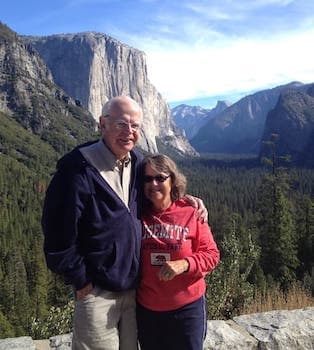
Curated with aloha by
Ted Mooney, P.E. RET
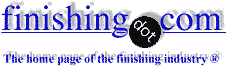
The authoritative public forum
for Metal Finishing 1989-2025
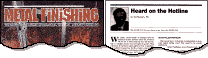
-----
Thermal & mechanical properties of anodized aluminum
Q. Does anyone have, or know where to find, information on the "thermal conductivity of aluminum oxide (anodize) for different thickness" and on different alloys? Any help would be much appreciated.
David A. Kraft- Long Island City, New York
1997
A. David,
A good question. Could not find anything in plating books, but an old Langes Lange's Handbook of Chemistry [adv: on Amazon, AbeBooks, or eBay affil links] gives aluminum oxide powder at 46.8C as gamma(?) 1.62 x10 to the 3 power g.-cal/(sec)(sq cm)(deg C/cm)
Fused aluminum oxide at 650-1350 °C is 8.0
This is the quantity of heat in gram calories transmitted /second thru a plate one cm thick and one sq cm in area with a temp difference between the sides of one deg C.
As you know, the density of anodize depends on the voltage and temperature. As well as it cracks at over 100 °C so that would throw off any high temp conductivity measurements.
James Watts- Navarre, Florida
1997
by William Safranek
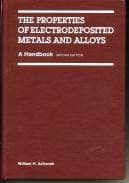
on eBay or
AbeBooks
or Amazon
(affil links)
A. Hi Dave. A common source for properties of electrodeposited coatings is Safranek's book.
It does not seem to contain that info for different thicknesses and alloys but it does have a list of good reference sources for further data.
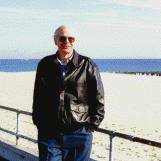
Ted Mooney, P.E.
Striving to live Aloha
finishing.com - Pine Beach, New Jersey
Multiple threads merged: please forgive chronology errors and repetition 🙂
Dielectric constant & thermal conductivity of anodized coatings
Q. Does anyone know what are the electrical permittivity and thermal conductivity factor for anodized coatings?
Thanks
Jerome Jacksonresearch - Mountain View, California
1998
A. Jerome,
Both electric permittivity and thermal conductivity vary with anodizing process, coating thickness, sealing process, environmental temperature. It was reported that the electric permittivity (dielectric constant) of hard anodic coatings is in the range of 7 to 10, and the thermal conductivity of the anodic coatings is about 21-63 W/m per degree.
Ling
Ling Hao- Grand Rapids, Michigan
1998
Q. Thanks for your response Mr. Hao.
This response supports some assumptions I made regarding the composition of the oxide layer, which I assumed was just Al203. I was concerned that, because of the porosity of the aluminum oxide layer, that the bulk electrical properties of an anodized aluminum surface might be different from the those of the pure oxide material. Do you have any insight into whether this oxide layer's electrical properties would still be equivalent to the pure oxide if the anodized aluminum surface was immersed in a conductive media? Also, how I might model the capacitance of an anodized aluminum surface coated with a dielectric like PTFE (Teflon)? The simple model would be to consider the anodized and PTFE layers to be series capacitors, but I wonder if the porosity, and thus, non-homogeneous composition of the anodized aluminum surface would have to be considered?
Thanks for your comments
Jerome
Jerome Jackson [returning]research - Mountain View, California
1998
A. Jerome,
The data ranges I gave above refer to the porous anodic coatings with and without the boiling DI water sealing. Salt solution sealing could significantly affect the dielectric constant but not the thermal conductivity. Boiling water sealed anodic coatings can be regarded as good insulators. The dielectric characteristic of the porous anodic coatings without boiling DI water sealing would definitely be altered by conductive media which can penetrate the micro pores.
The effect of PTFE top film on the total capacitance depends on the process of applying PTFE to anodic coatings. You need to take a few points into consideration. Sealing will certainly reduce the adhesion of PTFE onto anodic coatings. Without sealing, it is generally believed that PTFE only stays on the anodic coating surface without penetrating the micro pores because the sizes of PTFE resin particles are much larger than those of coating pores. In this case, the model can be approximated to a series structure. However, if the PTFE film is formed on anodic coatings using a homogeneous PTFE solution instead of a suspension PTFE solution, I tend to consider the possibility for PTFE molecules partially insert into the micro pores since PTFE molecules are the chain structure, which diameter is much smaller than the pore sizes. Then, non-homogeneous structure sounds more reasonable to me. In either of cases, you'd better design some experiments to determine it quantitatively. In addition, high temperature for curing PTFE layer could change the properties of anodic coatings to some extent.
Good luck.
Ling
Ling Hao- Grand Rapids, Michigan
1998
A. On the subject of dielectric properties of anodic coatings: A while back I had some specular anodic coated Aluminum spectro-photometered for a National Standards Laboratory reflectivity application. The exact material was a European commercial spinning grade Aluminum with a super-pure side rolled onto one surface for lighting reflector use. The material was then coated using a proprietary European Brit-Al anodic coating with chemical polishing stages. The resulting coating was highly specular, highly reflective and obviously very thick.
Of interest to the original poster is that the spectral response of the coating - as determined by NIST - was pretty much an evenly spaced saw filter from the UV through visible to the IR end of the spectrum. This was not what I expected at all - being evenly spaced band cut and band pass steps across the whole spectrum. Continuous responses being more typical, with varying levels of IR / UR transmission resulting from various coating processes.
The various deposition steps in the tank seemed to have created a multi-layer thin film optical filter. This would be of interest to the original writer - thin films interspaced with dielectric media being key to capacitance properties. The explanation is my best guess - the spectral response being sufficiently complicated I have no other way to explain it. Presumably time in the tank and content of the resulting layer would not only influence spectral response, but also the capacitance of the applied coating. Of use not only to optical engineers, but also to thermal and electronic disciplines.
- Brooklyn, New York
December 31, 2008
Multiple threads merged: please forgive chronology errors and repetition 🙂
Q. I am looking for the thermal and mechanical properties of the hard anodize film characteristics, i.e. thermal coefficient of expansion, heat conductivity, specific heat, density, Poisson's ratio, Young's/elastic modulus, etc.
I need to analyze the possible behavior of a one-sided hard-anodized 6061 thin aluminum disc as a bi-metal under heating conditions.
product designer - HOD HASHARON, Israel
June 5, 2009
Treatment &
Finishing of
Aluminium and
Its Alloys"
by Wernick, Pinner
& Sheasby
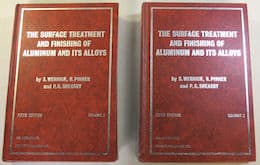
(note: this book is two volumes)
on eBay or
AbeBooks
or Amazon
(affil links)
A. Sheasby and Pinner.
say that the coefficient of expansion of the anodic film is 0.2 that of the underlying aluminum metal. They also say that cracking starts somewhere near 80 °C to 100 °C.
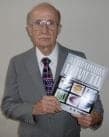
Robert H Probert
Robert H Probert Technical Services

Garner, North Carolina
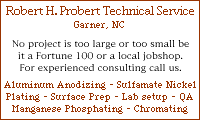
Q. Is there any available reference on all other characteristics of the hard anodize film ?
Sason Benado [returning]- Hod-Hasharon, Israel
June 21, 2009
June 22, 2009
A. Hello, Sason. Some of the remaining properties are also covered in "The Surface Treatment of Aluminum and its Alloys" (same book as referenced by Mr. Probert).
The coefficient of linear expansion and thermal conductivity are in the 'Hard Anodizing' chapter, listed under "Thermal Properties". There is some information about Young's modulus in the 'Anodic Coatings: Properties and Tests' chapter, under "Elasticity and Fracture of films". The same chapter lists the apparent density, and there is a good deal of discussion of real vs. apparent density scattered throughout the book. I don't think you'll find Poisson's ratio, and I'm not sure it's really a measurable or calculable property for hard anodized films. Good luck.
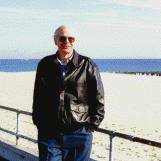
Ted Mooney, P.E.
Striving to live Aloha
finishing.com - Pine Beach, New Jersey
Q. I am Folabi an undergraduate student and I am looking for information similar to that of Sason, but I am not dealing with hard anodised aluminum rather I am dealing with anodised aluminum. I am looking for information on the thermal and mechanical properties of anodised aluminum. Especially aluminum anodised with sulfuric acid as electrolyte. I will also like to know the conditions (voltage, current density, concentration of electrolyte, and temperature) for producing top quality films using sulfuric acid. I also want to know what advantages there are, if there is any, in using aluminum as the cathode instead of lead.
Thank you.
Folabi
student - Epe, Lagos, Nigeria
April 8, 2011
A. Hi, Folabi.
The previously referenced book is the closest thing to the "encyclopedia" for anodizing of aluminum. Please look for it in a Lagos public or university library. We are reluctant to quote values out of context because, for one thing, anodized films are not metals, they are thin surface coatings attached to aluminum, and it is very easy to take quoted values and misuse them; better to read them in context and understand what the numbers actually mean and imply for a design. For example, fatigue can be a very serious issue in anodized parts, and to take the mechanical property numbers from a chart and use them without being exposed to those introductory discussions of fatigue can be a problem.
Probert's "Aluminum How To" is not encyclopedic, but is a great practical reference for producing quality anodized films.
The biggest advantage of aluminum cathodes is probably energy savings. If you search the site for "aluminum cathodes" you will find several in-depth discussions of that topic. Best of luck!
Regards,
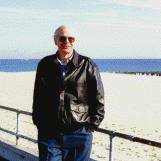
Ted Mooney, P.E.
Striving to live Aloha
finishing.com - Pine Beach, New Jersey
April 11, 2011
April 29, 2011
A. I got a hold of the books so I'll post the values here so that people that don't have the access can readily get the values:
Surface Treatment of Aluminum, Wernick and Pinner, 4th Edition, P.608, Ch. 9. Hard Anodizing:
Thermal properties
The temperature of fusion of anhydrous alumina is 2100. The hydrated alumina begins to lose its water of crystallisation at about 500. The specific heat of the coating is:
0.200 cal/g from 20 to 100
0.233 cal/g from 100 to 500
The coefficient of linear expansion is approximately five times less than that of the basis metal:
anodic coating, alpha = 5 x 10^-6
aluminum, alpha = 23 x 10^-6
The thermal conductivity of the anodic coating is between one tenth and one thirtieth of that of aluminum:
alumina 0.05-0.015 cal/cm^2/sec/cm/C = 21 - 6.3 W/m
aluminum 0.5 cal/cm^2/sec/cm/C = 209 W/m
The emissivity of aluminium increases rapidly as the thickness of the layer is built up, increasing to 80% for a 10 µm coating. A thick hard anodic coating is therefore well on the way to being a 'black-body' for heat dissipation, and there is very little advantage in dyeing it black as is sometimes done.
- Madison, Wisconsin, USA
Q. I understand anodizing per MIL-A-8625 is normally considered a non-electrically conductive finish, but isn't there a certain point / voltage in which static electricity will begin to flow through an anodize finish? If so what would be the minimum and maximum expected voltage this would occur at? What are the units that the insulative (or conductive) properties are specified for comparing different anodized finishes.
Kent Campbell- Everett, Washington
November 16, 2012
Q, A, or Comment on THIS thread -or- Start a NEW Thread