electroplating, I (personally) would remind the plater what a NDA means and that if they chose not to work with you, you may start looking for a plater that will work with you.
Acronyms:
EN on Ti: electroless nickel plating on titanium That said, I am aware of at least one MAJOR US firm that browbeat the plater into disclosing a very proprietary process of EN on Ti way back in the earliest stages of this work. A senior employee took the information to another plating shop that he was part owner of and underbid the original plating shop. - Navarre, Florida A. Dear Joe, - Salem, Tamil nadu, India A. Before you spend too much energy inventing a new system, take a look at.. ![]() Geoff Smith Hampshire, England Ed. note --
A. Dear Joe,
Acronyms:
8d = 8 disciplines FMEA = failure mode and effects analysis) The positive side is that it gives any company a better insight in what the real influences in the process are (and not only by assumption). I cannot understand that, while having an NDA, a company tries to hide something, unless they know themselves that they do a "lousy" job. Finally as a customer, you have no choice but to work with the professional suppliers and all this systematics helps to improve a supplier and make them able to continuously deliver a constant quality. With a PPA you can think about the occurrence of possible disasters and how to prevent them, with the 8D and FMEA you can prevent the re-occurrence of disasters, with SPC you can connect critical process data to product quality, with a control plan you assure the equal way for everyone to check the process, with SOP's people know how a certain job needs to be done. With DOE you can determine the important influence factors in your process and after this, only some "black magic" remains, due to parameters you're still not aware of. I can assure you that the number of these parameters slowly is greatly reduced. Ted is also right, the basics are important and have to be included too. Many approaches die (and cause only lots of frustration) because people start at the top of the pyramid, instead of starting with a good simple fundamental and continue the road from there. In my opinion, a supplier should be glad if a customer is willing to help in this process, it's in the interest of both. Reasons why it could go wrong is that either your supplier is incapable (from knowledge point of view or from staffing point of view) or that you insist on doing a lot of additional work in his/her opinion, without willing to pay for this. This part of the discussion is always difficult, as in general the supplier will benefit from the systematic approach, but if you are one of the first customers who comes with a lot of additional requests which give a lot of additional work to your supplier, for sure they will not be happy. Especially not if your turn-over is relatively low for yr supplier. ![]() Harry van der Zanden consultant - Tilburg, Netherlands |
FMEA analysis for Nickel Chrome plating
Q. Hi all,
I am a student. I am doing a project in Nickel Plating. I need to prepare FMEA report for Nickel Chrome Plating. Please anyone guide me.
- India
May 21, 2018
A. Hi Sathya. We appended your question to a thread which you will hopefully find interesting. Obviously you need a clear understanding of what an FMEA Report is, and specifically what it means to you with respect to nickel-chrome plating, i.e., does a failure mean an operator injured, or plating solution leaked onto the floor, or a nickel-chrome widget being returned under warranty, or the motorcycle it's mounted on crashing, or what. Generally, a sampling of the plated components are subjected to various tests & inspections to check adhesion, corrosion resistance, aesthetic defects, etc. -- and that may be what you're concentrating on in this case.
Regards,
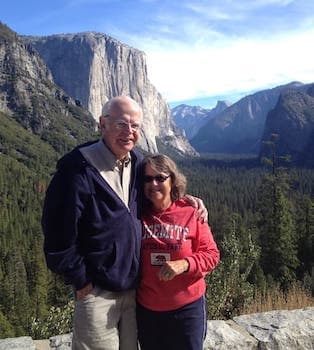
Ted Mooney, P.E. RET
Striving to live Aloha
finishing.com - Pine Beach, New Jersey
Readers may also be interested in these related threads:
• Topic #611/39 "Manual anodizing versus automation"
• Topic #10/19 "Process Control for Zincate Solutions"
Q, A, or Comment on THIS thread -or- Start a NEW Thread