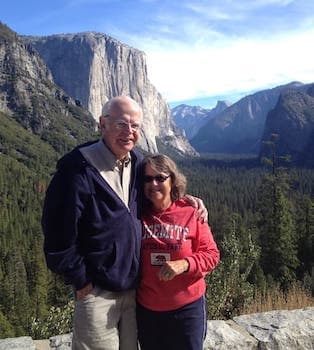
Curated with aloha by
Ted Mooney, P.E. RET
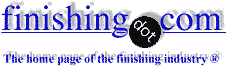
The authoritative public forum
for Metal Finishing 1989-2025
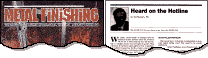
-----
Gold plated aluminum bubbles, blisters, peels
Q. Problem: Copper strike not adhering to 1100 series Aluminum wire. The larger the diameter wire the better we can plate. We are using a hot caustic etch to clean the wire. The final plate is a gold plate. Any suggestions would help.
Christel Bitz- Mount Vernon, New York
2002
A. Hi Christel. It sounds like there are intermediate steps you have skipped, such as zincating, copper and nickel plating or electroless nickel plating, etc. It should be determinable what layer is separating from what?
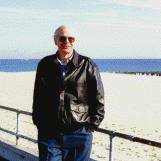
Ted Mooney, P.E.
Striving to live Aloha
finishing.com - Pine Beach, New Jersey
2002
Q. We are using an alkaline etch hot. Then rinsing and putting a copper cyanide plate on immediately since it is reel to reel so we skipped the zincating step. It was determined that the copper is separating from the aluminum.
Christel Bitz [returning]- Mount Vernon, New York
2002
A. Is this an established process that has gone well for years and has suddenly started to get troublesome, or is it a new installation which has not demonstrated robustness yet?
I ask because I can't state that it's impossible to reliably plate cyanide copper directly onto etched aluminum, but even in reel-to-reel wire plating installations, I have only seen cyanide copper plating onto aluminum done with a zincate layer in between.
Notwithstanding that, I have seen electroless nickel deposited directly onto aluminum with neither the zincate nor the cyanide copper and it worked (although I was not in a position to know what the adhesion value was in that case) and I have heard that aluminum can be plated without zincate with the brush plating method.
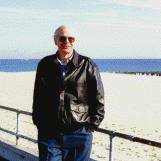
Ted Mooney, P.E.
Striving to live Aloha
finishing.com - Pine Beach, New Jersey
2002
The process is not a new one but has never really been perfected, there have always been issues of the copper layer adhering to the aluminum. The customer has issues with nickel and we are not equipped to do brush plating. Thanks for the advice about the zincating we will try this next.
- Mount Vernon, New York
2002
Multiple threads merged: please forgive chronology errors and repetition 🙂
Gold plated aluminum blisters after high temperature bake
by Reid & Goldie
-- hard to find & expensive; if you see a copy cheap, act fast!
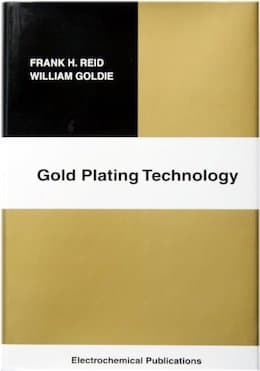
on eBay or
AbeBooks
or Amazon
(affil links)
Q. Greetings Everyone,
Our plating company is having adhesion problems with certain 6061 aluminum housings. The spec calls for .0001"-.0003" mid-phos EN followed by a final plate of .00005" min. pure gold. The problem is blisters after a 25 minute bake at 610 F. Our typical process is:
Non-Etch soak clean: 5 minutes
Etch Clean: 1 minute
Nitric/Fluoride Acid: 1 minute
Cyanide Zincate: 2 minutes
Nitric/Fluoride Strip: 1 minute
2nd Zincate: 1 minute
EN Plate: we apply approx. .0002"
Gold Strike
All steps are followed by triple rinsing and the chemicals we use are proprietary (i.e., not home brews).
After the gold strike we inspect the parts and bake them at 375 ° F for 1.5 hours to check adhesion and help relieve the EN.
All parts pass the first bake and look excellent. No defects are found when examined under magnification. We then soak clean, re-activate in an acid salt, gold strike again, and then plate the final gold layer. The parts are inspected again then baked at 610 °F for 25 minutes. This is when blisters finally appear. They are relatively small and go down to aluminum when peeled back and examined at 10x magnification.
This is a little confusing to us since we plate a lot of aluminum parts and rarely have problems, albeit most are subject to a lesser heat treat. We monitor all our baths and rinses to ensure they are in-line and have noticed no irregularities. The parts are plated in an EN bath with 3 or less turnovers to help ensure maximum adhesion.
We question that if the parts were improperly pre-treated shouldn't blisters manifest after the first bake? Are we inducing additional stresses in the deposit when we put the final plate on? Is the combination bake too much before some type of diffusion occurs?
Any and all insight would be greatly appreciated. Please let me know if you need any more information.
Plating shop employee - Erie, Pennsylvania, USA
A. Joe, my comments are an educated guess based on your description.
Since you do not have complete coverage (perfect 100% coverage)on either the EN or the gold strike(they are too thin for that), I think that putting them back in the caustic and the acid is finding pores or micro voids in the plate that one or both chemicals is getting under the plate. Your gold is plating over it and the oven is expanding the liquid, turning it into gas at 760 times the volume. the final gold is also pulling some of the weakened strike off, giving you bare aluminum.
Unless you have a good reason, I would only go into the gold 1 time. Your first bake is not really doing that much for you and gold does not oxidize if it is kept clean, you might be able to do the inspection and go back into the gold for a second time. This is not my favorite way of doing it.
- Navarre, Florida
May 19, 2009
A. You are right to consider diffusion, BUT ALSO, think about coefficient of thermal expansion. I do not have a number for EN, but it is documented that anodizing expands only 1/5 of the underlying aluminum metal beginning at 100 °C (says Sheasby and Pinner).
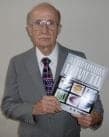
Robert H Probert
Robert H Probert Technical Services

Garner, North Carolina
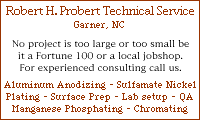
May 19, 2009
A. Dear Joe,
Your pretreatment sounds OK.
I would recommend to reduce the dipping time of the second Zincate to no more than 20 sec.
The root of your problems may be stress on the deposit.
This can be resolved by using a Alkaline Electroless Strike and/or limiting the MTO of your EN Bath.
Bnei Berak, Israel
May 29, 2009
June 1, 2009
Hello All,
Thanks for the helpful information you provided. It seems that we have solved the problem by switching to a different EN chemistry.
I'm not exactly sure why the different chemistry is working, but my hunch is it has to do with the amount of stress involved with the two baths. I'm currently working with our supplier and will let you know if we discover the true trigger mechanism.
- Erie, Pennsylvania, USA
A. The problems with the small blisters were hydrogen or chemical trapped under deposit metal,when you baked and released a gas it made its small bubbles on the surface.When I worked with Alumina oxide substrate,we cleaned with alkaline and baked to make sure the substrates clean,before we lay down palladium and copper.After we plated and we can see the small blisters in different area and we changed the way how to clean the Alumina substrates and we never see the blisters again.Maybe during transfer parts and the ages of the electroless nickel bath,because of the chemicals deplete you don't know what is the ingredient missing.The electroless nickel is very sensitive.Good Luck,
Duang Bouphasavanh- Myrtle Beach, South Carolina, U.S.A.
June 7, 2009
Blister on aluminum with Electroless Ni plated with gold
August 17, 2009Q. To whom it may concern,
I am a technician/operator for a small medical company in Boulder CO. where we manufacture a hearing aid.
One of the parts we use in the construction of this hearing aid is an aluminum mandrel w/ convolutions, that is plated with Electroless Nickel, and then is electroplated in a gold thallium bath solution. There are four different processes, and the first process is the electroless Ni plating and gold plating. The aluminum mandrel is cleaned with acetone
⇦ this on
eBay
or
Amazon
[affil links] Warning! highly Flammable!
for approx. 5 minutes, then cleaned/etched in NaOH for 20 seconds, rinse in D.I. water, Desmut for 10 seconds, rinsed again in D.I. water, then put in a Zincate solution for 1 minute, rinsed again for 10 seconds, and then plated in Electroless Ni that is heated to 190 °C for 2 minutes. The parts are triple rinsed and plated for a total of 7 minutes in a gold thallium solution. Sometime the parts usually air dry for 24 hours after the initial gold plating. But since we are gearing up productions of these parts, I have been testing and drying the parts within a hour after air drying. I do a testing of these mandrels in Sodium Hydroxide for 5 minutes, triple rinse in DI water, then oven dried. Lately I have been having a problem with blisters on the surface of the mandrel after drying the parts in an oven that is 125 °C ^125 °F.
Before I dry them I do a visual inspection and I find no blisters, the surfaces of the mandrel are smooth and blemish free. After testing the parts in a Sodium Hydroxide solution (.5N), drying the parts in the oven for 20-30 minutes and the when doing a visual inspection of the surface of the mandrels, I have blisters.
Can this blister be forming from the drying of the part and the electroless Ni releasing hydrogen and the hydrogen is trapped under the thin layer of gold? The mandrel's convolutions have most of the blister.
I am at odds of what could be going on with this process, and I would appreciate any advice you could give me.
operator - Boulder, Colorado
A. Hi, Troy. There are two things that are not quite clear to me. First, you are electroplating, not electroforming? That is, although you use the term 'mandrel', the mandrel is part of the finished product? Second, you suspect that the blister problem is between the electroless nickel and the gold, rather than between the aluminum and the electroless nickel -- and you have confirmed this by breaking off a blister and seeing that gold rather than nickel is on the underside of the blister?
Baking of parts is often done as an adhesion test, not just for drying, so it is no surprise that heating the parts to 125°C accelerates the blistering. So, in a way, it really doesn't matter what the mechanism is by which the baking causes loss of adhesion: regardless of whether it's caused by hydrogen, water vapor, or differential expansion, the plating should be able to "take it".
I suspect that the adhesion of the gold plating onto the electroless nickel is not good enough for some reason revolving around the fact that electroless nickel passivates rapidly. You could try paying very close attention to absolute minimum delay time between exiting the electroless nickel tank and gold plating. If that does not solve the problem, you can try a Wood's nickel strike after electroless nickel and immediately before gold plating. Good luck.
Regards,
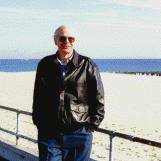
Ted Mooney, P.E.
Striving to live Aloha
finishing.com - Pine Beach, New Jersey
October 20, 2009
Corrosion blisters on nickel and gold plated 6061 aluminum housings
December 16, 2009WE CNC MACHINE 6061 ALUMINUM HOUSINGS AT OUR SHOP AND THEN SEND THEM TO A FIRST CLASS PLATING SHOP. WE HAVE BEEN DOING THIS FOR ABOUT 17 YEARS. FOR THE MOST PART WE HAVE HAD GOOD SUCCESS.
THE PROBLEM IS CONSISTENCY. A COUPLE OF TIMES A YEAR WE GET HOUSINGS BACK THAT ARE BLISTERED.LATELY IT HAS BEEN A REAL PROBLEM. THERE SEEMS TO BE CORROSION BETWEEN THE NICKEL AND THE ALUMINUM WHEN YOU SCRAPE IT UNDER 30X. SOMETIMES WE GET HEAT BLISTERS TOO. WE HAVE TRIED DIFFERENT PLATERS WITHOUT MUCH SUCCESS. COULD CHLORINE THAT THE CITY PUTS IN THE CITY TAP WATER HAVE ANY EFFECT IN THE RINSE TANKS AT THE PLATER? COULD CHLORINE BE GETTING TRAPPED UNDER THE NICKEL LAYER AND CAUSING THE CORROSION? COULD THE ZINCATE STEPS HAVE AN EFFECT IF THE ZINC LAYER IS NOT UNIFORM?
THE PARTS ARE BAKED OUT AT THE PLATER AND ARE FINE THE PROBLEM IS AFTER A COUPLE OF WEEKS THE BLISTERS APPEAR.
ANY HELP ON BLISTERING OF NICKEL/GOLD PLATED 6061-T6 ALUMINUM WOULD BE GREAT.
PS. THE PLATING SPEC:
ZINCATE PER ASTM B253 TWICE
NICKEL PLATE, ELECTROLESS [100-300 MICRO-IN] PER MIL-C-26074
[⇦ this spec on DLA], CLASS1
GOLD PLATE [50-120 MICRO-IN] PER MIL-G-45204 [link is to free spec spec at Defense Logistics Agency, dla.mil], TYPE 3,GRADE A, CLASS 1,
BAKE HOUSING @ 320 °C FOR 20 MINUTES MIN.
CNC MACHINING. - GLOUCESTER, Massachusetts USA.
Putting the pieces together on gold plating aluminum
May 15, 2017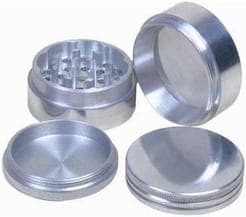
Q. I have questions about gold plating aluminum. I have used custom search and scoured the internet but I still can't find sufficient answers.
I am attempting to gold plate tobacco grinders (looks like this.
They are made of aluminum. I understand that you can either zincate the aluminum (which I read is very difficult for an amateur) and then plate it with nickel, and then gold. Or you can plate the aluminum with copper, then nickel, then gold. Now to my questions:
Which is the best method for an item such as this? There are sharp corners and it is generally an odd shape, so I don't know if one method is better than the other.
If zincating is the truly better option, can I buy the solution to zincate outright or do I need to mix it myself? I live near the LA jewelry district and searching through supply stores websites, I haven't found what I need.
If plating with copper first then nickel and then finally gold is the better option, what do I need to get the first layer of copper to adhere properly to the aluminum? Just degreasing/electrocleaning? I plan on using a bath plate system with 30 V/5 Amp adjustable rectifier. I have tried reading through some books I have seen posted here, but it just made me even more confused.
If anyone can give me definitive answers to the process and what exact solutions I need to get aluminum gold plated I would greatly appreciate it! Thank you
- California, United States
A. Hi James. I don't think copper plating directly on aluminum is accepted practice. You need to properly pretreat (non-etch clean, etch, de-smut), then zincate, then you could electroless nickel plate, then gold plate. Or zincate, cyanide copper plate (cyanide is not appropriate for hobbyists, of course), nickel plate, then gold plate. Trustable responders on this site have said you can zincate, then nickel plate without the copper, but I personally haven't seen it.
Still, when people ask for "exact solutions" to do a multi-step process which they realize is difficult, and is fraught with booby traps at every step, I personally think it's a doomed approach. I think you acquire some aluminum pretreatment experience, acquire some zincating experience, acquire some nickel plating experience, and acquire some gold plating experience ... and then get back to us with the problems you experience in each area. I'd probably start by nickel and gold plating some nice high quality brass sample panels because they are probably the easiest; then with confidence that you know how to nickel-gold plate, you can start fooling with aluminum.
For zincate and other processes, it's probably best to look up "plating supplies" or plating distributors". Good luck.
Regards,
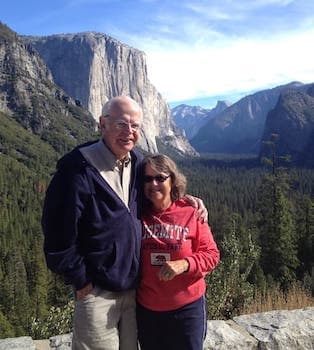
Ted Mooney, P.E. RET
Striving to live Aloha
finishing.com - Pine Beach, New Jersey
May 2017
A. Hi James. Although electroplating over aluminium can be done successfully it is known as a pretty tricky process even for an experienced processing engineer. Aluminum is not, however, difficult to anodize. Have you considered anodizing them a gold color?
If it is real gold you seek, then try making them or have them made out of a different material like brass or bronze. Then you can use that Cu strike, Ni, Au process you read about. Lastly, If changing the substrate material or anodizing is not the answer you should find a shop that specializes in plating aluminum and have your parts done by a professional. Setting up a D-I-Y Gold over aluminum plating process will be nearly impossible without a team of plating engineers, analytical equipment or lab access, and a great sum of money to cover material cost to put together and manage gold plating solutions.
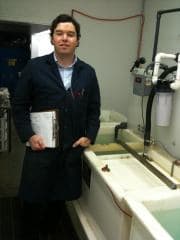
Chance Dunstan
Electroplating/Forming/Coating Manager
Placerville, California USA
August 2, 2017
Q. Hi,
I have a slight problem with electroplating Al blocks. Sometimes I see blistering after a post-plating bake at 250 °C for 4 hours. The substrate is Al and I am electroplating Ni then followed by Au. I have noticed that the blistering occurs at the corners and edges. Sometimes 8/10 blocks show blisters and other times only 1/10. The blisters only show after the bake and not before.
Has anyone experienced this before and if so, how have you solved it?
Many thanks,
Ali
- Didcot, Oxfordshire
December 7, 2020
Q, A, or Comment on THIS thread -or- Start a NEW Thread