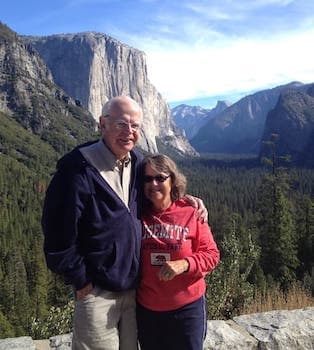
Curated with aloha by
Ted Mooney, P.E. RET
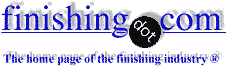
The authoritative public forum
for Metal Finishing 1989-2025
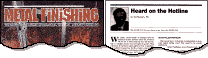
-----
Solving "Acid Weep" in galvanizing

Q. An unattractive phenomenon that sometimes occurs in galvanizing occurs after galvanizing steel fabrications where two flat surfaces are welded together but not fully welded. Acid and alkali etc seep into the crevice formed by the flat surfaces being close but not sealed by welds, and subsequently boil dry in the immersion in zinc. This leaves oxidized dry crystalline residue behind. On the first shower of rain and water entering the crevice, a solution of iron hydroxide is formed which then seeps out leaving what looks like a rusty stain. In fact the stain is on the surface of the zinc coating, and doesn't normally compromise corrosion protection, but it looks unsightly and to the uninformed, looks like the job is "going rusty"..
One solution is to fully seal such welds so that no cleaning chemicals can enter. But this solution is not in the control of the jobbing galvanizer, and so usually doesn't happen.
Has anyone else found a workable, practical solution to this problem?
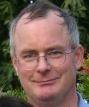
Geoff Crowley
Crithwood Ltd.
Westfield, Scotland, UK
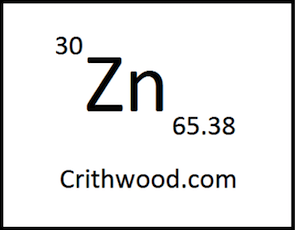
May 18, 2009
![]() |
A. Geoff, ![]() Bill Reynolds [deceased] consultant metallurgist - Ballarat, Victoria, Australia We sadly relate the news that Bill passed away on Jan. 29, 2010. A. Yes, you're right regarding the acid weeping but that occurs normally after quenching and there is no such method to control it but after 2 or 3 days when the weeping is over you can give touch up to the weeped area. SENTHIL KUMAR- Mumbai |
Thanks for replies.
One of the "joys" of jobbing galvanizing is that you don't know who the customer will be tomorrow! (In fact forward visibility of orders is about 1 day! Half our work comes in unannounced). Additionally there's lots of them (about 1500)
So getting the fabricator to "do the job right" isn't really a viable option.
I need some magic that can solve the problem at low cost!
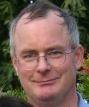
Geoff Crowley
Crithwood Ltd.
Westfield, Scotland, UK
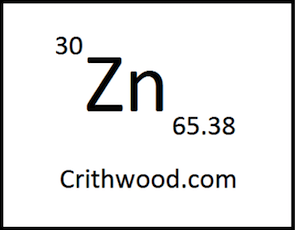
A. Geoff,
This is what I call a "pocket weld." I did a calculation for a
"closed pocket" having dimensions 3mm x 100mm x 100mm. First filled with DRY air and the result was only 15 to 20 psi. Next I calculated the same "closed pocket" filled with water and the result was around
50,000 psi. Thus for a semi closed (or slowly leaking pocket weld) the pressure is enormous. This explains the bowed out kettles that I saw many years ago in the early work. There have been several very serious injuries resulting from semi closed pocket welds in hot dip galvanizing.
Regards, Dr. Thomas H. Cook, Hot Springs, South Dakota, USA
Galvanizing Consultant - Hot Springs, South Dakota, USA
Q, A, or Comment on THIS thread -or- Start a NEW Thread