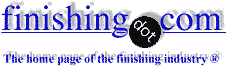
-----
Mechanical polishing or passivation of Stainless Steel - which comes first?
April 30, 2009
Hello,
I know that if you electropolish it is not necessary to passivate stainless steel.
But what if mechanical polishing is the process? Should you passivate then polish or polish then passivate.
Thank-you,
Finishing Company - Rincon, Georgia
Hi, Micheline. The mechanical polishing comes first, and then the passivation. The reason you don't need to passivate if you electropolish is because the electropolishing process (putting the component into a strong acid with an oxidizing electrical current at work) is pretty much the same thing as passivating (putting the component into an oxidizing acid) from the standpoint of de-activating the stainless steel.
Regards,
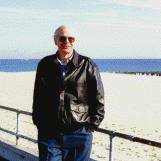
Ted Mooney, P.E.
Striving to live Aloha
finishing.com - Pine Beach, New Jersey
May 1, 2009
May 7, 2009
Ted,
If you polish first will passivation not ruin the beautiful finish?
Micheline
- Rincon, Georgia
First of three simultaneous responses --
Not if it is done correctly. There will be virtually no change.
James Watts- Navarre, Florida
May 8, 2009
Second of three simultaneous responses --
Mechanical polishing will give you the surface finish you require. This could be enhanced by electropolishing, which will also provide you with a better passivation than normally obtained with simple polishing. For instance, with stainless steel the passivation film is normally an oxide that will give a dull finish; electropolishing gives a brighter finish that is passivated by phosphate
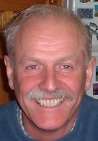
Trevor Crichton
R&D practical scientist
Chesham, Bucks, UK
May 9, 2009
Third of three simultaneous responses --
The answer to that question is no. A passivation will not change surface quality :)
Bill GraysonMetal Finishing - Santa Clara, California
May 11, 2009
May 13, 2009
Thank-you for all the responses.
I did find a couple of scrap pieces that had been polished and was able to practice on them, and of coarse I found out that you are all correct. It did not change the appearance, but now I must be very careful of scratching.
I use Stainless Steel baskets and SS wire in my tanks. can I get any suggestions that would be less abrasive.
Sincerely,
- Rincon, Georgia
You can get plastic "pails" that have lots of small holes in them. Some places have different size holes. I would prefer polyethylene to polypropylene for resistance to the nitric acid, but PP will do. They are quite stout and will last for a couple years or more in normal use. Eventually, the oxidizing acids will make the pail brittle.
Also, they cost about the same as a good 316SS basket.
- Navarre, Florida
May 14, 2009
Electropolishing and passivation are both good for corrosion resistance of stainless steel, for different reasons.
Electropolishing produces a very smooth surface, and corrosion is best able to occur on rough surfaces. Passivation produces an iron-free surface with high amounts of chromium and chrome oxide, which is resistance to chemical reaction and protects the underlying iron. A electropolished surface that is then passivated enhances the corrosion resistance even further.
Nitric passivation can change the finish if not done properly, i.e. parts are left in too long. citric acid passivation does not present that risk.
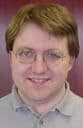
Ray Kremer
Stellar Solutions, Inc.

McHenry, Illinois
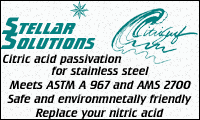
June 2, 2009
Electropolishing or Passivation/Pickling comes after mechanical polishing.
Passivation in Nitric/Hydrofluoric solutions will produce a dull grey matte surface finish if processed too long.
Pickling pastes/gels (Nitric/Hydrofluoric/Jelling agent) will produce a dull grey matte surface finish if processed to long.
Electropolishing produces a bright polished surface finish with the same benefits as ultra-passivation.
You can use different combinations of the above to meet clients requests.
electropolishing shop - North Vancouver, British Columbia, Canada
September 18, 2009
Hi, Cliff. I've never heard of passivating in nitric/hydrofluoric acid, but I've certainly heard of pickling in it. I think we're starting to conflate pickling with passivation.
Regards,
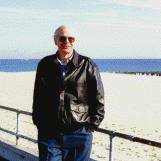
Ted Mooney, P.E.
Striving to live Aloha
finishing.com - Pine Beach, New Jersey
September 18, 2009
Hey Ted,
Yes you're right. My apologies, the Hydrofluoric in Nitric/HF solutions make it a pickling solution. The HF removes the passive layer, rust, heat scale, and just about everything else on the surface leaving a "white pickled" finish. Conditions being right in the area will lend the freshly pickled surface to auto-passivation by reacting with oxygen in the air. Again my apologies to everyone.
- north Vancouver, bc, Canada
October 8, 2009
Q. Is there a need for pickling of inner surface of a polished vessel prior to passivation?
Sethuraman- Hyderabad, A.P., INDIA
June 14, 2012
A. Hi Sethuraman.
A "polished" vessel? I'd say no "pickling" is required. But please remember that the passivation solution is not a good cleaner, so you probably need alkaline cleaning and rinsing before passivation. Good luck.
Regards,
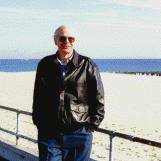
Ted Mooney, P.E.
Striving to live Aloha
finishing.com - Pine Beach, New Jersey
June 15, 2012
March 13, 2013
Surface Polishing hydraulic components after Passivation
Q. Lap Fitted / Match Fitted Assemblies following passivation of the individual components. We match fit Spool and Sleeve assemblies to clearances from 20 millionths to a couple tenths. i.e., .000020 min. to .0002 max. depending on operating specifications. The components are passivated prior to the final matching process. The final polishing process may require only a few millionths material removal or a few tenths material removal necessary to achieve the required diametrical Clearances as well as straightness and roundness tolerances. What is the impact of this post passivation processing on the passivation?
Is there an Industry Spec that allows a certain amount of Polishing after Passivation, under certain applications?
Quality Engineering - Los Angeles, California, USA
A. QQ-P-35 Rev C "Passivation Treatments". Section 6.1 and elsewhere mention how to handle parts after passivation. It seems risky to me, it's too bad you can't match them then passivate rather than adjust them after passivation. One important note, no matter what you want to wait 24 hours after the passivation before trying anything.
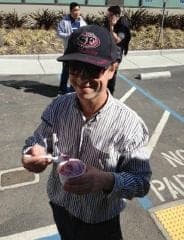
Blake Kneedler
Feather Hollow Eng. - Stockton, California
July 13, 2013
A. Hi Douglas,
We had a similar problem with a similar part type. It seems rather pointless to passivate if you are then going match grind, even if only kiss grinding. Passivation is a cleaning process that allows the growth of a natural oxide layer, this layer is extremely thin (in the order of nanometers) so any post treatment activity will remove that oxide layer.
In our case we were fortunate that the parts were running in hydraulic fluid, which is corrosion inhibited so we just dropped the passivation requirement.
Aerospace - Yeovil, Somerset, UK
July 16, 2013
Q. As in our case as well, the lap fits are used in hydraulic applications, i.e., 5606, 83282, phosphate ester, etc. The vast majority are used in hydraulic fluid, however there maybe a couple applications where a pneumatic valve is produced utilizing a match lapped slide & sleeve assembly.
The biggest problem with passivating post Lap Fitting is the super critical finishes, tight clearances and sharp metering edges. These surfaces and features are so easily damaged by handling that it would be very risky sending match fitted assemblies OP for passivation. No doubt some pieces would become damaged and then require lapping to rework.
Is it safe to say that if these types of components are operating in hydraulic fluids it's acceptable to lap the surfaces post passivation? Match fitted assemblies would be installed in the next level assembly fairly soon after being fitted. Individual components, prior to match fitting, may sit in stock for several days. In this case passivation would be beneficial to protect the components pre-match / lap fitting.
- Los Angeles, California, USA
July 23, 2013
A. Hydraulic fluids are corrosive in most situations. Corrosion inhibitors are probably contained in the hydraulic fluid in question, however, the effects of such additives sometimes do not add up to a hill of beans.
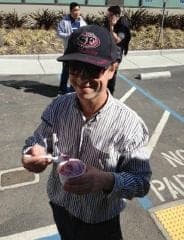
Blake Kneedler
Feather Hollow Eng. - Stockton, California
July 25, 2013
A. Hi Douglas,
We initially moved away from the passivation not because of the lapping afterwards, but for the fact the parts tend to be designed from 440C and we were frequently seeing the parts chewed up by the passivation process.
We have only been running parts like this for about 3 years, but as yet we have not seen any issues. The corrosion inhibitors used are pretty darned good in aerospace and defence hydraulic fluids.
If you are lapping the parts post passivation I see no problems, the parts will be running in hydraulic fluid and to be honest they are corrosion resisting steels so should have an inherent corrosion resistance anyway.
Aerospace - Yeovil, Somerset, UK
July 25, 2013
A. As the others have mentioned, passivation must be the absolute final process performed after all surface cutting, shaping, grinding, etc. are completed. If the combination of alloy and environment is such that corrosion isn't likely, then you can try it without passivation and see if the results are acceptable.
If passivation is deemed necessary, might I suggest an in-house citric acid based bath? I have spoken with many manufactures who switch to citric exactly for the reasons given, they have to do some last minute rework on some parts and don't want to send them out again to their passivation contractor because they can't wait that long, they don't want to pay further shipping costs, or they have had issues with the contractor damaging their parts. Even 440C can be managed in citric under the correct bath parameters.
adv.
Let us know if we can help.
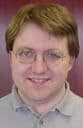
Ray Kremer
Stellar Solutions, Inc.

McHenry, Illinois
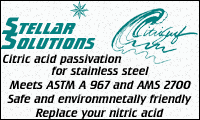
July 30, 2013
Q, A, or Comment on THIS thread -or- Start a NEW Thread