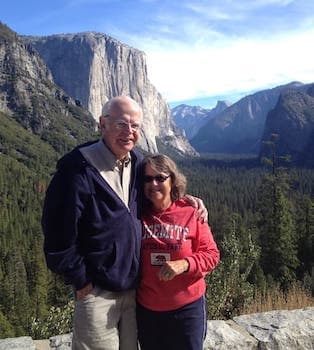
Curated with aloha by
Ted Mooney, P.E. RET
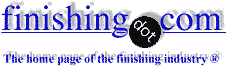
The authoritative public forum
for Metal Finishing 1989-2025
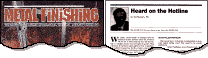
-----
Sand blasted surface won't take hard chrome plating
I got a problem during hard chrome plating on sand blast surface.
My product is a roller with OD 1200 x chrome length of 1500 mm. Sand blast surface roughness is 3.2 Ra
During hard chrome plating on surface without sand blasting, I'm using 8000 ampere and I able to hard chrome on the surface.
But after I sand blast to 3.2 Ra on the roll surface, I'm using a similar parameter I unable to hard chrome on it.
Please advise me, if got any method to solve the problem.
Hard Chrome plater - Selangor, Malaysia
June 24, 2009
June 30, 2009
You will need to increase the C.D.
Maintain the temperature, anode , cd ratio
After sandblasting, the surface becomes rough
so you need to give a strike for the ions to penetrate the crevices
if you have limitation on current try doing half at one time.
Regards
Prashant.Soman
- Ambernath , India
July 17, 2009
I try one sample recently again.
OD 700 x 1500 length. = 330 dm2
My rectifier capacity is 10,000 A
This is using sand as a medium to do sand blasting
Surface roughness 3.0 Ra
1st try,
using 7000 A to chrome this roll
Results..only both side 20 mm area have chrome
2nd try
Using 3200 A to chrome this half of this roll
Results still same
Anyone got experience on this?
Hard Chrome plater - Selangor, Malaysia
I will guess that you are using lead anodes. The next guess is that they have more yellow than brown/black which means that they are passivated. Two options-clean them to a new lead condition and then prep them with a smaller dummy part in the tank at a high amperage. This will form the dark coat that is required. Second is buy or cast new anodes. You may want to investigate the positives and the negatives of using a closer anode spacing. It has both.
James Watts- Navarre, Florida
July 22, 2009
Q, A, or Comment on THIS thread -or- Start a NEW Thread