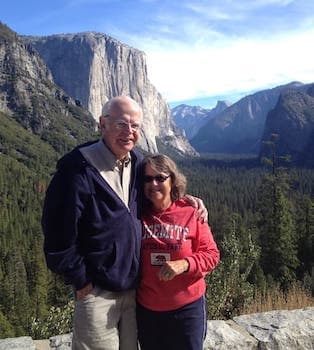
Curated with aloha by
Ted Mooney, P.E. RET
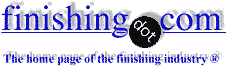
The authoritative public forum
for Metal Finishing 1989-2025
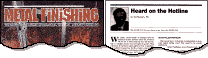
-----
Want technical know how for hot dip galvanising of bolts
April 29, 2009
Dear Sir,
I am already having a Hot Dip Galvanising unit in India but during the galvanising process on bolts I face a problem of Zinc deposit on Thread of the bolt . Kindly give me a detailed solution of the problem . Moreover Kindly also tell me that how in bulk quantity the bolts can be galvanised .
Thank you in anticipation
Director - Kanpur, Uttar Pradesh, India
First of two simultaneous responses --
Normally, you have to pay some one for their time to get a DETAILED answer.
James Watts- Navarre, Florida
May 1, 2009
Second of two simultaneous responses --
Sir:
What are the typical diameters and lengths of the bolts you wish to galvanize? Do you wish to spin these bolts? Some years ago I carefully investigated spin galvanizing with a small,clear plastic basket, white nylon bolts and water to determine how to spin galvanize. I also used a variable speed drill and dyes to determine how quickly the heat would distribute evenly in the basket and product. I video taped this work (4 hours, over a two year period). My conclusion is that 1,000 pounds of short, small diameter bolts can be done per basket giving 1,000,000 pounds/day if the kettle is properly designed thermally fired (a very deep kettle is required). Problem is that nobody is doing that many bolts or small items.
If you are interested in spin galvanizing there are many, many questions that need to be addressed including: Spin Type, e.g. centrifuge or "spin-a-batch;" Spin Power, air, hydraulic, or electric; Basket Type, mild, non-silicon steel or Haynes 556 alloy; Kettle Type, wet or dry; Quench, water-fall dump or basket immerse. There are at least a few hundred questions that need proper answers.
In the alternative, if you are galvanizing large and/or long bolts the methods are quite easy.
Regards,
Galvanizing Consultant - Hot Springs, South Dakota, USA
May 4, 2009
HDG of threaded components usually requires centrifuging. This can be done at standard temperature of about 450C, for larger components, but quite often at 550C (with a ceramic kettle) for smaller diameters.
The items are prepared in normal way, then immersed contained in a perforated bucket like container, which is attached to or placed quickly into a device to spin it. The spinning action centrifuges the surplus zinc leaving the threads relatively free of surplus.
The higher temperature work allows more time to centrifuge before solidification of the zinc.
External threads coated this way (e.g., bolts, stud bolts, etc.) still require either to be over cut themselves to fit a nut, or for the nut to be overcut. This allows for the extra thickness of the coating.
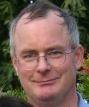
Geoff Crowley
Crithwood Ltd.
Westfield, Scotland, UK
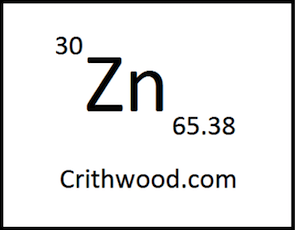
May 5, 2009
I saw somewhere (maybe a thread on this site, maybe somewhere else) the point made that bolts need to be overcut to allow for the galvanizing, but nuts are better galvanized as blanks then tapped correct size, since their threads will be fully protected when screwed onto the galvanized bolts. Avoid hassles with zinc being trapped in the nuts even though centrifuged.
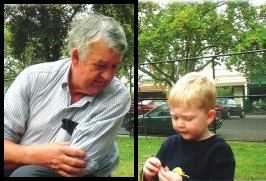
Bill Reynolds [deceased]
consultant metallurgist - Ballarat, Victoria, Australia
We sadly relate the news that Bill passed away on Jan. 29, 2010.
May 8, 2009
May 10, 2009
Dear Sir,
Can you give details on following so that I can help you.
1) What is the process you are doing right now.
2)What is the dipping load.
3)If you are centrifuging the product
what is the transfer time between bath and centrifuge.
What is the speed of centifuge.
4)what is the size of your bath and what is your dross percentage.
- Vizag, Andhra pradesh, INDIA
May 12, 2009
Thank you all for your invaluable advises . At presently I am using a wet kettle process for HDG . The dipping load at a time is 20-25 kgs . The size of the bolts I require to Galvanise is from 6.0mm to 20.0 mm dia & length is from 10.0mm to 150.0mm . I tried Galvanising the bolts by putting approximately 20.0 kgs bolts in perforated mild steel basket & then immersing them in the wet type galvanising tank after pre treatment of bolts . The basket was then immersed directly in the water tank. kindly give a detailed process of centrifuging .
Arvinder Singh- Kanpur, Uttar Pradesh , INDIA
Sir:
Your bolts are small and the best way to do them is likely by centrifuge. In this process the bolts are loaded into a circular perforated basket (holes just the bottom are okay to help allow the bolts to slide out later: holes just in the bottom are much better for nails) and then lowered into the zinc (wet or dry kettle) and usually bounced up-and-down in the zinc until "cooked out." Next the basked is put into a "dumper" and then raised and dumped like a water-fall into water. After withdrawing from the zinc this process must be relatively rapid.
In the USA one centrifuge mfg is "Barrett" and I think they may have 5 or 10 hp electric motor driven devices. Some people think the best centrifuge is hydraulically driven because the torque is greater and can attain a high rotation rate more quickly. Most of the zinc is tossed off in a fraction of a second. A weak electric or air driven motor, because it takes too long to attain rotation speed does not work properly. The final rotation speed need not be great.
I suspect there may be another way to do these small bolts which can best be described as a vibrating perforated table. I have never seen such a device, it is only a rumor.
Regards,
Galvanizing Consultant - Hot Springs, South Dakota, USA
May 14, 2009
Dear Mr Cook,
Thanks for your reply. Kindly clarify what you exactly mean by dumper
. Is it a hot oven in which the perforated basket has to rotate after
" cook out" of bolts or is it something else. Kindly also mention the final speed in terms of RPM of the perforated basket at the time of centrifuging.
Thanks
- Kanpur, Uttar Pradesh, India
May 19, 2009
May 22, 2009
Sir:
The "dumper" is standard equipment into which the spin basket is placed just after removal from the kettle and raises off the floor
(turning over in the process) and then dumping the product into the quench water. A hook on the dumper prevents the spin basket from falling into the quench water. The crane is then attached to the bail of the spin basket away from the hook side and the spin basket withdrawn and allowed to stay hot for the next product. The dumper is not heated except for the spin baskets and product going through.
While at a spin plant I asked about RPM and the operator said that he did better at the 500 RPM than 1,000 RPM, likely because the 500 was achieved more quickly. The bearings on the centrifuge were 4 inches diameter and shielded to prevent damage from the molten zinc. I believe that the minimum electric spinner horsepower should be 10 HP, also you need a very, very good brake to stop the spinner. Hydraulic spinning is likely better due to the higher torque (based on a pump-up pressure chamber between loads), however precautions must be adequate to prevent the high pressure hoses from bursting and burning down the plant (which has happened).
There are several reasons why a galvanizer gets into the spinning business, including the price for product which is usually 3 to 5 times greater than hanging wire product. Also a galvanizer may have clients for structural product who also want to bolt these structures together.
I caution you that I have seen many, many "homemade" spinners which were "junk" and produced junk product that did not produce acceptable threads. I also have seen a fair number of commercial spinners that were not well made and did not produce good product.
I consider spin galvanizing about 20 times more difficult as compared with wired or hooked hanging product. I spent two years studying spin galvanizing by using clear plastic baskets and a 4 liter clear beaker. The result was 4 hours of video tape which clearly shows how to spin galvanize 1,000,000 pounds of small product/year. I also developed "spin express" which works extremely well for thin spin work and for work with "wings."
Hopefully I am not encouraging you to "homebuild" a junk spinner. I will not continue to give information on your project.
Regards, Dr. Thomas H. Cook, Hot Springs, South Dakota, USA
Galvanizing Consultant - Hot Springs, South Dakota, USA

Q, A, or Comment on THIS thread -or- Start a NEW Thread