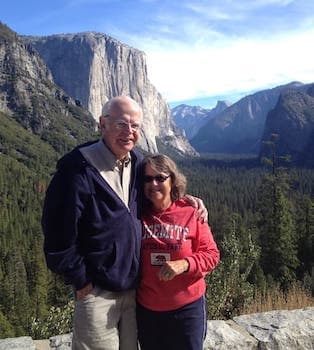
Curated with aloha by
Ted Mooney, P.E. RET
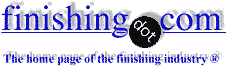
The authoritative public forum
for Metal Finishing 1989-2025
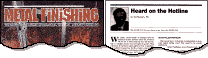
-----
Trouble Plating Very Thin Tin Films
2000
Q. Hi, I'm a grad student working on my Masters Thesis. I'm trying to electroplate very thin (~10 Angstrom) Sn on a copper substrate. Ideally I'd like it to be ductile but most importantly I want it to be very smooth while covering the copper entirely. I'm using the following bath:
- 60g/L SnSo4
- 40g/L H2SO4
- 40g/L Phenolsulfonic acid
- 2g/L Gelatin
- 1g/L Beta-Naphthol
My substrate is 28cm^2 and I usually run at 1mA/cm^2. I use a Titanium Anode that is not "bagged". I'm afraid I don't understand the concept or need for a bagged anode? I prepare the foil by cleaning it with acetone ⇦ this on eBay or Amazon [affil links] Warning! highly Flammable! and then soaking in 1:1 HCl for a minute. I can get a nice Sn plate if I make it thick enough, but this is not my goal. When I try for a 10 Angstrom layer I get spots of Sn with poor coverage on the Cu. Also, the plate is very porous and water logged. Water content in the plate is detrimental to my research. I can rid myself of it by heating under Argon but that is one more step I'd rather not have. Thanks in advance!
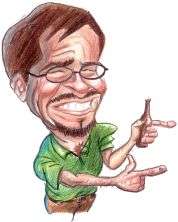
Shane Beattie
research scientist - Halifax, Nova Scotia, Canada
A. Hello Shane,
I think you've got a really tough problem here! The tin will be ductile and have good adherence, but 10 angstroms is very thin. What does your copper substrate look like before you plate it? I use electropolishing after acetone ⇦ this on eBay or Amazon [affil links] Warning! highly Flammable! to prepare my copper substrates and it does not leave them perfectly flat. I suspect the HCl will also attack some areas slightly more than others plus how flat is the substrate before cleaning. With out a perfectly flat substrate initial deposition will be on favoured sites.
Also reading my reference books tin has an atomic radius of 1.5 angstroms, so your looking for 6-7 atoms deep. The water I think is present on the copper (nooks and crannies) and not held in the tin layer. I'm dealing with thicker layers so I find hot air drying sufficient, if you had total coverage it could be sufficient for you too.
As to bagging, you don't need to worry about it, industrially consumable anodes are used, placed in bags (not sure if tin plating anodes use this). Usually in acid tin (which you are using) tin anodes are used, but as your not going to be taking many tin-ions out of solution you might not have to worry about using tin anodes. Possibly you could be forming tin(IV) at the anode, which could throw your calculations out. Maybe up the current density too, 10 mA/cm2 might work better. Hope I've been some help. Ian
Ian Brookeuniversity - Glasgow, Scotland
2000
Thanks for your advice Ian, you bring up some very good points I hadn't considered. Most papers I read about Tin plating suggest electropolishing, so I think I'll have to start doing that.
My readings suggest that Tin binds strongly to ligands, and has a hard time riding itself of them while it's plating, I think this is how the water is getting in. A major concern of mine is the leveling agent I'm using. Though I agree the copper substrate is far from flat, I was hoping that the leveling agents would compensate for that and give nice, smooth, thin Tin, but obviously they aren't. Ideally I'd like to try a different plating recipe with a much better leveler. A paper I'm reading now suggests N,N-bis(tetraoxyethylene) octadeclyamine and benzyl acetone, but I can't seem to find a company that supplies the first one.
I don't see how upping the current density will help me. Intuitively it seems that a slower current density will yield a smoother plate, since the deposited atoms have more time to migrate along the surface to find a valley rather than being confined to where they initially plated out, no doubt a mountain.
Shane Beattieresearch scientist - Halifax, Nova Scotia, Canada
2000
A. 10 angstroms sounds like an application for a PVD or CVD process. I would guess that some department in the university has the means and equipment to do this for you.
Dale Woika- Bellefonte, Pennsylvania
2000
Q. I have an optical application which requires depositing a thin layer (~300 nm) of either copper or tin on a flat non-conducting part ~4 m x 0.5 m. The tolerance on the layer thickness is ~±20 nm.
I'm assuming that electroplating would be unlikely to achieve the tolerance because getting a sufficiently uniform electric field over that area would be virtually impossible.
Would this be possible with an electroless process? Presumably being a much slower process, the build-up can be better controlled and the bath well agitated / mixed to ensure the chemical concentration and temperature are uniform.
Thanks
Product designer - Edinburgh, Lothian, UK
March 1, 2012
A. That is a very tight tolerance. Straight electrolytic will never get it, even with shields and thieves. pulsed periodic reverse might be able to achieve it, but you could spend a lifetime finding the right window.
Electroless stands a possibility. Talk to tech services of the vendors of the solutions.
One of the many types of physical vapor deposition might work, but there are not that many contractors that can handle your large part and do it well.
- Navarre, Florida
First of two simultaneous responses -- March 2, 2012
A. Go PVD!
Daniel Hernandez- Bucaramanga Santander Colombia
Second of two simultaneous responses -- March 2, 2012
A. David,
I am new to the forum and came across your post while browsing through the forums. You mentioned that you are trying to deposit thin metal on a "non-conductive" surface. That means, electroplating is out of the question! As for electroless plating, you could try but depending on the type of substrate, adhesion may become a big issue. As someone else pointed out, PVD seems to be your best bet.
Good luck.
-Niranjan.
- WESTBOROUGH, MASSACHUSETTS, USA
March 20, 2012
Q, A, or Comment on THIS thread -or- Start a NEW Thread