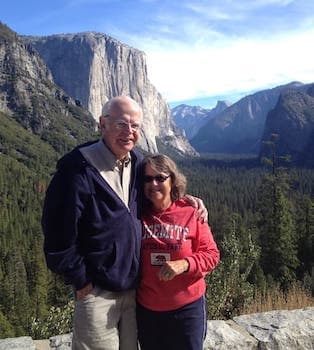
Curated with aloha by
Ted Mooney, P.E. RET
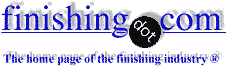
The authoritative public forum
for Metal Finishing 1989-2025
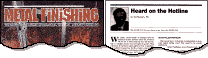
-----
Arc-wire/flamespraying aluminium bronze on fiberglass
A customer has requested that we attempt several tests to determine if a component they have that is made of fiberglass can be coated with aluminum bronze using TAFA's 8830 arc wire system. Naturally, heat is a determining factor. However, on initial testing, the component was kept cool ( under 135 degrees F ) and no visible warpage of the test panel was observed. The test panels are approximately .250 mil. in thickness and 6" in width X 4" in length. Prepping of the initial test panel was done by using 24 size aluminum oxide grit blast@ 20 psi. The coating failed and began to flake off at .024 mil thickness. The required coating thickness is to be .030. Am I wasting my customers time, or can this be achieved using this method of metallization? Would application of an epoxy-type resin to the component prior to arc-wire spraying of surface be a possible fix?
Any insight you can give me on this problem would be greatly appreciated.
Thermal spraying and machining - Norfolk, Virginia, USA
June 20, 2009
June 24, 2009
Talk to some more of the vendors. 20 years ago, I saw business cards that Metco had flame sprayed with something and then printed.
You are working with two competing factors as flame (arc) spray likes to have the parent metal at an elevated temperature. Among other things, it allows the spray material to have a coefficient of linear expansion much closer to the amount of shrinkage that the part has.
Opposing this is the need for fiberglass to have a very low temp applied to it. Also, its coefficient is about ten times that of the sprayed metal.(per degree)
A wild guess, really wild, you may have to go to a very low temp bond coat, possibly something like tin or solder or similar low temp metal.
- Navarre, Florida
Q, A, or Comment on THIS thread -or- Start a NEW Thread