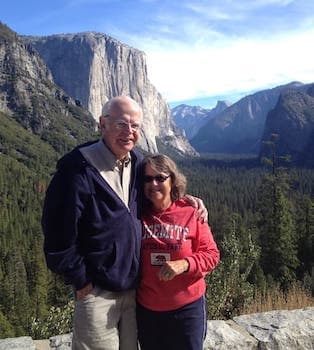
Curated with aloha by
Ted Mooney, P.E. RET
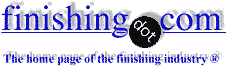
The authoritative public forum
for Metal Finishing 1989-2025
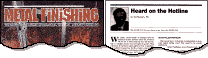
-----
Wear resistant finish for 2014 aluminum cylinder bore
Our application is a small 2014-T4 hydraulic cylinder, about 1.25" i.d., .2" wall thickness, 4" long. We are looking for a plating process for the inside bore. Hard urethane seals ride in the bore at high pressures, 4-5000 psi. The surface finish requirement is 8 Ra uin. Part were 6 Ra µinprior to anodizing.
We have tried hard anodizing/lube process and the parts came back 23 µinfinish. We put on test stand and coating wore off in 100K cycles, and did not seem much better than non coated surface.
Anodizing is degrading the surface finish, and we were unsuccessful at honing the parts after anodizing.
We are now looking at Electroless nickel for this application. Corrosion is not a concern.
Which is a better choice, EN or hard anodize? If we can't obtain the surface finish, no point in the coating. Will EN degrade the surface finish? If so how much?
Thanks
- Woodstock, NY, United States
May 15, 2009
First of two simultaneous responses -- May 18, 2009
I would look at EN. The surface will be close to what you start with. Exceptions are if the plater stays in the cleaner tank or the etch tank too long. It also needs to have a zincated surface. A zincate-strip zincate will give the best adhesion, but it will roughen the surface a bit, but not that much.
An electroless nickel strike will go a long way in getting great adhesion. I would look at a low phosphorous EN for the final coat. Done correctly, there is no honing required.
You might have to look around to find a plater with excellent experience. Some shops will have part of what I recommended and other shops will have other parts of it. A few will have all of it and be good at it.
- Navarre, Florida
Second of two simultaneous responses --
Hi Robert,
Anodizing the inner dia is a tricky affair! You may have to have a rod like cathode which should be positioned inside the surface to get a better throw. Else you can't assure uniform thickness ( may not build up at bottom ).2017 is a copper Aluminum alloy which may not support much for Hard Anodizing (You may have burning problem)
Electroless Nickel could be a good choice but ensure proper Bondage of the coating.i.e. your pre-treatment must be good. You must go for double Zincating.
You can also think of Electroless Nickel with PTFE composite coating, wherein you get a better co-efficient of friction.
Good luck!
- Chennai, India
May 19, 2009

Q, A, or Comment on THIS thread -or- Start a NEW Thread