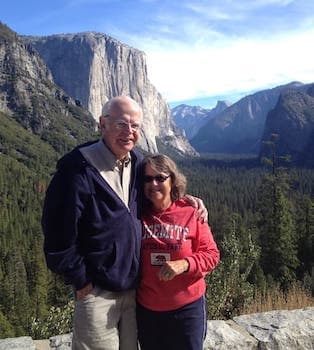
Curated with aloha by
Ted Mooney, P.E. RET
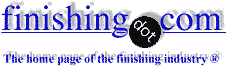
The authoritative public forum
for Metal Finishing 1989-2025
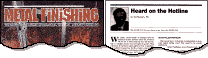
-----
Best surface treatment for a running mate against 54 Rc. TIN surface component
April 28, 2009
I am using a TIN surfaced tool steel (H-13), hardened to 54 Rc. as a wear surface and am looking for the best material and treatment possible for it's running mate.
The force exerted between these two running components is 1000 PSI over an area of about one square inch, stroking about an inch in length.
I need to know what material, hardness, and overall treatment would give the best wear and gall resistance over one million strokes.
Am looking for expert opinions or a qualified reference or technical paper please, as this
involves an investment of time and money on my part and it's hard to come by either lately.
Certainly the lowest cost is always in mind, but will appreciate all viewpoints.
Best regards,
Tool and Die maker - Chicago, IL.
Hi, Ken. Teflon and the like might extrude out at that pressure. I think hardened steel without a coating may be the best running mate if there is lubrication. If not, sintered bronze might be good.
Regards,
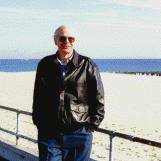
Ted Mooney, P.E.
Striving to live Aloha
finishing.com - Pine Beach, New Jersey
April 28, 2009
First of two simultaneous responses --
If you are using lubrication, you want a very highly-polished steel for the other surface. If not, you might want to consider a solid lubricant coating, such as diamond-like carbon or molybdenum
(or tungsten) disulfide.
Why did you choose TiN? Other PVD coatings are more lubricious. The pairing for bearings that is known to work well is highly-polished steel against a PVD-deposited metal-containing diamond-like carbon
(Timken). NASA likes very thin nickel-containing moly-disulfide on its bearings for space applications, where you can't use any lubricants.
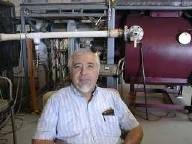
Jim Treglio - scwineryreview.com
PVD Consultant & Wine Lover
San Diego, California
May 1, 2009
Second of two simultaneous responses --
If it were my project, I would look into teflon impregnated EN, or low phos hardened EN (both 0.0015 or so thick). Hard chrome, about 0.004" thick should also work. If done very well, it should not require grinding for flatness.
Some kind of lubrication, regardless of the material, would help a lot.
- Navarre, Florida
May 1, 2009
Close consideration should also be given to the final finish and roughness of the mating surfaces, more so if the application is non-lubricated. When solid surfaces rub against each other, the nominal or average exerted pressure is rather meaningless. In a microscopic level, the protrusions of each surface are in fact taking the contact load which may be orders of magnitude higher. In this respect I fully agree with Ted's recommendation; bronze acts as a sacrificial material. Good luck. G. Marrufo-Mold Finish
Guillermo Marrufo- Monterrey, Mexico
May 4, 2009
Q, A, or Comment on THIS thread -or- Start a NEW Thread