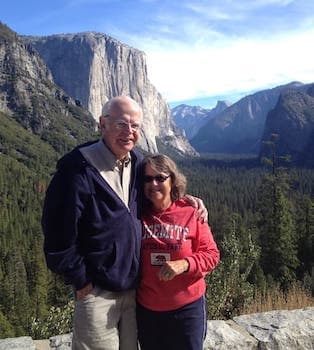
Sound technical content, curated with aloha by
Ted Mooney, P.E. RET
Pine Beach, NJ
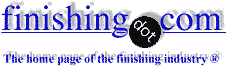
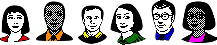
The authoritative public forum
for Metal Finishing since 1989
-----
Tech help for wheelchair riders in developing countries (finishing of steel pushrims)
May 30, 2009
I need ideas on a difficult steel finishing problem affecting wheelchair riders in developing countries. I've listed the design requirements and past ideas below, with the questions at the bottom. Thanks in advance.
REQUIREMENTS:
A wheelchair pushrim (the large ring attached to the rear wheel for propulsion by the wheelchair rider's hands, often made of 19 mm mild steel tubing with 1 mm wall thickness) has the following requirements for finishing:
1) corrosion resistance
2) impact and abrasion resistance (pushrims are the widest point on wheelchairs and frequently bang and scrape against doorways etc)
3) "coolness" during braking (when a rider coasts down a hill, the rider must be able to let the rim slip rapidly through the fingers, then grip strongly at the end of the ramp or hill to slow the wheelchair. If the rider cannot "brake" both strongly and evenly, the wheelchair may get out of control and the rider may crash.
4) safety against cuts
5) safety against toxicity (skin contact)
6) residue on hands (some finishes i.e., hot-dip galvanization leave hands black)
7) appearance (over and over we have learned that when people are proud of the appearance of their wheelchair, they will have more confidence to use the wheelchair in public, and they will maintain the wheelchair better).
8) cost (wheelchairs in developing countries are often purchased by donors or governments who want lowest cost)
9) worker / environmental health
(note: I have left out "gripping friction", which is a requirement for riders with low hand strength. however this is usually accomplished by adding an additional layer of rubber or similar material, rather than a finishing)
PAST IDEAS AND PAST PROBLEMS
1) Nickel-Chrome: good abrasion resistance and "coolness" but when it "flakes" / delaminates, the resulting razor-sharp flakes cause serious injury to fingers. these (often deep) cuts are extremely inconvenient for wheelchair riders who must use their hands to propel, and present an infection risk for poor people without good access to nutrition and medicine who may be living in unhygenic environments. Toxicity concern for workers and people who live near factories (serious concern in under-regulated countries).
2) Powdercoating: looks great when new, and never cuts fingers even when worn. However can cause severe friction burns (even deep burns with blistering) when a rider descends a steep hill too quickly. Riders without the pain tolerance to grip the rims anyway may lose control and crash. Abrasion resistance is not very good, usually there is visible steel (and often rust) after a few months of use. Low-cost and non-toxic.
3) Stainless steel pushrim (alternative to plating): works well, has excellent abrasion resistance, but is expensive. use of thin-wall stainless to save cost results in brittle failure of welds.
4) Plastic pushrim (alternative to plating): similar problems to powdercoating plus poor abrasion resistance and fragility.
5) Anodized aluminum pushrims (alternative to plating): This is the standard in wealthy countries where people can afford to replace damaged pushrims
QUESTIONS:
--How can we assure nickel-chrome will not flake and cut fingers, especially from low-cost producers? what method (steel/nickel/chrome, steel/copper/nickel/chrome, steel/nickel layer 1/nickel layer 2/chrome) provides best adhesion? what are "warning signs" of improper steel prep to look for during factory visits? In general is it reasonable to expect well-applied nickel chrome to take a beating without flaking--ie is the flaking we've seen in the field because of poor manufacturing QC, or is chrome a poor design choice for this application?
--what other technologies (chrome substitutes i.e., cobalt alloys, nickel-only plating, passivated zinc, black oxide, ?) might meet the requirements above?
Many, many thanks on behalf of all the wheelchair riders in the world with burned or cut fingers.
product designer - Cape Town, South Africa
As a powder supplier to wheel chair mfgr. in the UK I understand that they do not seem to have the problems you mention. They apply tinted clear powder lacquers (red, blue, green etc) over a chrome finished substrate. This finish is not only appealing to the purchaser but... as you state, hard wearing, non toxic and maybe because the powder contains no pigments or extenders, does not have the abrasive properties you describe.
Terry HicklingBirmingham, United Kingdom
June 3, 2009
Q, A, or Comment on THIS thread -or- Start a NEW Thread